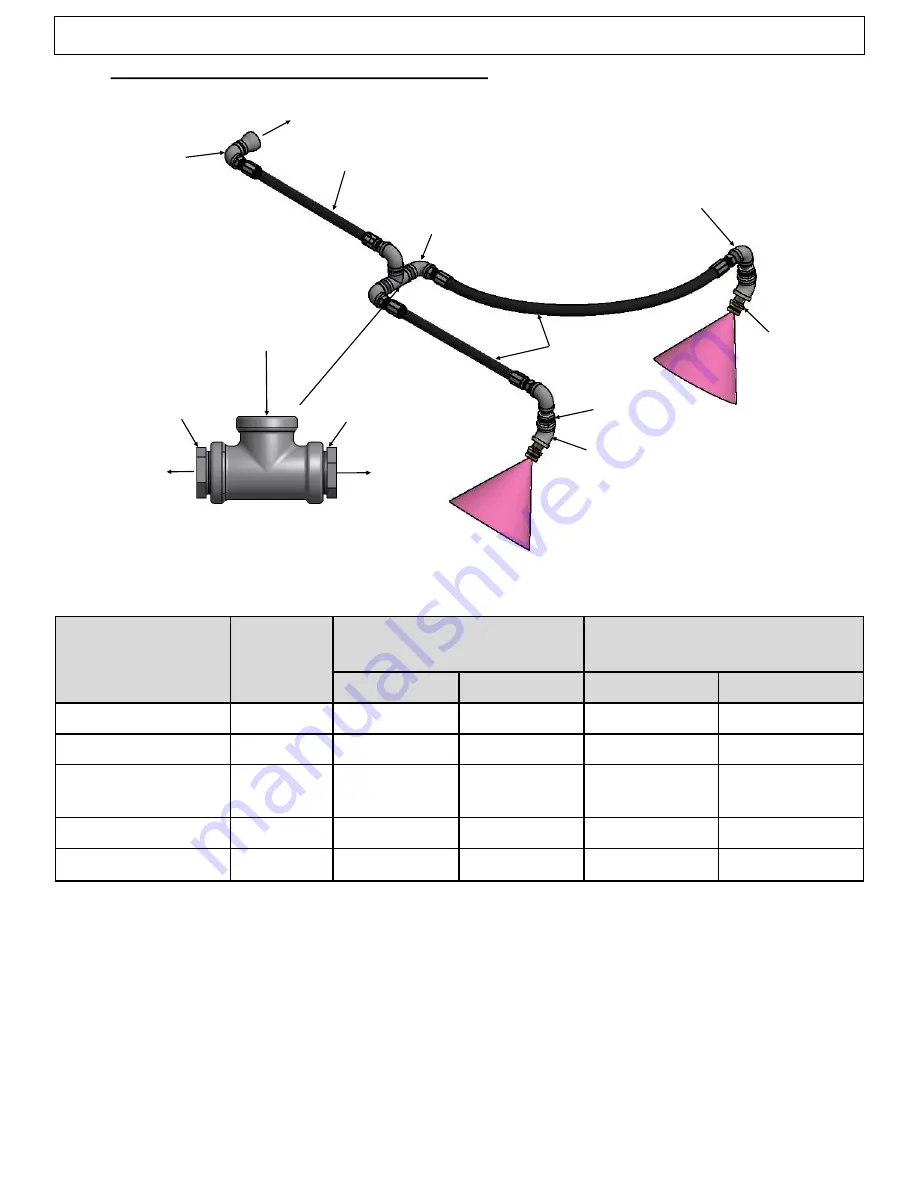
32
HELIX™ Manual
(P/N 26291)
Chapter 3: System Design
Rev A (February 2018)
HELIX™ PCU
Fire Suppression System
LOCATION
HOSE I.D.
in (mm)
HOSE LENGTH
ft (m)
NUMBER OF ELBOWS PER
SECTION OF HOSE
MAXIMUM
MINIMUM
MAXIMUM
MINIMUM
Cylinder to T1
3/4 (19.1)
45 (13.7)
5 (1.5)
2
0
T1 to each Nozzle
1/2 (12.7)
15 (4.6)
—
2*
0
Cylinder to any
Nozzle
—
60 (18.3)
5 (1.5)
—
—
All 1/2” hose
—
30 (9.1)
—
—
—
All 3/4” hose
—
45 (13.7)
5 (1.5)
—
—
Table 3.4.1
Note:
Hose length may be unbalanced in a maximum ratio of 3:1 where the Agent Distribution
Network splits (T1 to Nozzle). However, this ratio must be observed for the minimum versus
maximum hose length. Example: If the longest 1/2 inch I.D. hose leading from where the network
splits (T1 to Nozzle) is 15 feet, the shortest 1/2 inch I.D. hose leading from the same network split
location cannot be less than 5 feet, and all 1/2 inch I.D. hoses together must fall within the length
specified.
3.4.1 HX25 Agent Distribution Network (2 Nozzle)
Figure 3.4.1
1/2” I.D. HOSE
1/2” ELBOW
(TYP)
1/2” ELBOW
3/4” ELBOW
(OPTIONAL)
3/4” I.D. HOSE
T1* = 3/4” NPT TEE
TO NOZZLE
TO NOZZLE
3/4”
-
1/2” NPT
REDUCER
3/4”
-
1/2” NPT
FROM AGENT
CYLINDER
TO DISCHARGE FITTING KIT
(P/N 10199
-
R)
T1*
NOZZLE
(P/N 26330)
QUIK SEAL
(P/N 14204)
1/2” 45° ELBOW
(TYP)
*Not including 45° elbow used at nozzle