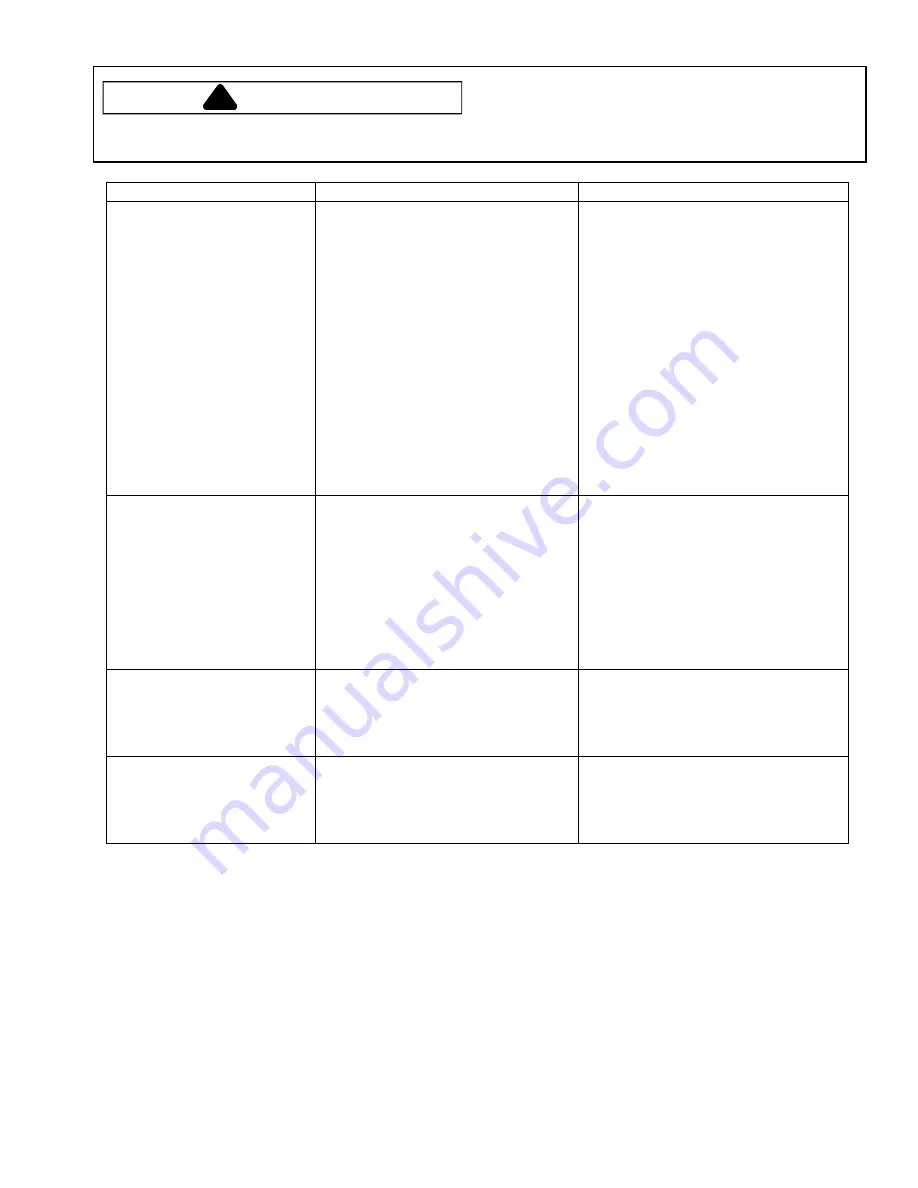
25
RS1500000 Rev.0
Troubleshooting
To avoid risk electrical shock, personal injury, or death,
always disconnect electrical power source to the freezer
before attempting to service, unless test procedures require
power to be connected. When removing any wiring from terminals they must be replaced on the same terminals.
Ensure all ground wires are connected before certifying unit as repaired and/or operational.
WARNING
!
Problems
Possible Causes
Correction
Compressor runs, but short
cycles
Temperature control
Improper setting of temperature
control for prevailing environmental
and usage conditions
Failed
Low Voltage
Overload protector failed
Excessive load of unfrozen food at
one time
Loose electrical connections
Refer to ”CHECKING OPERATING
TEMPERATURES and reset for
proper setting
Replace
Check voltage-must be at least 100 of
moment of start time, with all other
loads on the line
Replace
Advise customer to freeze no more
than 10% of freezer capacity at one
time
Locate and fix loose connections
Compressor runs but does
not freeze
Complete loss of sealed system
charge(Low Wattage Readings)
Restricted capillary or drier (Low
wattage readings while running). Will
cycle on overload when unit tries to
come on after having been shut off
and restriction still present
Compressor defective
Locate and repair leaks before re-
charging with refrigerant
Refer to operating pressure and
wattage’s replace failed parts
Replace
Compressor runs
excessively Freezer too cold
Temperature control
Misadjusted
Feeler tube not touching freezer
shelf
Failed
Adjust control for normal operation
Install control feeler tube to sense
proper temperature
Replace
Defrost water disposal
problem
Water frozen in drain trough (Failed
defrost timer, radiant heater or
thermostat on No Frost Models Only)
Restriction in drain system
Check and replace defective part or
parts
Clean drain system