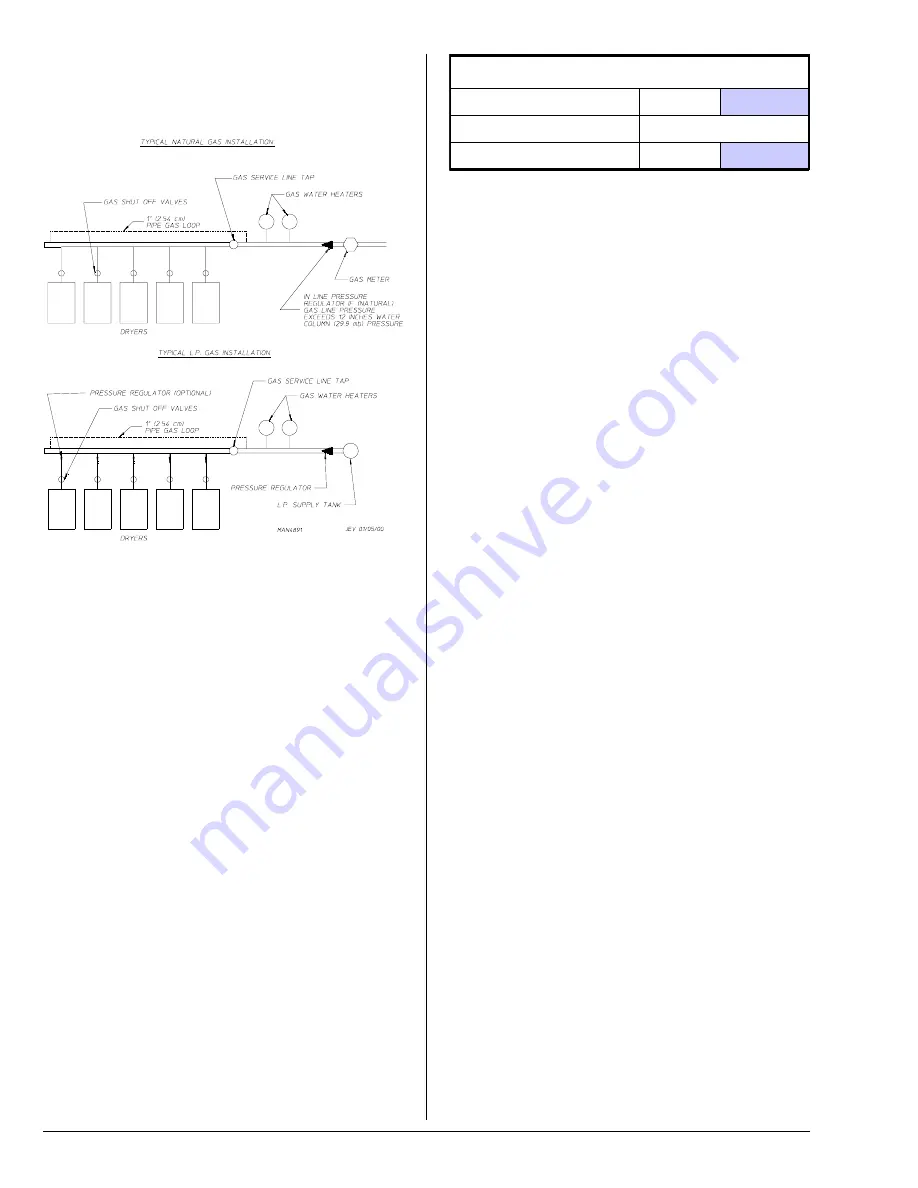
18
American Dryer Corp.
113335 - 12
NOTE: The dryer must be isolated from the gas supply
piping system by closing its individual manual shutoff valve
during any pressure testing of the gas supply piping
system at test pressures equal to or less than 1/2 psig (3.5
kPa).
Steam Information ____________________
It is your responsibility to have all steam plumbing connections
made by a qualified professional to ensure that the installation
is adequate and conforms to local and state regulations or
codes.
IMPORTANT: Failure to comply with the requirements
stipulated in this manual can result in component failure,
which will void the warranty.
NOTE: The dryer is manufactured with a pneumatic
(piston) damper system, which requires an external supply
of clean, dry, and regulated air of 0.75 cfh (0.02 cmh) @ 80
psi +/- 10 psi (5.51 bar +/- 0.68 bar). Refer to Steam
Damper Air System Connections on the following page.
Steam Coil pH Level
The normal pH level for copper type steam coils must be
maintained between a value of 8.5 to 9.5. For steel type
steam coils the pH level must be maintained between a value
of 9.5 to 10.5. These limits are set to limit the acid attack of
the steam coils.
IMPORTANT: Coil failure due to improper pH level will void
the warranty.
Steam Requirements, High Pressure
Inlet .................... 1-1/4” supply line connection
qty. 1 at top manifold.
Return ................ 1-1/4” return line connection
qty. 1 at bottom manifold.
Operating Steam Pressure
Maximum
125 psig
*
862.84 kPa
Heat Input (Normal Load)
13
Bhp
Consumption (Approximate)
450 lb/hr
202.2 kg/hr
Shaded areas are stated in metric equivalents
* The minimum operating pressure for optimum results is 100 psig (689.47
kPa).
Installation Instructions
To ensure that an adequate supply of steam is provided, be
sure that the steam supply lines and steam return lines are
sized and laid out as stipulated in this manual. Inadequate
steam supply and steam return lines or improper steam
plumbing will result in poor performance and can cause
component failure. Clean, dry, and regulated steam must be
provided to the dryer.
IMPORTANT: Steam coil failure due to water hammer by
wet steam will void the warranty.
The pressure of the condensate in the steam supply line will
cause water hammer and subsequent heat exchanger (steam
coil) failure. The steam supply connection into the main
supply line must be made within a minimum 12-inch (30.48
cm) riser. This will prevent any condensate from draining
towards the dryer.
The steam supply line to the dryer must include a 12-inch
(30.48 cm) riser along with a drip trap and check valve. This
will prevent any condensate from entering the steam coil.
Flexible hoses or couplings must be used. The dryer vibrates
slightly when it runs and this will cause the steam coil
connections to crack if they are hard piped to the supply and
return mains.
Shutoff valves for each dryer should be installed in the supply,
return, and drip trap return lines. This will allow the dryer to
be isolated from the supply and return mains if the dryer needs
maintenance work.
Install an inverted bucket steam trap and check valve for
each unit at least 12-inch (30.48 cm) below steam coil as
close to the coil as possible.
A trap with a capacity of 1,200 lb (544 kg) of condensate per
hour at 125 psi (8.61 bar) is needed for each unit.
A 3/4-inch (19.05 mm) vacuum breaker should be installed
for each unit in the piping. This will prevent the condensing
steam from causing a vacuum inside the coil and possibly
damaging the coil.
Dryers with optional solenoid valve must be mounted with
coil positioned directly above the valve body.
The supply and return lines should be insulated. This will
save energy and provide safety for the operator and
maintenance personnel.
Water pockets in the supply line, caused by low points, will
provide wet steam to the coil possibly causing coil damage.
All horizontal runs of steam supply piping should be pitched
1/4-inch (6.35 mm) for every 1 foot (0.31 meters) back towards
the steam supply header causing any condensate in the line
to drain to the header. Install a bypass trap in any low point
to eliminate wet steam.