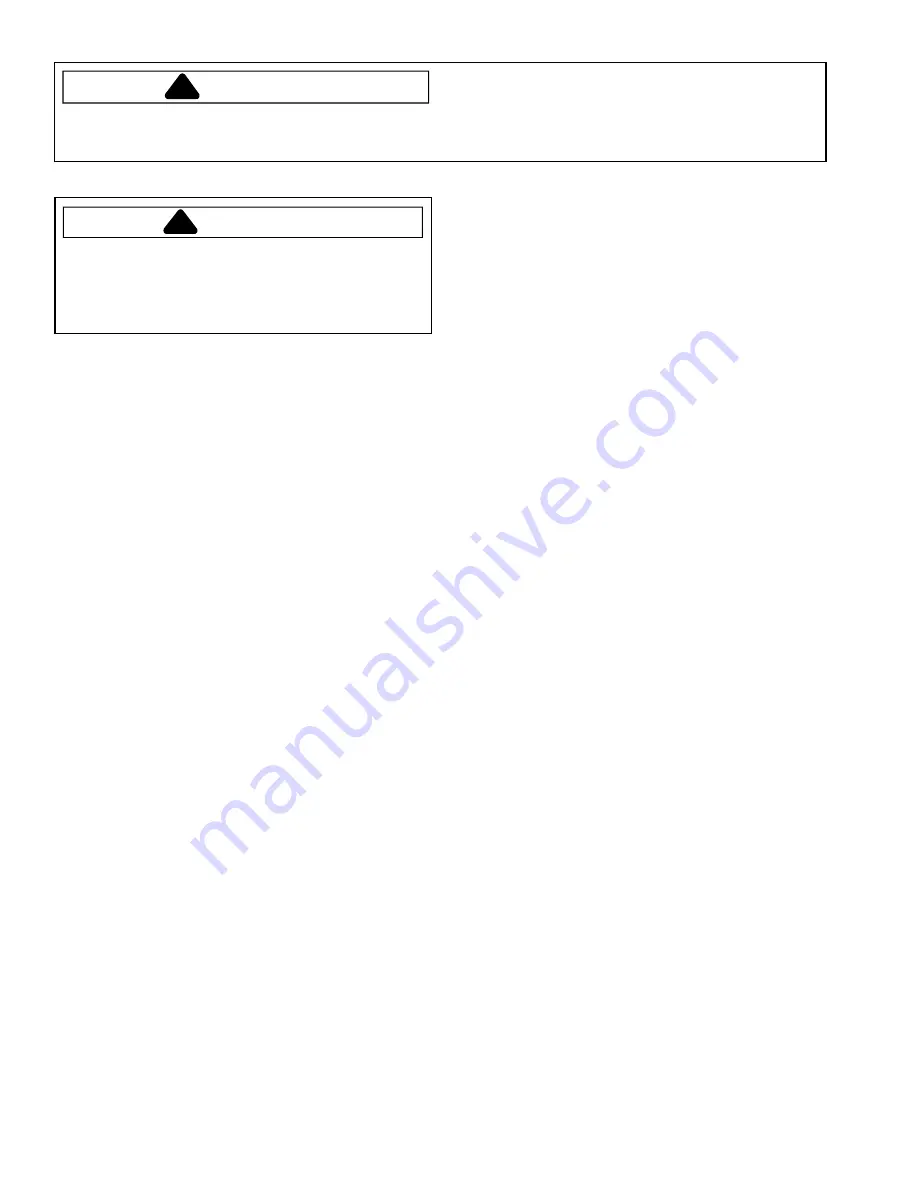
RS1500000 Rev. 0
44
Service Information
To avoid risk of electrical shock, personal injury, or death,
always disconnect electrical power source to the freezer
before attempting to service unless test procedures require power to be connected. When removing any wiring from
terminals, replace on the same terminals. Ensure all ground wires are connected before certifying unit as repaired
and/or operational.
WARNING
!
Service Equipment
CAUTION
!
Service equipment for HFC134a systems must be
used exclusively with HFC134a refrigerant. Do not use
this equipment to service devices using other types of
refrigerant (for example, CFC12 or CFC22
refrigerants).
Listed below are the tools and equipment needed for
proper servicing of HFC134a systems.
NOTE:
Once equipment is designated for HFC134a
use, it must be exclusively use for HFC134a
only. An
*
will identify the following equipment.
* Evacuation pump
Check with vacuum pump
supplier to verify equipment is compatible for
HFC134a. Robinair, Model 15600, 2 stage, 170 liters
(6 cubic feet) per minute pump is recommended.
* Four-way manifold gauge set with low loss quick
couplers
Leak detector
* Charging cylinder
* Line piercing saddle valve
Seals must be
HFC134a and ester oil compatible. Line piercing
valves may be used for diagnosis but are not suitable
for evacuation or charging, due to minute holes
pierced in tubing. Do not leave mechanical access
valves on system. Valves eventually will leak.
Molecules of HFC134a are smaller than other
refrigerants and will leak where other refrigerants
would not.
* Swaging tools
* Flaring tools
* Tubing cutter
Flux
Sil-Fos
Silver solder
* Oil for swaging and flaring
* Copper tubing
Dry nitrogen
99.5% minimum purity, with -40°C (-40°F) or lower
dew point
Crimp tool
Tube bender
Micron vacuum gauge
* Process tube adaptor kit
Heat trap paste
* Appliance grade HFC134a
Drier Replacement
Before opening sealed system, recover HFC134a
refrigerant for safe disposal.
Every time sealed HFC134a system is repaired, drier
filter must be replaced. Cut drier out of system by
completing the following steps. Do not unbraze drier
filter. Applying heat to remove drier will allow moisture
into system.
1. Score capillary tube close to drier and break.
2. Reform inlet tube to drier allowing enough space for
large tube cutter.
3. Cut circumference of drier 1-1/4" (3.175 cm), below
condenser inlet tube joint to drier.
4. Remove drier.
5. Unbraze remaining part of drier. Remove drier from
system.
6. Discard drier in safe place. Do not leave drier with
customer.