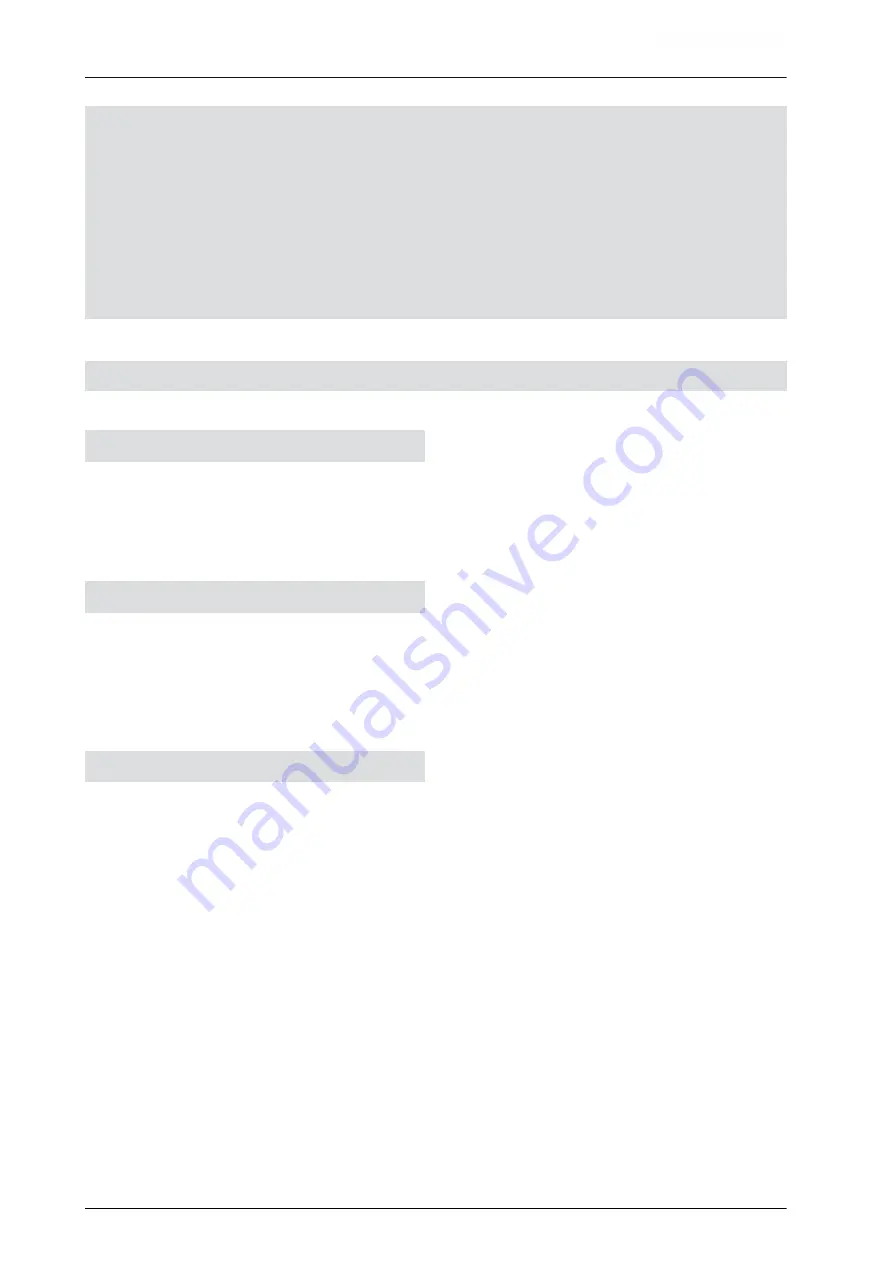
Directories
13
13.1 Glossary
CMS-T-00000513-B.1
M
Machine
Mounted implements are accessory parts of the
tractor. However, mounted implements are always
referred to as the implement in this operating manual.
O
Operating materials
Operating materials serve to ensure operational
readiness. Operating materials include e.g. cleaning
agents and lubricants such as lubricating oil, greases
or cleaners.
T
Tractor
In this operating manual, the designation tractor is
always used, even for other agricultural tractor units.
Implements are mounted on the tractor or towed by
the tractor.
13 | Directories
MG7508-EN-GB | B.1 | 31.08.2022 | © AMAZONE
148