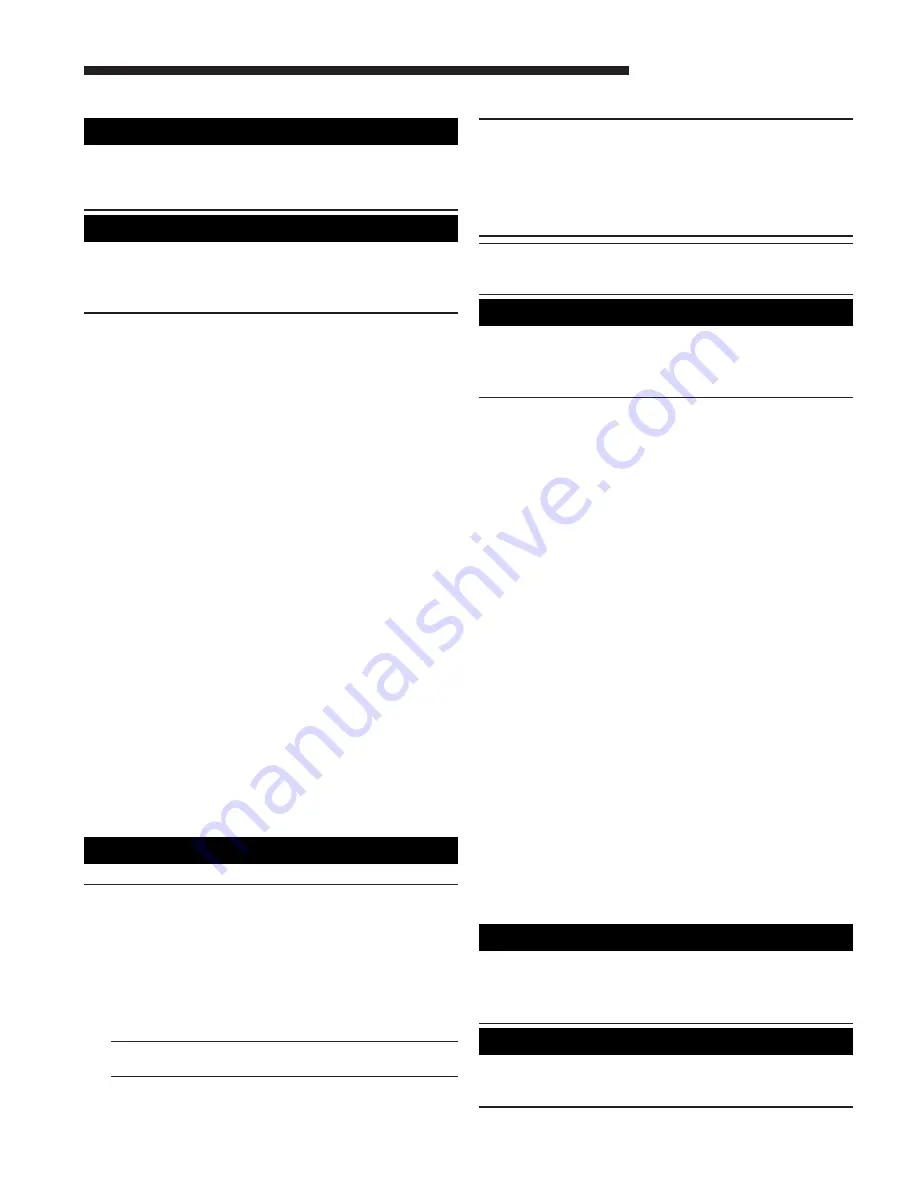
Page B-651-438
5
Service Facts
PERIODIC SERVICING REQUIREMENTS
▲
WARNING
!
Disconnect power to the unit before removing the blower
door. Allow a minimum of 10 seconds for IFC power supply
to drain to 0 volts. Failure to follow this warning could
result in property damage, personal injury or death.
▲
WARNING
!
CARBON MONOXIDE POISONING HAZARD
Failure to follow the service and/or periodic maintenance
instructions for the furnace and venting system, could
result in carbon monoxide poisoning or death.
1. GENERAL INSPECTION –
Examine the furnace
installation annually for the following items:
a. All flue product carrying areas external to the furnace
(i.e. chimney, vent connector) are clear and free of
obstruction. A vent screen in the end of the vent (flue)
pipe must be inspected for blockage annually.
b. The vent connector is in place, slopes upward and is
physically sound without holes or excessive corrosion.
c. The return air duct connection(s) is physically sound,
is sealed to the furnace and terminates outside the
space containing the furnace.
d. The physical support of the furnace should be sound
without sagging, cracks, gaps, etc., around the base so
as to provide a seal between the support and the base.
e. There are no obvious signs of deterioration of the furnace.
