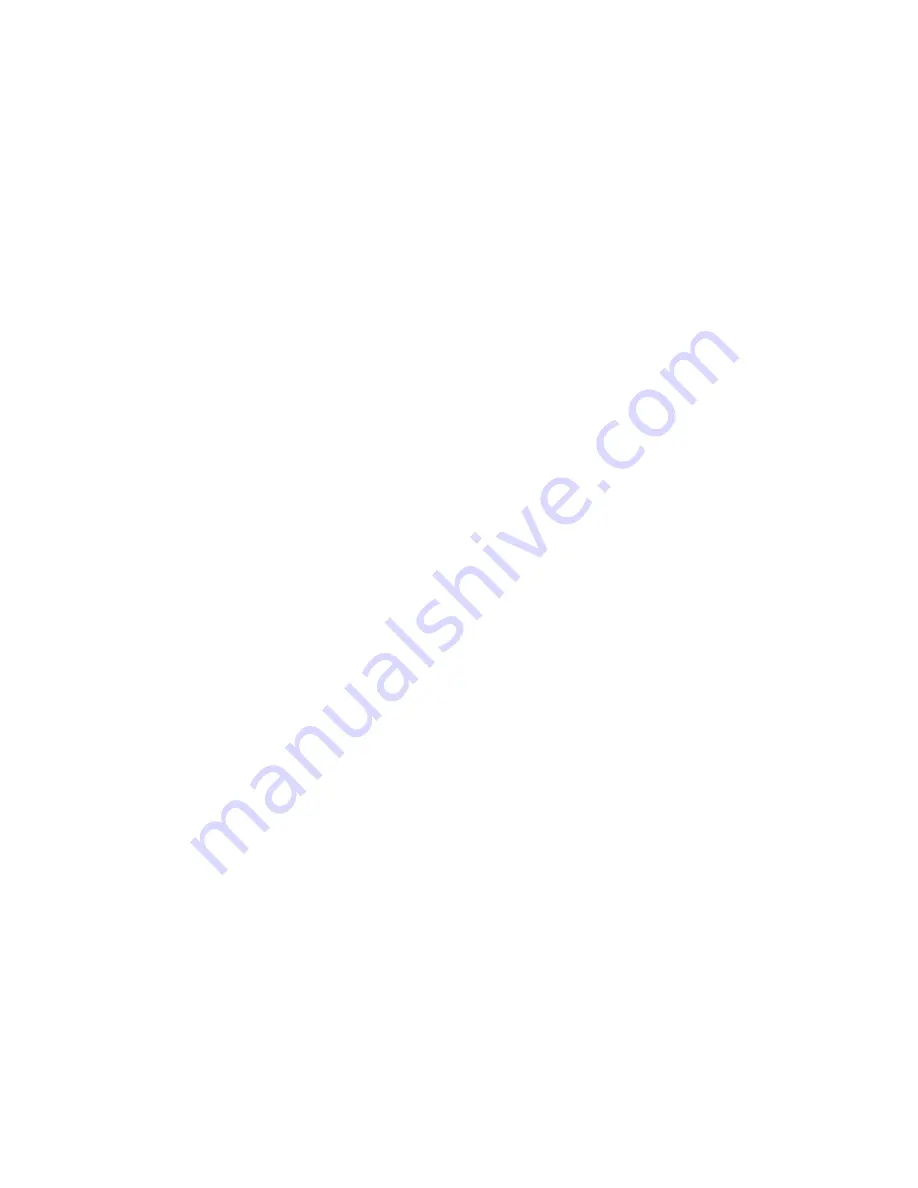
5
www.amico.com
Installation
THE ALARM BOX
Install the back-box to the studs of the wall at the desired height. Ensure that the box is securely in place. The mounting
brackets are adjustable to suit the thickness of the wall. MAKE SURE the box is parallel, squared and flush with the finished wall
surface, to ensure that the frame assembly will fit properly.
FOR LOCAL SENSOR ONLY
If the sensors are to be mounted locally (inside the back box), the pipe stubs must be connected to the pipeline. Using
silver-brazing techniques, connect each pipe stub to it’s appropriate gas or vacuum while ensuring that the bottom of
the pipe stub is wrapped with a damp cloth. BE CAREFUL not to damage the DISS check-valve by overheating the lower
portion of the copper pipe. When the brazing of pipe stubs has been completed, the system can be pressure tested.
STANDING PRESSURE TEST
Perform a standing pressure test on the piping system as per NFPA 99 “Health Care Facilities”. Inspect all joints for leaks
and make certain each gas is piped to a correspondingly labelled gas service.
FRAME/MODULE ASSEMBLY
Step #1 Remove the frame/module assembly from its protective box.
Step #2 Remove screws from the frame section (6 screws).
Step #3 Attach the flat head screws (provided with frame in plastic bag) to the hinge. This will line up with holes on
the box.
Step #4 Attach the frame wire with 2 dome head screws (provided with frame in plastic bag).
Step #5 Close the frame panel and tighten the screws on the frame plate.
Step #6 Carefully place the front frame over the fastened plate. Refasten the screws that were removed in Step #2.