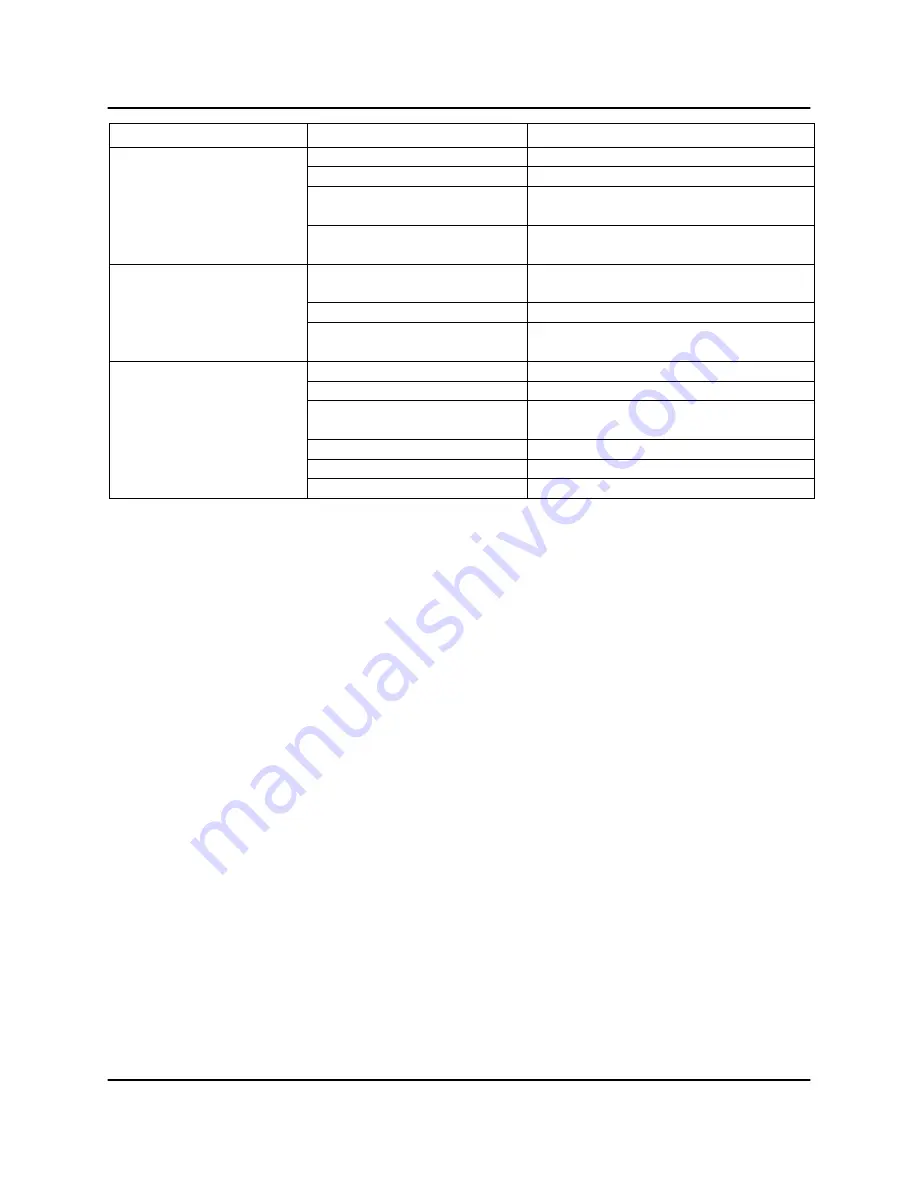
Troubleshooting
Ampco Pumps Company
Page 22
Symptom
Cause
Solution
Tri-Blender is noisy
Magnetic hum in motor
Consult motor manufacturer
Motor bearings are worn
Consult motor manufacturer
Tri-Blender bearings are
worn
Replace bearings
Foreign matter is rotating
with impeller
Remove casing and foreign matter
inside, Inspect for damage
Excessive vibration
Blender is not leveled
properly
Level blender
Impeller is damaged
Replace impeller
Foreign matter in casing
Remove casing and foreign matter,
inspect f or damage
O-ring seal is worn
Replace o-ring seal
Carbon seal is worn
Replace carbon seal
Insufficient compression on
seal
Replace spring
Back plate gasket is worn
Replace gasket
Back plate is worn
Replace back plate
Clamp is loose
Tighten clamp
Dry-Blender leaks
Ampco Pumps Company AC+ Dry Blender Manual M-028 Rev C 12.20