2. FILTERS – Filters should be cleaned or replaced (with
high velocity filters only), monthly and more frequently
during high use times of the year such as midsummer
or midwinter.
3. BLOWERS – The blower size and speed determine the
air volume delivered by the furnace. The blower motor
bearings are factory lubricated and under normal
operating conditions do not require servicing. If motor
lubrication is required it should only be done by a
qualified servicer. Annual cleaning of the blower wheel
and housing is recommended for maximum air output,
and this must be performed only by a qualified servicer
or service agency.
4. IGNITER – This unit has a special hot surface direct
ignition device that automatically lights the burners.
Please note that it is very fragile and should be handled
with care.
▲
CAUTION
!
Do not touch igniter. It is extremely hot.
5. BURNER – Gas burners do not normally require
scheduled servicing, however, accumulation of foreign
material may cause a yellowing flame or delayed
ignition. Either condition indicates that a service call is
required. For best operation, burners must be cleaned
annually using brushes and vacuum cleaner.
Turn off gas and electric power supply. To clean burners,
remove burner box cover (6 to 8 screws) and top burner
bracket. Lift burners from orifices.
NOTE:
Be careful not to break igniter when removing burners.
Clean burners with brush and/or vacuum cleaner. Reas-
semble parts by reversal of the above procedure. The
burner box must be resealed when replacing box cover.
NOTE:
On LP (propane) units, some light yellow tipping of the
outer mantle is normal. Inner mantle should be bright blue.
Natural gas units should not have any yellow tipped flames.
This condition indicates that a service call is required. For
best operation, burners must be cleaned annually using
brushes and vacuum cleaner.
NOTE:
On LP (propane) units, due to variations in BTU content and
altitude, servicing may be required at shorter intervals.
▲
WARNING
!
CARBON MONOXIDE POISONING HAZARD
Failure to follow the service and/or periodic maintenance
instructions for the furnace and venting system, could
result in carbon monoxide poisoning or death.
6. HEAT EXCHANGER/FLUE PIPE – These items must be
inspected for signs of corrosion, and/or deterioration at the
beginning of each heating season by a qualified service
technician and cleaned annually for best operation. To
clean flue gas passages, follow recommendations below:
a. Turn off gas and electric power supply.
b. Inspect flue pipe exterior for cracks, leaks, holes or
leaky joints. Some discoloration of PVC pipe is normal.
c. Remove burner compartment door from furnace.
d. Inspect around insulation covering flue collector box.
Inspect induced draft blower connections from
recuperative cell and to the flue pipe connection.
e. Remove burners. (See 4.)
f. Use a mirror and flashlight to inspect interior of heat
exchanger, be careful not to damage the igniter, flame
sensor or other components.
g. If any corrosion is present, contact a service agency.
Heat exchanger should be cleaned by a qualified
service technician.
h. After inspection is complete replace burner box cover,
burners, and furnace door.
i. Restore gas supply. Check for leaks using a soap
solution. Restore electrical supply. Check unit for
normal operation.
7. COOLING COIL CONDENSATE DRAIN - If a cooling
coil is installed with the furnace, condensate drains
should be checked and cleaned periodically to assure
that condensate can drain freely from coil to drain. If
condensate cannot drain freely water damage could
occur. (See Condensate Drain in Installer’s Guide.)
▲
CAUTION
!
Label all wires prior to disconnection when servicing
controls. Wiring errors can cause improper and
dangerous operation.
Verify proper operation after servicing.
▲
WARNING
!
NEVER USE AN OPEN FLAME TO TEST FOR GAS LEAKS:
AN EXPLOSION COULD OCCUR, CAUSING INJURY OR
DEATH.
Summary of Contents for ADY060R9V3W
Page 6: ...6 Page B 651 438 Service Facts UY WIRING DIAGRAM ...
Page 7: ...Page B 651 438 7 Service Facts UY SCHEMATIC DIAGRAM ...
Page 8: ...8 Page B 651 438 Service Facts DY WIRING DIAGRAM ...
Page 9: ...Page B 651 438 9 Service Facts DY SCHEMATIC DIAGRAM ...