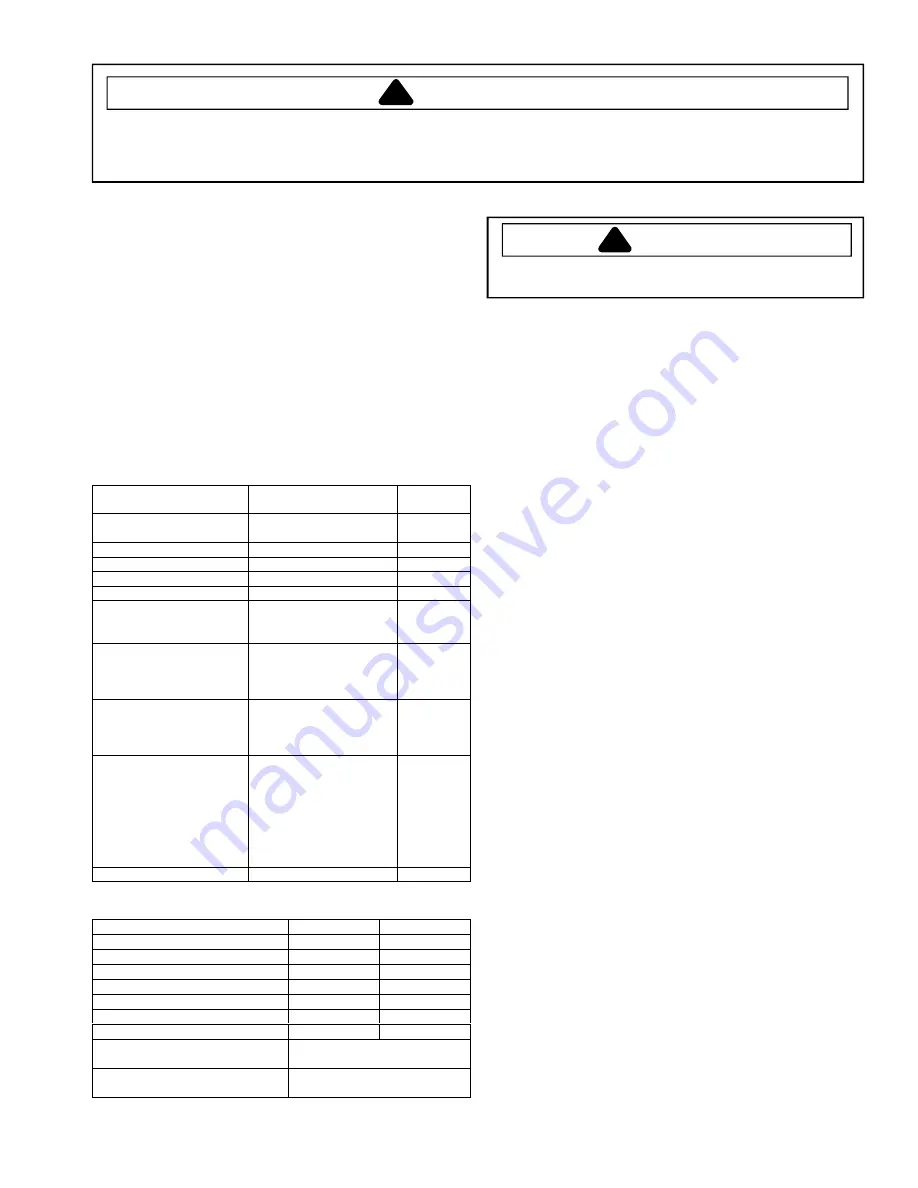
35
RS5280001 Rev. 0
To minimize contamination, exercise extreme care
when servicing HFC134A sealed systems.
•
No trace of other refrigerants is allowed in HFC134a
systems. Chlorinated molecules in other refrigerants
such as CFC12, etc. will lead to capillary tube
plugging.
