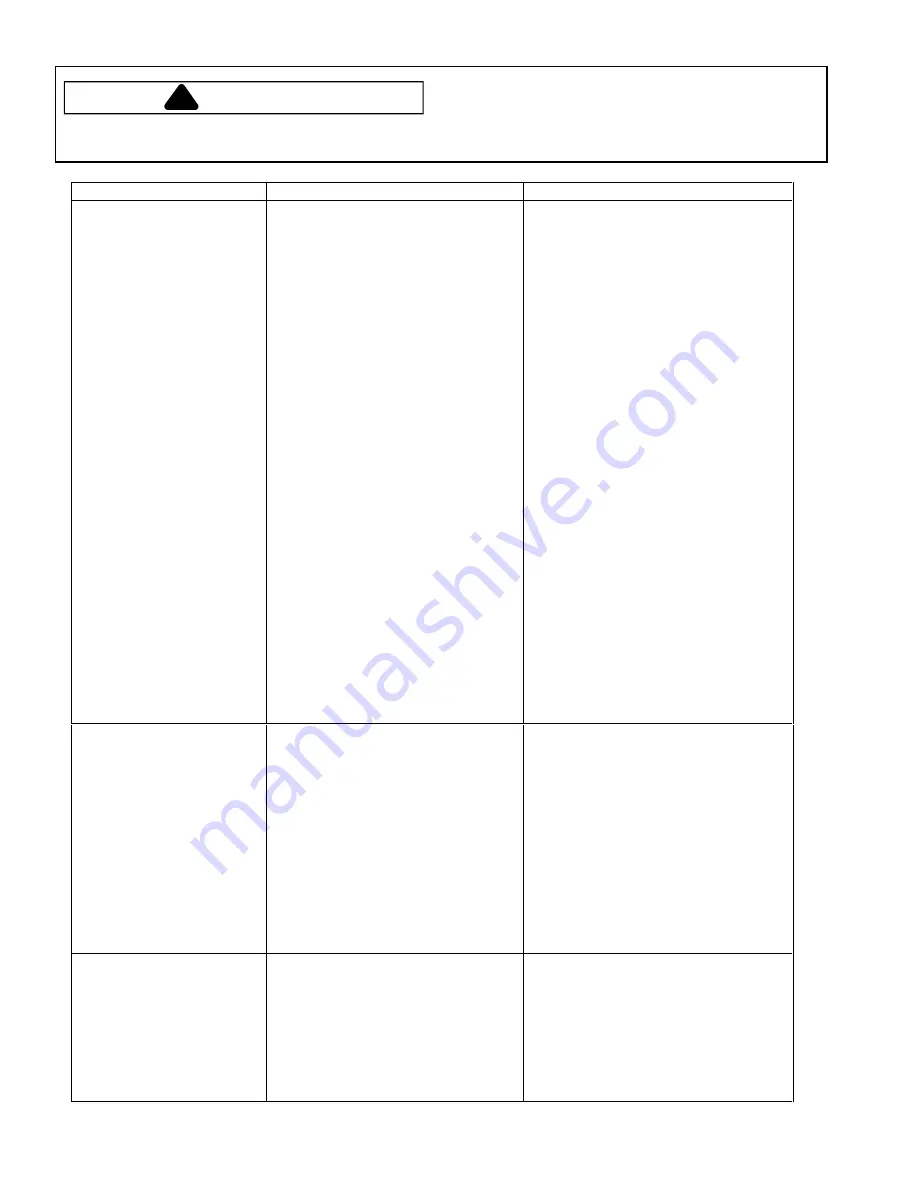
RS1500000 Rev. 0
24
Troubleshooting
To avoid risk electrical shock, personal injury, or death,
always disconnect electrical power source to the freezer
before attempting to service, unless test procedures require
power to be connected. When removing any wiring from terminals they must be replaced on the same terminals.
Ensure all ground wires are connected before certifying unit as repaired and/or operational.
WARNING
!
Problems
Possible Causes
Correction
Compressor runs but
freezer temperature is
higher than
necessary
Temperature control
Misadjusted or out of calibration
Failed
Freezer fan motor (no-frost only)
AC circuit to fan motor open
Failed
Excessive load of unfrozen food
Door Seal
Poor seal
Failed
Loss of sealed system charge
Timer stuck in defrost
Partial restriction
Frost build-up on freezer coil (over
1/2 inch thick (12.7 mm))
Separation of heat exchanger
Adjust control
Replace
See wiring diagram and check circuit
Replace
Advise customer to freeze no more
than 10% of freezer capacity at one
time
Adjust door & gasket as instructed
under improving gasket seal
Replace
Locate and repair leak. Evacuate
undercharge system proper amount
of refrigerant
Replace
Locate and repair restriction.
Evacuate and recharge system with
proper amount of refrigerant
Check door seal. If not Frost Free
model, advise customer to defrost
every time frost builds up to almost 1”
thick (25 mm)
Install heat exchanger repair kit.
Compressor does not run
and no light
No power at AC outlet
Failed fuse
Failed outlet
Line cord
Disconnect
Failed
Open machine compartment wiring
harness
Two simultaneous problems-light
bulb out and open AC circuit to
compressor
Replace
Advise customer to replace
Plug-in line cord to AC outlet
Replace
See wiring diagram and check circuit
Replace light bulb. See wiring
diagram and check circuit
Sweating but freezer is
working normally
otherwise
Exterior sweating
Void in insulation
Overcharged
Defective door seal
Add insulation inside the affected
area, if possible
Evacuate and recharge system with
right amount of refrigerant. See
specification chart
Replace