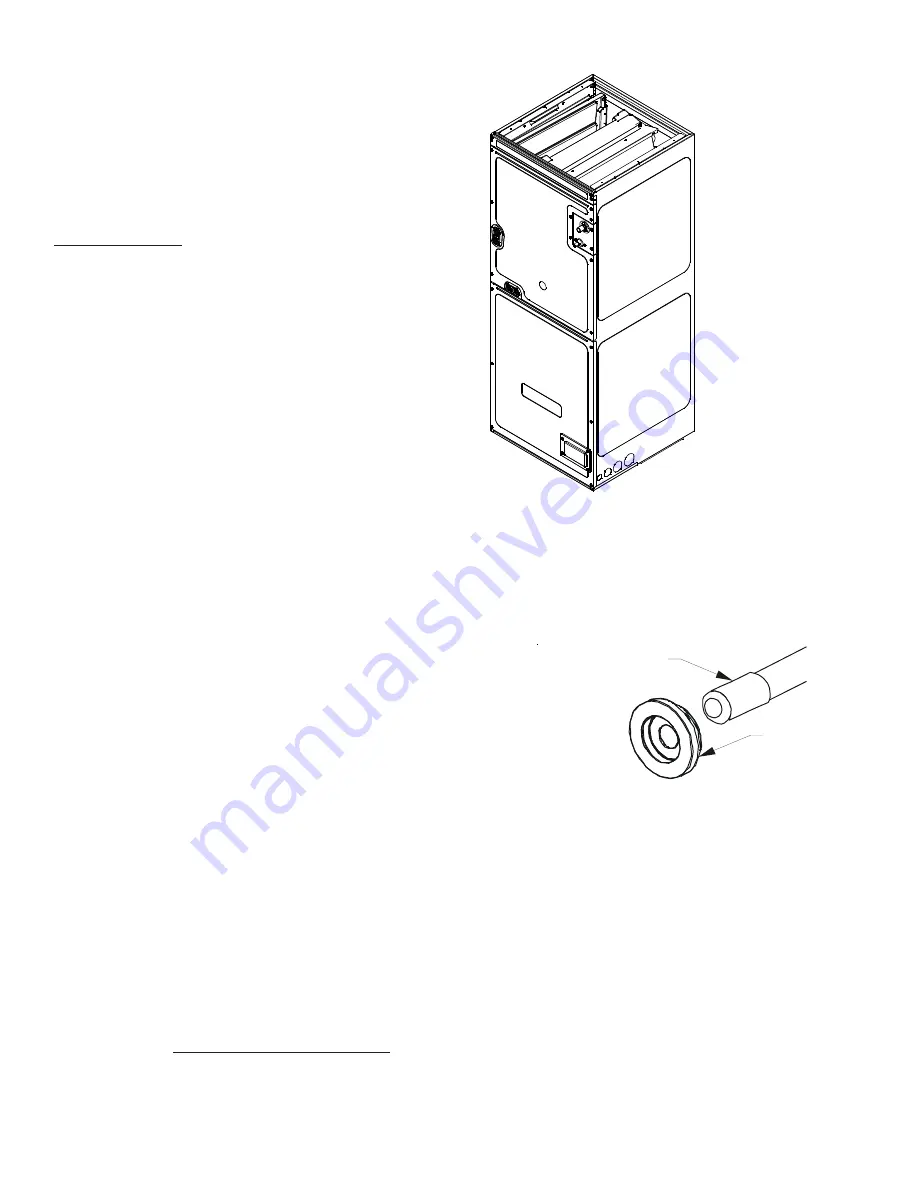
8
6. Insert suction line set into suction tube expansion and
slide insulation and grommet about 18" away from braze
joint.
7. Braze joints. Quench all brazed joints with water or a
wet rag upon completion of brazing.
8. Replace access panels, suction line grommet, insulation
and all screws.
NOTE:
The use of a heat shield is strongly recommended when
brazing to avoid burning the serial plate or the finish of the unit.
Heat trap or wet rags must be used to protect heat sensitive com-
ponents such as service valves, electronic expansion valve (EEV),
thermistors and pressure sensors.
8 CONDENSATE DRAIN LINES
The coil drain pan has a primary and a secondary drain with 3/4"
NPT female connections. The connectors required are 3/4" NPT
male, either PVC or metal pipe, and should be hand tightened to a
torque of no more than 37 in-lbs. to prevent damage to the drain
pan connection. An insertion depth of approximately 3/8” to 1/2”
(3-5 turns) should be expected at this torque.
1. Ensure drain pan hole is not obstructed.
2. To prevent potential sweating and dripping on to finished
space, it may be necessary to insulate the condensate drain
line located inside the building. Use Armaflex
®
or similar ma-
terial.
A secondary condensate drain connection has been provided for
areas where the building codes require it. Pitch all drain lines a
minimum of 1/4" per foot to provide free drainage. Provide re-
quired support to the drain line to prevent bowing. If the second-
ary drain line is required, run the line separately from the primary
drain and end it where condensate discharge can be easily seen.
NOTE:
Water coming from secondary line means the coil primary
drain is plugged and needs immediate attention.
Insulate drain lines located inside the building or above a finished
living space to prevent sweating. Install a condensate trap to en-
sure proper drainage.
NOTE:
When units are installed above ceilings, or in other loca-
tions where damage from condensate overflow may occur, it is
MANDATORY
to install a field fabricated auxiliary drain pan un-
der the coil cabinet enclosure.
The installation must include a “P” style trap that is located as
close as is practical to the evaporator coil. See Figure 12
for de-
tails of a typical condensate line “P” trap.
NOTE: Units operating in high static pressure applications may
require a deeper field constructed “P” style trap than is shown in
Figure 12 to allow proper drainage and prevent condensate
overflow.
NOTE:
Trapped lines are required by many local codes. In the
absence of any prevailing local codes, please refer to the require-
ments listed in the Uniform Mechanical Building Code.
RUBBER
GROMMET
SUCTION LINE
WITH SPIN CLOSURE
SUCTION LINE GROMMET
Figure 11
ACCESS PANEL
CONFIGURATION FOR
DOWNFLOW
OR HORIZONTAL RIGHT
Figure 10
A drain trap in a
draw-through
application prevents air from
being drawn back through the drain line during fan operation
thus preventing condensate from draining, and if connected to a
sewer line to prevent sewer gases from being drawn into the air-
stream during blower operation.
Use of a condensate removal pump is permitted when necessary.
This condensate pump should have provisions for shutting off
the control voltage should a blocked drain occur. See Auxiliary
Alarm Switch section for more details. A trap must be installed
between the unit and the condensate pump.
IMPORTANT NOTE:
The evaporator coil is fabricated with oils
that may dissolve styrofoam and certain types of plastics.
Therefore, a removal pump or float switch must not contain any
of these materials.