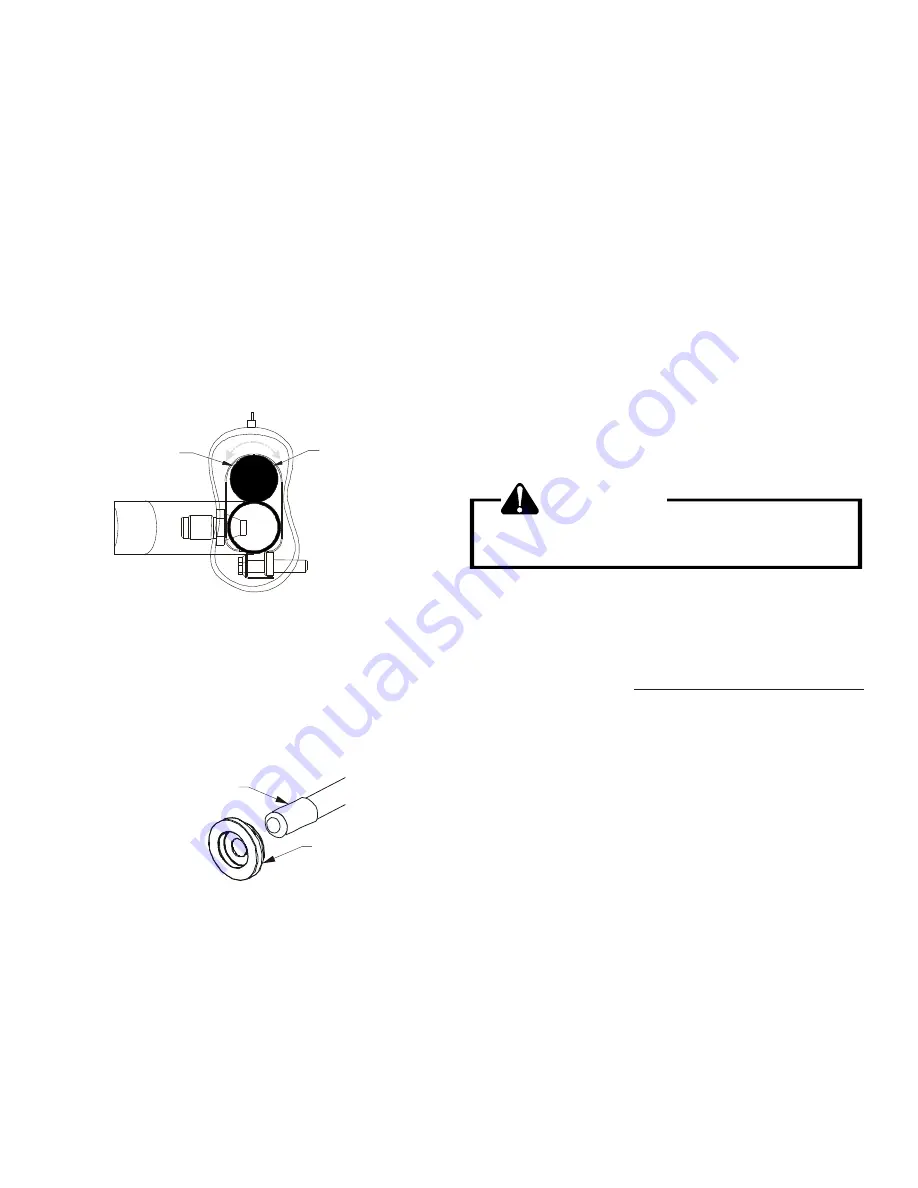
7
1. Remove refrigerant tubing panel or coil (lower) access
panel.
2. Remove access valve fitting cap and depress the valve
stem in access fitting to release pressure. No pressure
indicates possible leak.
3. Replace the refrigerant tubing panel.
4. Remove the spin closure on both the liquid and suction
tubes using a tubing cutter.
5. Insert liquid line set into liquid tube expansion and slide
grommet about 18" away from braze joint.
6. Insert suction line set into suction tube expansion and
slide insulation and grommet about 18" away from braze
joint.
7. Braze joints. Quench all brazed joints with water or a
wet rag upon completion of brazing.
REFRIGERANT BULB
MUST BE POSITIONED
BETWEEN 10 & 2 O’CLOCK
REFRIGERANT BULB
MUST BE POSITIONED
BETWEEN 10 & 2 O’CLOCK
Figure 10
NOTE: The sensing bulb must be permanently located. A
heat shield, heat trap, or wet rag must be used during braz-
ing to prevent damage to the TXV valve.
8. Replace access panels, suction line grommet, insulation
and all screws.
RUBBER
GROMMET
SUCTION LINE
WITH SPIN CLOSURE
Suction Line Grommet
Figure 11
8
Condensate Drain Lines
The coil drain pan has a primary and a secondary drain with
3/4" NPT female connections. The connectors required are
3/4" NPT male, either PVC or metal pipe, and should be hand
tightened to a torque of no more than 37 in-lbs. to prevent
damage to the drain pan connection. An insertion depth of
approximately 3/8” to 1/2” (3-5 turns) should be expected at
this torque.
1. Ensure drain pan hole is not obstructed.
2. To prevent potential sweating and dripping on to finished
space, it may be necessary to insulate the condensate
drain line located inside the building. Use Armaflex
®
or
similar material.
A secondary condensate drain connection has been provided
for areas where the building codes require it. Pitch all drain
lines a minimum of 1/4" per foot to provide free drainage.
Provide required support to the drain line to prevent bowing.
If the secondary drain line is required, run the line separately
from the primary drain and end it where condensate discharge
can be easily seen.
NOTE:
Water coming from secondary line means the coil
primary drain is plugged and needs immediate attention.
Insulate drain lines located inside the building or above a
finished living space to prevent sweating. Install a conden-
sate trap to ensure proper drainage.
NOTE:
When units are installed above ceilings, or in other
locations where damage from condensate overflow may
occur, it is
MANDATORY
to install a field fabricated auxiliary
drain pan under the coil cabinet enclosure.
CAUTION
If secondary drain is not installed, the secondary
access must be plugged.
The installation must include a “P” style trap that is located
as close as is practical to the evaporator coil. See
Figure 12
for details of a typical condensate line “P” trap.
NOTE:
Trapped lines are required by many local codes. In
the absence of any prevailing local codes, please refer to the
requirements listed in the Uniform Mechanical Building Code.
A drain trap in a
draw-through
application prevents air from
being drawn back through the drain line during fan operation
thus preventing condensate from draining, and if connected
to a sewer line to prevent sewer gases from being drawn into
the airstream during blower operation.
Field experience has shown condensate drain traps with an
open vertical Tee between the air handler and the conden-
sate drain trap can improve condensate drainage in some
applications, but may cause excessive air discharge out of
the open Tee. Goodman
®
does not prohibit this type of drain
but we also do not recommend it due to the resulting air leak-
age. Regardless of the condensate drain design used, it is
the installer’s responsibility to ensure the condensate drain
system is of sufficient design to ensure proper condensate
removal from the coil drain pan.