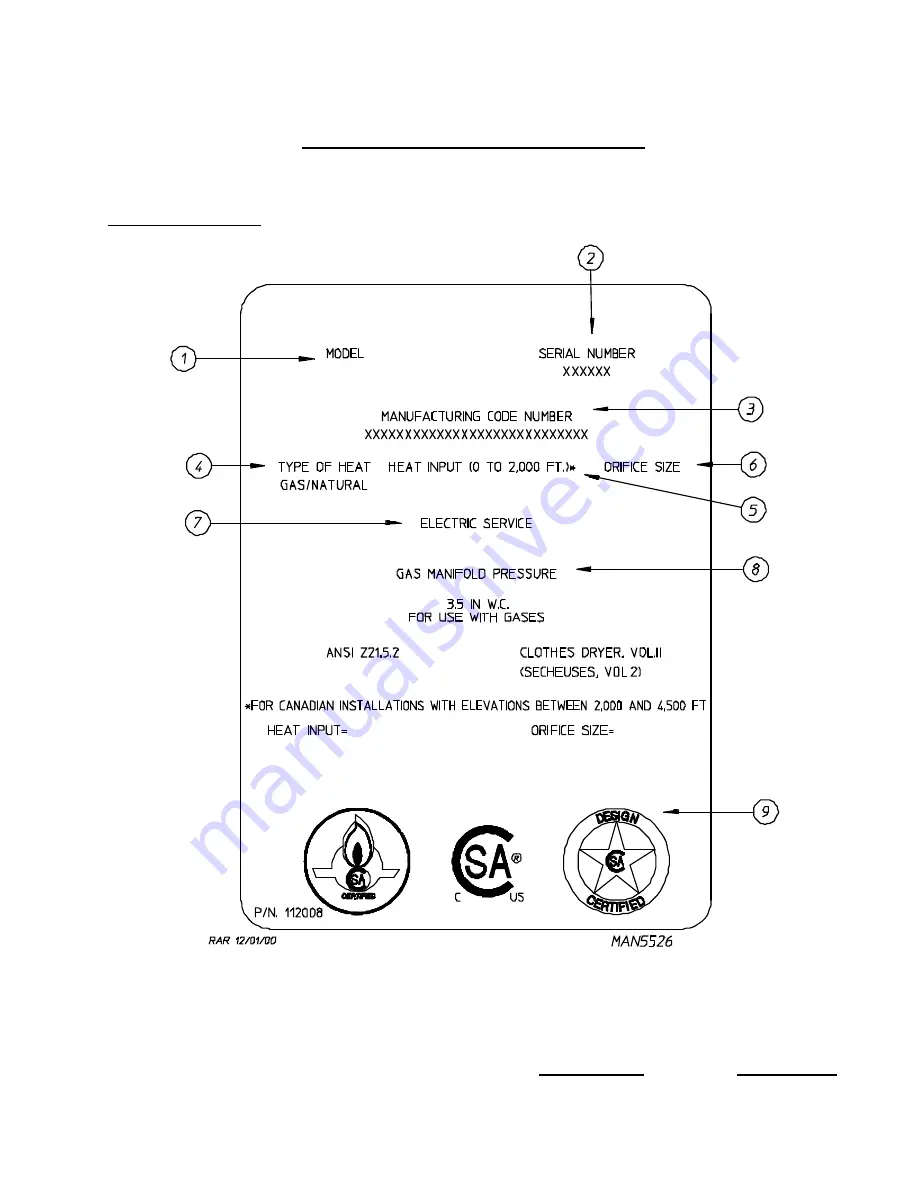
47
SECTION VIII
DATA LABEL INFORMATION
A. DATA LABEL
When contacting
American Dryer Corporation
, certain information is required to insure proper service/parts
information from
ADC
. This information is on the data label that is affixed to the left side panel area behind the
top control (access) door. When contacting
ADC
please have the
model number
as well as the
serial number
readily available.
Summary of Contents for ID-170
Page 25: ...21 ...
Page 55: ...ADC 113331 1 08 27 01 25 ...