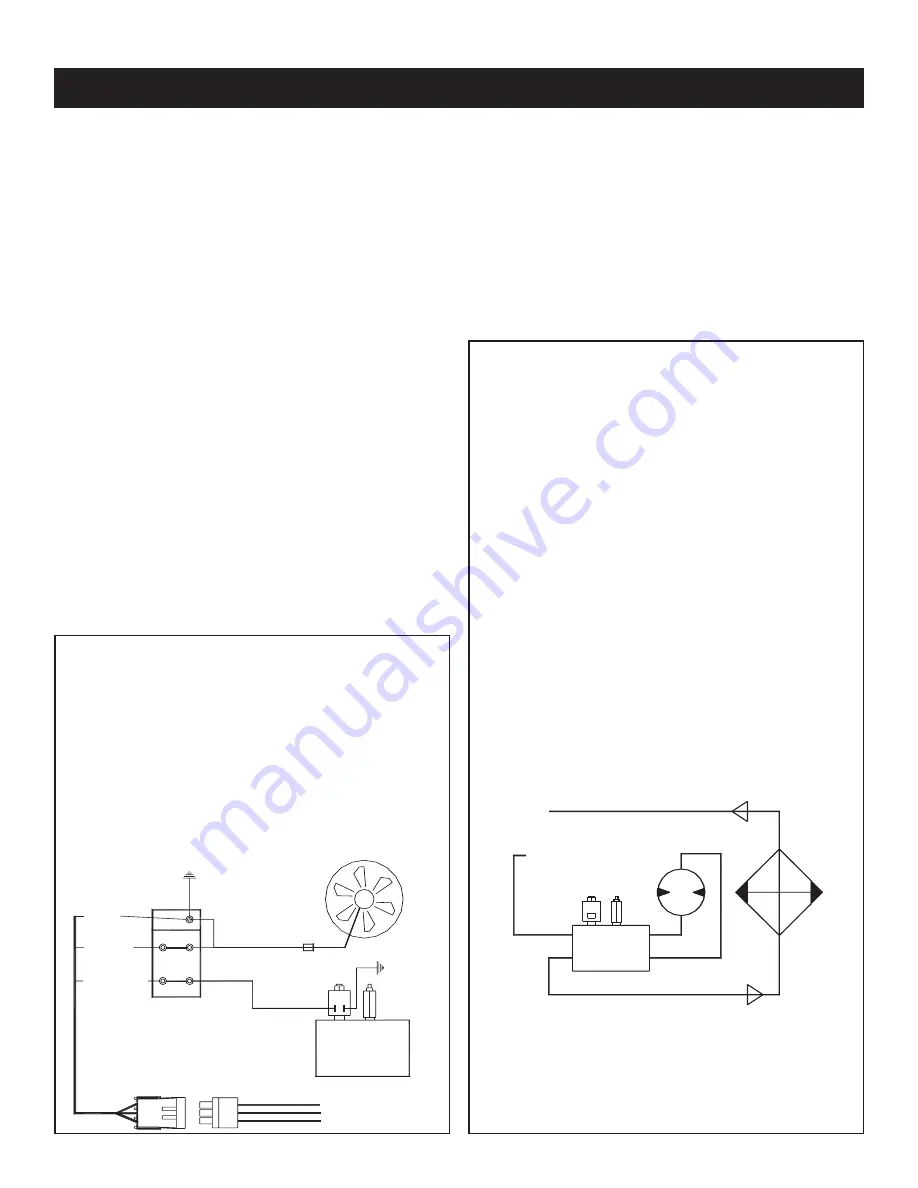
6
Class 3 Compressor Owner’s Manual
Return Line
Pressure
Line
FAN
GND
CPRSR
SPD CTRL
PRESSURE
SWITCH
LINE
MOTOR
HYDRAULIC
MANIFOLD
COMPRESSOR (12V INPUT)
GROUND
SPEED CONTROL
C
B
A
C
B
A
SHD-43 Installation
Pump Assembly:
The pump assembly may either be installed directly
on the PTO or as an optional method, may be
driven by a driveline from the PTO. Pump
manufacturers provide specific installation
information for their products and should be
consulted if questions arise.
PTO Assembly:
Check with the PTO manufactures representative
for specific instructions regarding your particular
make, model, and year of vehicle. As some trucks
may require modification of the transmission cross
member and the exhaust system, the
manufacturer’s instructions should be followed to
insure proper installation of the PTO.
Compressor Assembly:
Prepare the mounting location of the compressor
by locating and drilling four (4) holes, 7/16”
diameter as per the mounting pattern of the air
compressor base. Using four (4) 3/8” x 1.25 GR-5
cap screws, 3/8” flat washers, and 3/8” nyloc nuts,
secure the compressor in place. The compressor is
air cooled, and must have a clean supply of
cooling air to the fan with minimum restrictions.
Adequate space must be provided for proper
circulation of air.
Electrical Connections:
From the air pressure switch there are two (2) wires,
red and black, running to the outside of the
compressor housing. Connect the black wire to the
vehicle frame or other suitable ground. Mount a
single throw toggle switch in a convenient location
and connect the red wire from the compressor to
this switch. Connect the other switch terminal to a
fuse holder and then to a 12-volt power supply. A
third wire is required from the air compressor switch
when connecting the speed control into the
system. (See drawing below)
Electric speed control:
An optional electric or electronic speed control
must be used to maintain proper operating speed
of the air compressor. The engine speed control will
automatically increase from idle to preset speed
when engaged and decrease when disengaged.
The electric cable pull speed control American
Eagle P/N 25740 is used on most gasoline engines.
The electronic speed controls are used only on Ford
7.3 and 6.0L diesel engines. Proper installation
instructions are provided with each system.
Hydraulic System:
The hydraulic system consists of the pump, oil
reservoir, filters and hoses. Installed on the
compressor is a valve block assembly that controls
the flow to the hydraulic motor. To this block, a 1/2”
high-pressure hose must be attached. This hose
comes from the hydraulic pumps pressure side. A
3/4” minimum low-pressure return line is connected
to the oil cooler outlet and is routed to the oil
reservoir. American Eagle recommends a sufficient
sized reservoir be provided which includes the
proper suction and return filters. The cooler on the
compressor is designed and sized to cool the air
compressor efficiently. An auxillary oil cooler is
required when additional hydraulically operated
equipment are added to the hydraulic system.
Pressure on the return line exceeding 200 PSI can
and will cause damage to the filter, cooler, and
components of the compressor hydraulic system.