•
Ester oil is used in HFC134a systems. Do not use
mineral oil. HFC134a and mineral oils cannot be
mixed. If mineral oils were used in HFC134a systems,
lubricant would not return to compressor and would
cause early compressor failure. If significant amount
of oil has been lost from compressor, replace oil
rather than adding oil.
• Ester oils used in HFC134a systems are so
hydroscopic that by the time an inadequate system
performance is detected, oil will be saturated with
moisture.
• CFC12 has much higher tolerance to system
processing materials, such as drawing compounds,
rust inhibitors, and cleaning compounds, than
HFC134a. Such materials are not soluble in HFC134a
systems. If materials were to be washed from system
surfaces by ester oils, they could accumulate and
eventually plug capillary tube.
• Care must be taken to minimize moisture entering
HFC134a system. Do not leave compressor or system
open to atmosphere for more than 10 minutes.
Excessive moisture in HFC134a system will react with
compressor oil and generate acid.
• Compressor must be replaced when performing low
side leak repair.
•
Drier filter must always be replaced with service drier
filter, part #B2150504.
Important:
Unbrazing drier filter from tubing will drive
moisture from desiccant and into system, causing
acids to form. Do not unbraze filter drier from tubing.
If CFC12 service drier was installed in HFC134A
system, drier could overload due to excessive
moisture.
• HFC134a compatible copper tubing, part #R0174075
(6.35mm O.D. X 457mm length) and part #R0174076
(7.24mm O.D. X 610mm length) must be used when
replacing tubing.
• Avoid system contamination by using Towerdraw E610
evaporating oil, part # R0157532, when flaring,
swagging, or cutting refrigeration tubing.
Service Procedures
HFC134a Service Information
HFC134a is alternative refrigerant for CFC12.
HFC134a has an ozone depletion potential (ODP)
factor of 0.0 and a global warming potential (GWP)
factor of 0.27. HFC134a is not flammable and has
acceptable toxicity levels. HFC134a is not
interchangeable with CFC12. There are significant
differences between HFC134a and CFC12 which
must be considered when handling and processing
refrigeration system.
Health, Safety, and Handling
Health, safety and handling considerations for
HFC134A are virtually no different than those for
CFC12.
Comparison of CFC12 and HFC134a Properties
Health, Safety, and
Handling
CFC12
HFC134a
Allowable overall
exposure limit
1,000 ppm
Same
Vapor exposure to skin
No effect
Same
Liquid exposure to skin
Can cause frostbite
Same
Vapor exposure to eye
Very slight eye irritant
Same
Liquid exposure to eye
Can cause frostbit
Same
Above minimum exposure
limit
Can cause Asphyxiation,
Tachycardia, and Cardia
Arrhythmias
Same
Safety and handling
Wear appropriate skin
and eye protection. Use
with adequate
ventilation.
Same
Spill management
Remove or extinguish
ignition or combustion
sources. Evacuate or
ventilate area.
Same
Fire explosion hazards
May decompose if
contact with flames and
heating elements.
Container may explode
if heated due to resulting
pressure rise.
Combustion products
are toxic.
Same
Disposal procedures
Recycle or reclaim.
Same
Properties/Characteristics
CFC12
HFC134a
Ozone Depletion Potential (ODP)
1.0*
0.0*
Global Warming Potential (GPW)
3.2*
0.27*
Molecular weight
121
102
Boiling point at 1 atmosphere
-22°F (-30°C)
-15°F (-126°C)
Vapor pressure at 77°F (25°C)
80 psig
82 psig
Liquid density at 77°F (25°C)
82 lb/ft
3
75 lb/ft
3
Flammability
No
No
High-side system operating
Pressure at 65°F (18°C)
HFC134a approximately 3 psig
higher than CFC12
Low-side system operating
Pressure at 65°F (18°C)
HFC134a approximately 2 psig
lower than CFC12
To avoid risk of electrical shock, personal injury, or death, disconnect electrical power source to unit, unless test
procedures require power to be connected. Discharge capacitor through a 10,000 ohm resistor before attempting
to service. Ensure all earthing wires are connected before certifying unit as repaired and/or operational.
!
WARNING
CAUTION
!