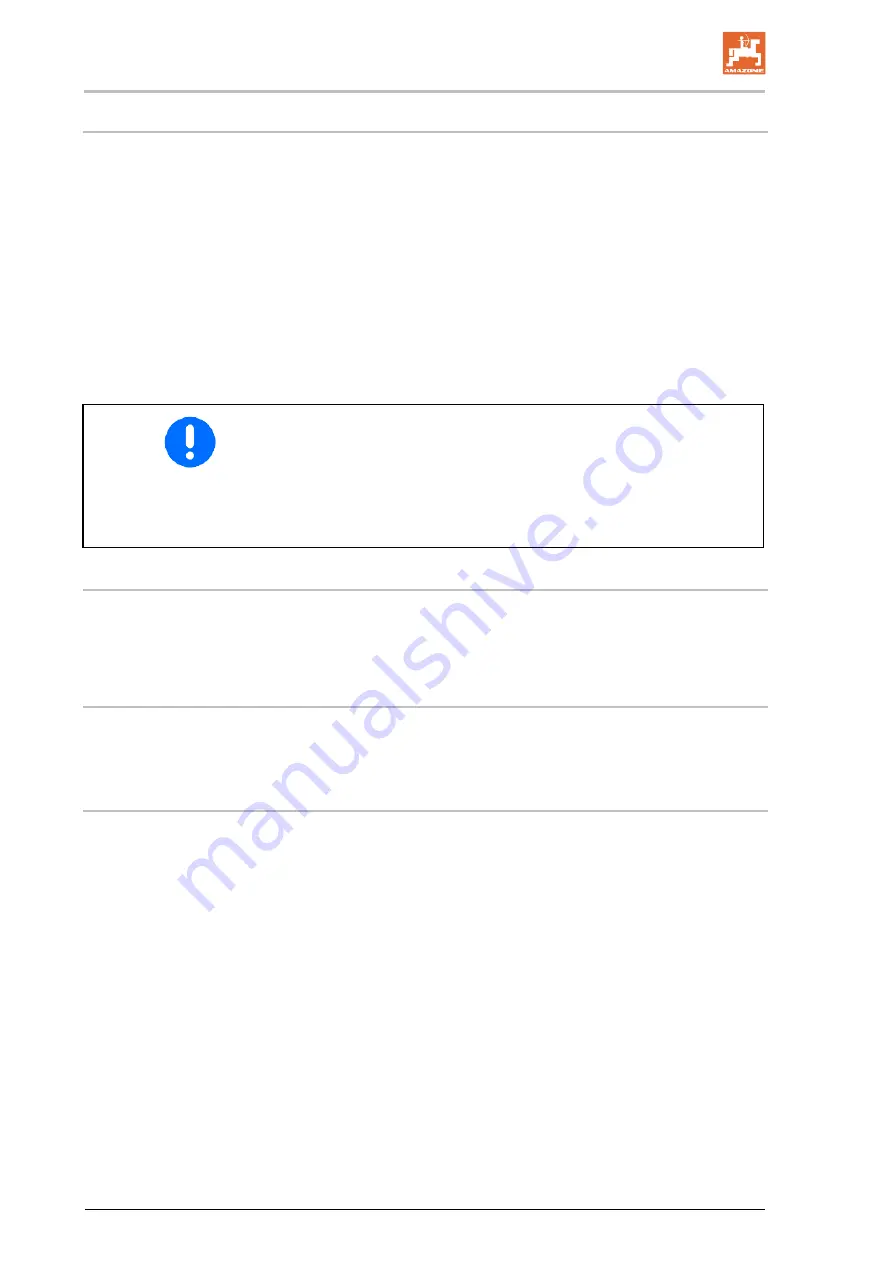
General safety instructions
12
ZG-
B
BAG0170.2 02.21
2.3
Organisational measures
The operator must provide the necessary personal protective equip-
ment as per the information provided by the manufacturer of the crop
protection agent to be used, such as:
•
Chemical-resistant gloves,
•
Chemical-resistant overalls,
•
Water-resistant footwear,
•
A face mask,
•
Breathing protection,
•
Safety glasses,
•
Skin protection agents, etc.
The operating manual
•
Must always be kept at the place at which the machine is oper-
ated.
•
Must always be easily accessible for the operator and mainte-
nance personnel.
Check all the available safety equipment regularly.
2.4
Safety and protection equipment
Before each commissioning of the machine, all the safety and protec-
tion equipment must be properly attached and fully functional. Check
all the safety and protection equipment regularly.
Faulty safety equipment
Faulty or disassembled safety and protection equipment can lead to
dangerous situations.
2.5
Informal safety measures
As well as all the safety information in this operating manual, comply
with the general, national regulations pertaining to accident prevention
and environmental protection.
When driving on public roads and routes, then you should comply with
the statutory road traffic regulations.
Summary of Contents for ZG-B 8200 Truck
Page 97: ...Hydraulic diagram ZG B BAG0170 2 02 21 97 ...
Page 98: ......