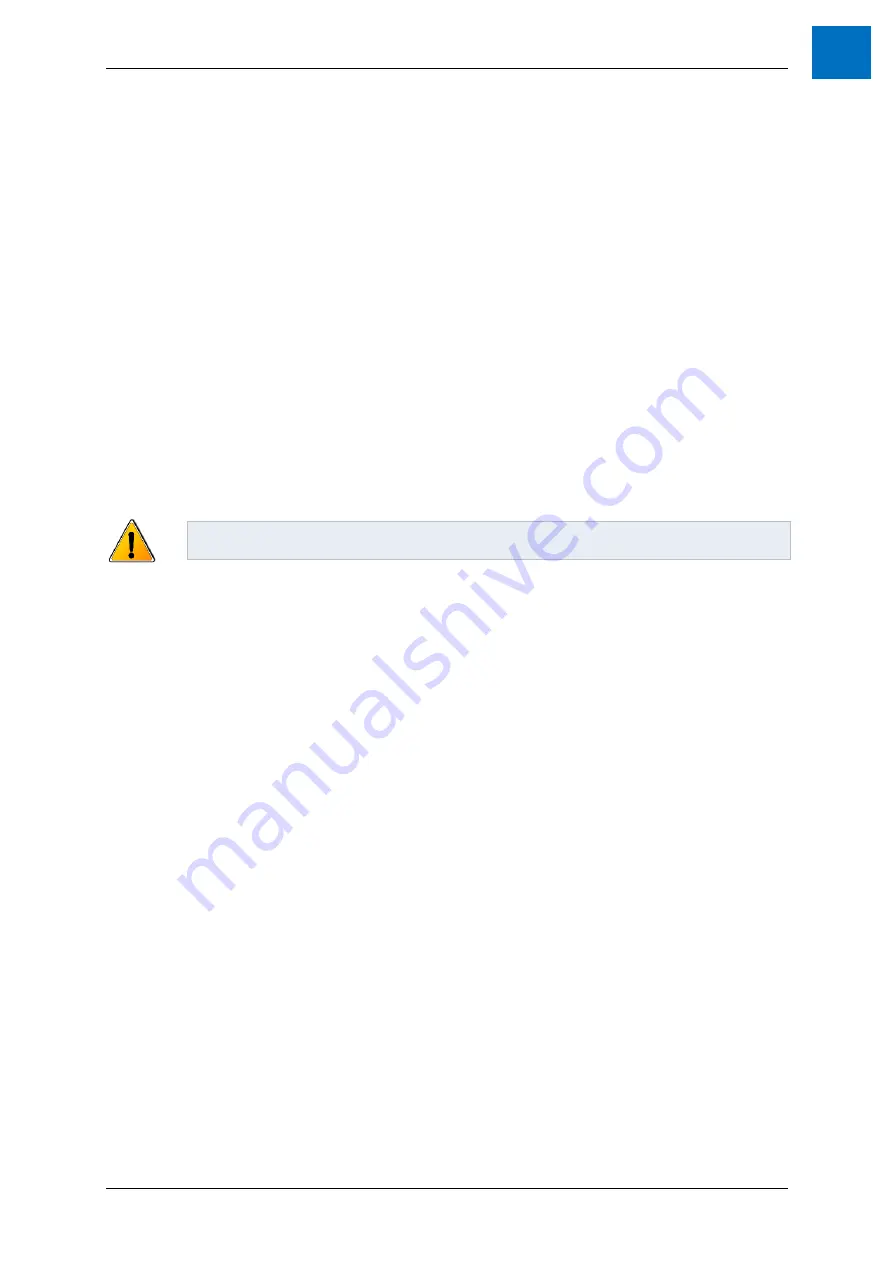
Planning the Electrical Installation
ANCA Motion
D-000088 Rev 09
23
5
5
Planning the Electrical Installation
5.1
What this Chapter Contains
This chapter contains information that is useful in planning the electrical installation of the servo drives:
Motor & Drive Compatibility
Electrical Isolation and Protection Devices
Cable Selection and Routing
The AMD2000 series of drives must be installed by a professional. A professional in this context is a person or
organisation possessing the necessary skills and qualifications relating to the installation and/or commissioning of
power drive systems, including their EMC aspects.
5.2
Motor and Drive Compatibility
Ensure that the AMD2000 drive and the AC motor intended for use are compatible according to their respective
allowable limits of operation. For example, the AMD2000 uses PWM to apply power to the motor. The insulation
stresses encountered using PWM will typically be higher than those experienced in non-PWM powered motor
applications.
Warning:
These drives are specifically for use ONLY with induction motors and PMSM motors
rated for operation on a PWM inverter power supply.
Refer to
11.2.2 Motor Electrical Information Summary
5.3
Power Supply Disconnecting Device
A Mains disconnecting device must be connected between the AC power source and the AMD2000 drive. This
must conform to the requirements and applicable safety regulations of the region of operation. An appropriate
approval for switches is IEC 60947-2 and for circuit breakers IEC 60947-3. Generally switches should be
selected with a mechanism available to use a lock. The drive STO function DOES NOT isolate power from any
part of the drive.
Refer to
6.7 Power Disconnect and Protection Devices
5.4
Emergency Stop Devices
An Emergency Stop Device must be installed for safety reasons within easy reach of operators and maintenance
personnel at all operator control stations and wherever deemed necessary. Please note that Emergency Stop
Devices are NOT to be confused with the Safe Torque Off (STO) function contained within the drive. The STO
may be used in such an Emergency Stop Device chain to provide a mechanism for stopping, but it is the
responsibility of the machine integrator to construct the suitable Emergency Stop Device, whether utilising STO
or otherwise.
For information regarding STO, refer to
7.7 Safe Torque Off (STO) Operation.
Summary of Contents for AMD2000 Series
Page 1: ...AMD2000 Series D2xxx Servo Drive User Guide D 000088 Rev 10 ...
Page 131: ...Technical Data ANCA Motion D 000088 Rev 09 119 10 ...
Page 132: ...AMD2000 Series D2xxx Servo Drive User Guide 120 D 000088 Rev 10 ANCA Motion 10 9 1 2 3 Phase ...
Page 133: ...Technical Data ANCA Motion D 000088 Rev 09 121 10 ...
Page 135: ...Technical Data ANCA Motion D 000088 Rev 09 123 10 ...
Page 136: ...AMD2000 Series D2xxx Servo Drive User Guide 124 D 000088 Rev 10 ANCA Motion 10 9 2 2 3 Phase ...
Page 137: ...Technical Data ANCA Motion D 000088 Rev 09 125 10 ...
Page 139: ...Technical Data ANCA Motion D 000088 Rev 09 127 10 ...
Page 140: ...AMD2000 Series D2xxx Servo Drive User Guide 128 D 000088 Rev 10 ANCA Motion ...
Page 141: ...Technical Data ANCA Motion D 000088 Rev 09 129 10 10 9 3 2 3 Phase ...
Page 142: ...AMD2000 Series D2xxx Servo Drive User Guide 130 D 000088 Rev 10 ANCA Motion ...