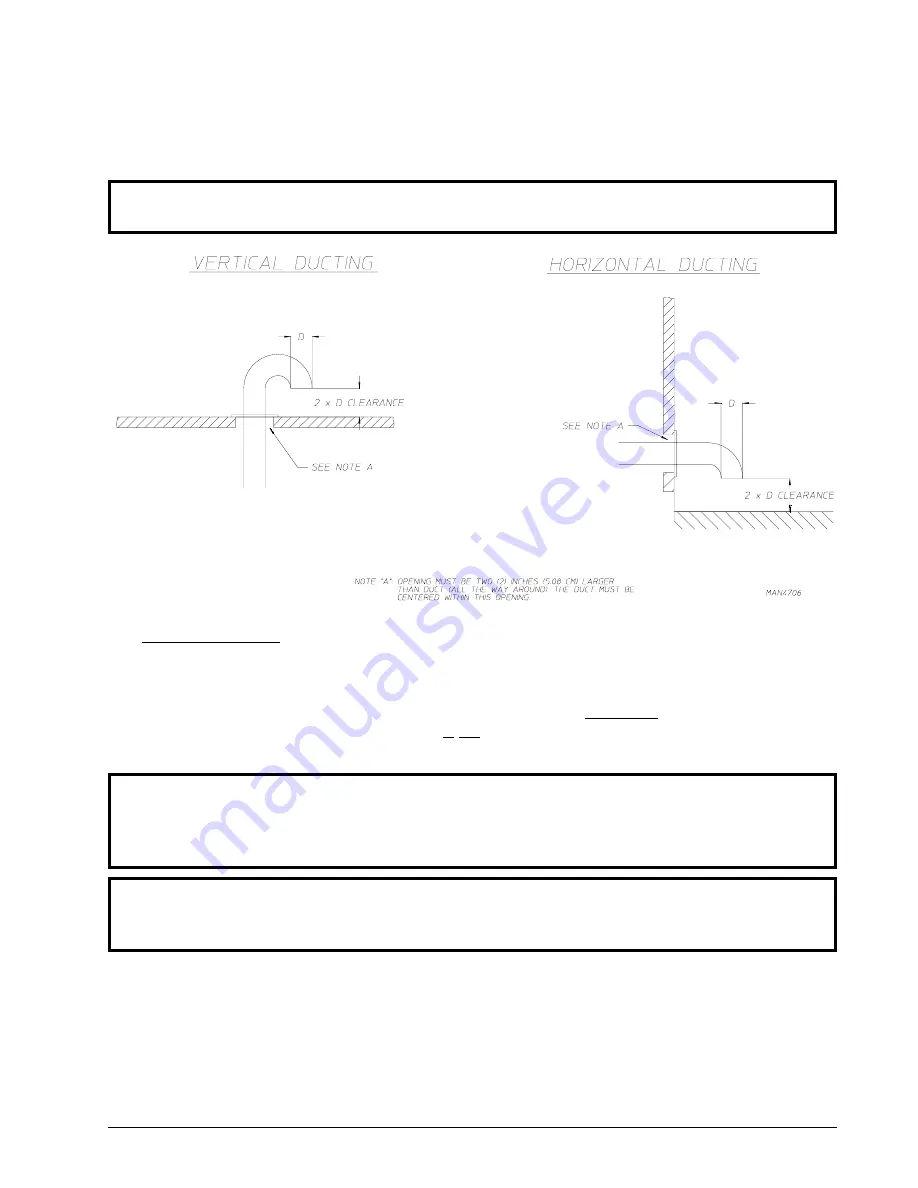
113344 - 9
www.amdry.com
13
2. Single Dryer Venting
When possible, it is suggested to provide a separate exhaust duct for each dryer. The exhaust duct
should
be
laid out in such a way that the ductwork travels as directly as possible to the outdoors with as few turns
as possible. It is suggested that the use of 90° turns in the ducting be avoided; use 30° and/or 45° angles
instead. The shape of the exhaust ductwork is not critical as long as the minimum cross section area is
provided.
IMPORTANT:
For a dryer that is vented horizontally, the minimum duct size for a gas dryer is
14-inches (35.56 cm) for a round duct or 12-1/2” (31.75 cm) for a square duct.
THE DUCT SIZE
MUST NOT BE
REDUCED ANYWHERE
DOWNSTREAM OF THE DRYER
.
IMPORTANT:
Exhaust back pressure measured by a manometer at each basket (tumbler) exhaust
duct area
must be
no less than 0 and
must not exceed
0.3 inches (0.74 mb) of water
column (W.C.).
It is suggested that the ductwork from each dryer not exceed 15 feet (4.57 meters) with no more than two
(2) elbows (excluding dryer connections and outside exhaust outlets). If the ductwork exceeds 15 feet
(4.57 meters) or has numerous elbows, the cross section area of the ductwork
must be
increased in
proportion to the length and number of elbows in it. In calculating duct size, the cross section area of a
square or rectangular duct
must be
increased by twenty percent (20%) for each additional 15 feet
(4.57 meters). The diameter of a round exhaust duct
should be
increased ten percent (10%) for each
additional 15 feet (4.57 meters). Each 90º elbow is equivalent to an additional 30 feet (9.14 meters), and
each 45º elbow is equivalent to an additional 15 feet (4.57 meters).
Outside Ductwork Protection
To protect the outside end of the horizontal ductwork from the weather, a 90º elbow bent downward
should
be
installed where the exhaust exits the building. If the ductwork travels vertically up through the roof, it
should be
protected from the weather by using a 180º turn to point the opening downward. In either case,
allow at least twice the diameter of the duct opening and the nearest obstruction.
IMPORTANT:
DO NOT
use screens, louvers, or caps on the outside opening of the exhaust
ductwork.