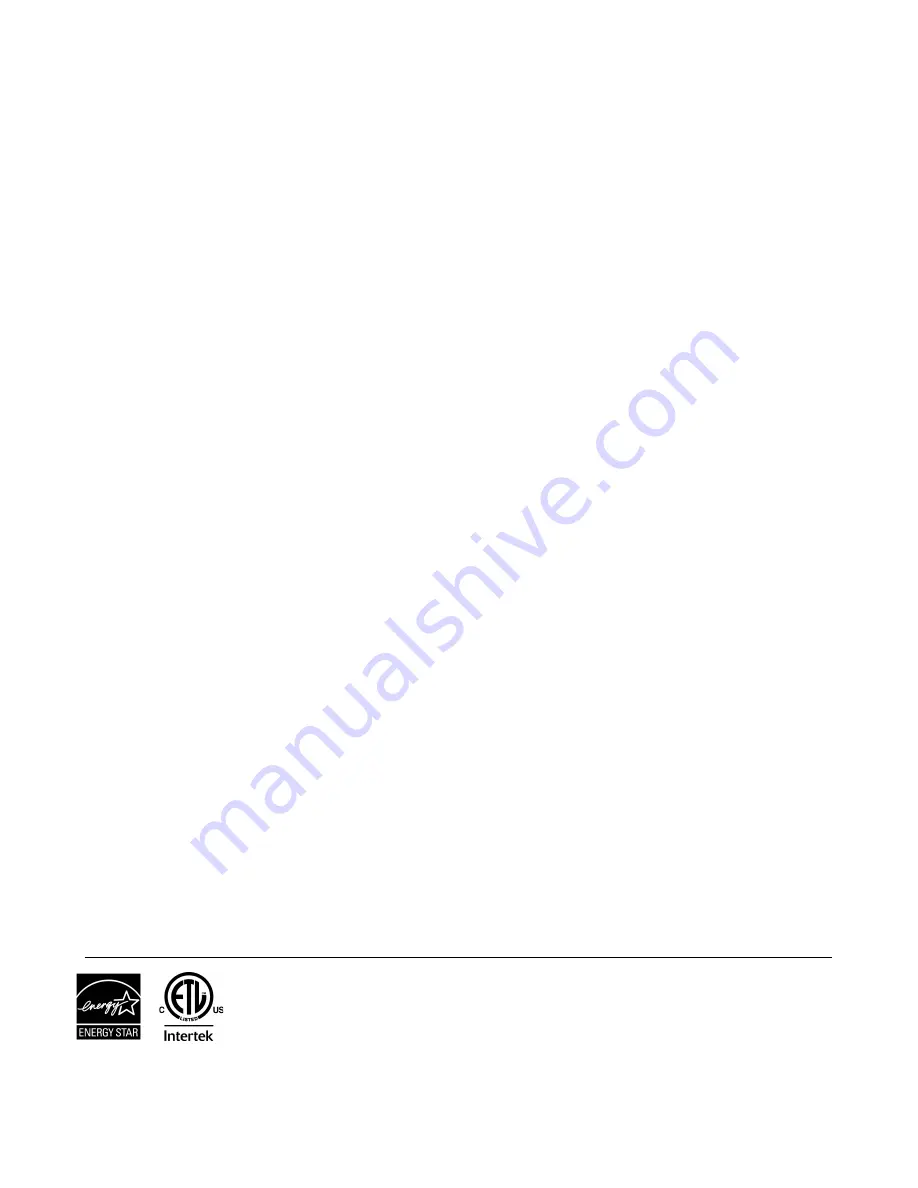
About Trane and American Standard Heating and Air Conditioning
Trane and American Standard create comfortable, energy efficient indoor environments for residential applications. For
more information, please visit www.trane.com or www.americanstandardair.com.
The manufacturer has a policy of continuous data improvement and it reserves the right to change design and specifications without notice. We are committed to
using environmentally conscious print practices.
18-CE12D1-1D-EN
15 Sep 2020
Supersedes 18-CE12D1-1C-EN
(April 2020)
©2020