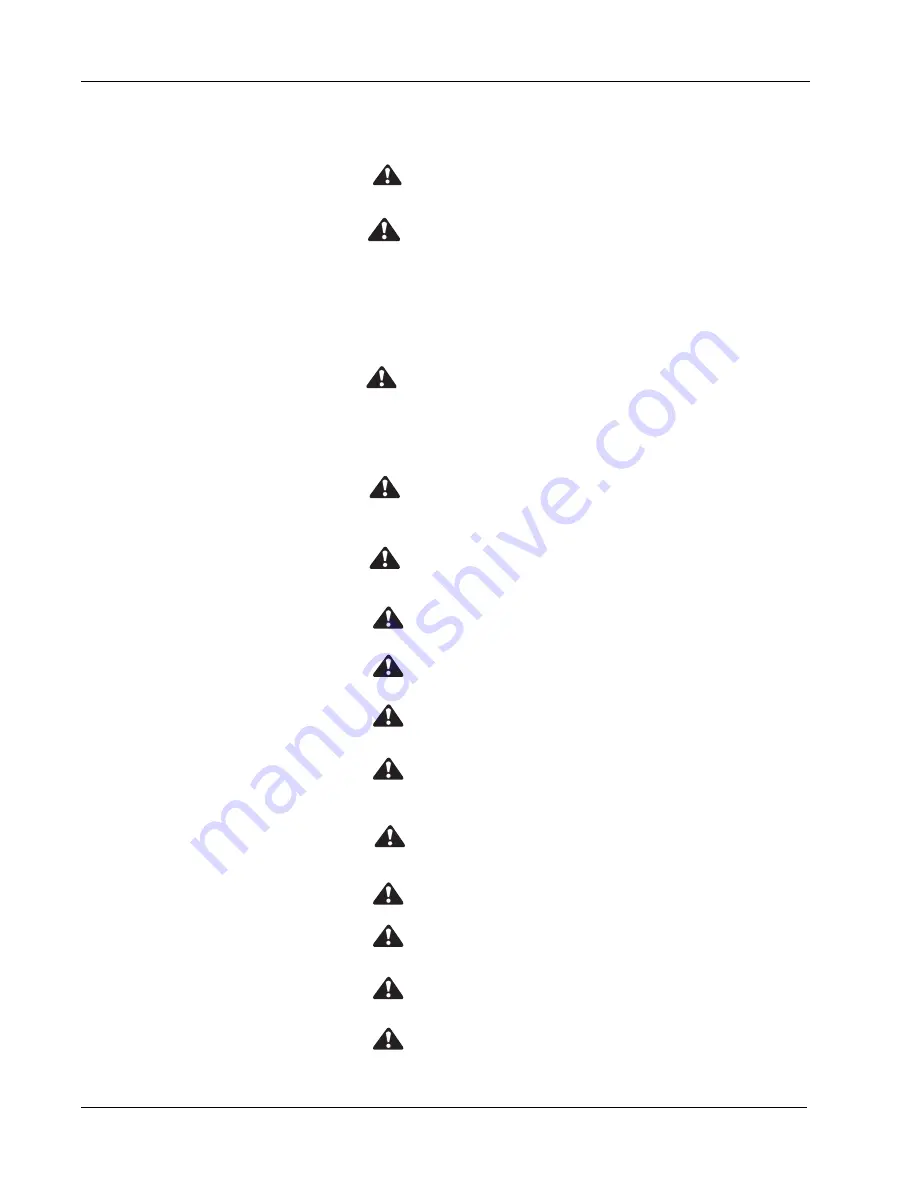
1-12
American-Lincoln
®
SC7740
SAFETY INSTRUCTIONS
THE FOLLOWING STATEMENTS ARE USED THROUGHOUT THIS MANUAL AS INDICATED IN THEIR
DESCRIPTIONS:
DANGER
To warn of immediate hazards which will result in severe personal injury or death.
WARNING
To warn of hazards or unsafe practices which could result in severe personal injury or death.
CAUTION
To warn of hazards or unsafe practices which could result in minor personal injury.
ATTENTION
To warn of unsafe practices which could result in extensive equipment damage.
NOTE
To give important information or to warn of unsafe practices which could result in equipment damage.
WARNING
THE FOLLOWING INFORMATION SIGNALS POTENTIALLY DANGEROUS CONDITIONS TO THE OPERATOR OR EQUIP-
MENT. READ THIS MANUAL CAREFULLY. KNOW WHEN THESE CONDITIONS CAN EXIST. THEN, TAKE NECESSARY
STEPS TO TRAIN MACHINE OPERATING PERSONNEL. FOR THE SAFE OPERATION OF THIS MACHINE, READ AND
UNDERSTAND ALL WARNINGS, CAUTIONS AND NOTES.
WARNING
Machines can ignite flammable materials and vapors. Do not use with or near flammables such as gasoline, grain
dust, solvents, and thinners.
WARNING
Improper use of heavy machinery can cause personal injury.
WARNING
Operate only when lids, doors, and access panels are securely closed.
WARNING
Use care when reversing machine in confined area.
WARNING
When servicing the machine, disconnect the batteries first to prevent possible injury.
WARNING
When working on the machine, empty hopper, remove batteries, clear area of people and obstructions, use
additional people and proper procedures when lifting the machine.
WARNING
Always empty the hopper and disconnect the battery before doing maintenance.
WARNING
You must have training in the operation of this machine before using it. READ THE INSTRUCTION BOOK.
WARNING
Do not operate this machine unless it is completely assembled.
WARNING
Do not use this machine as a step or furniture.
WARNING
Stop and leave this machine on a level surface. When you stop the machine, put the power switch in the “OFF”
position and engage the Wheel Lock.