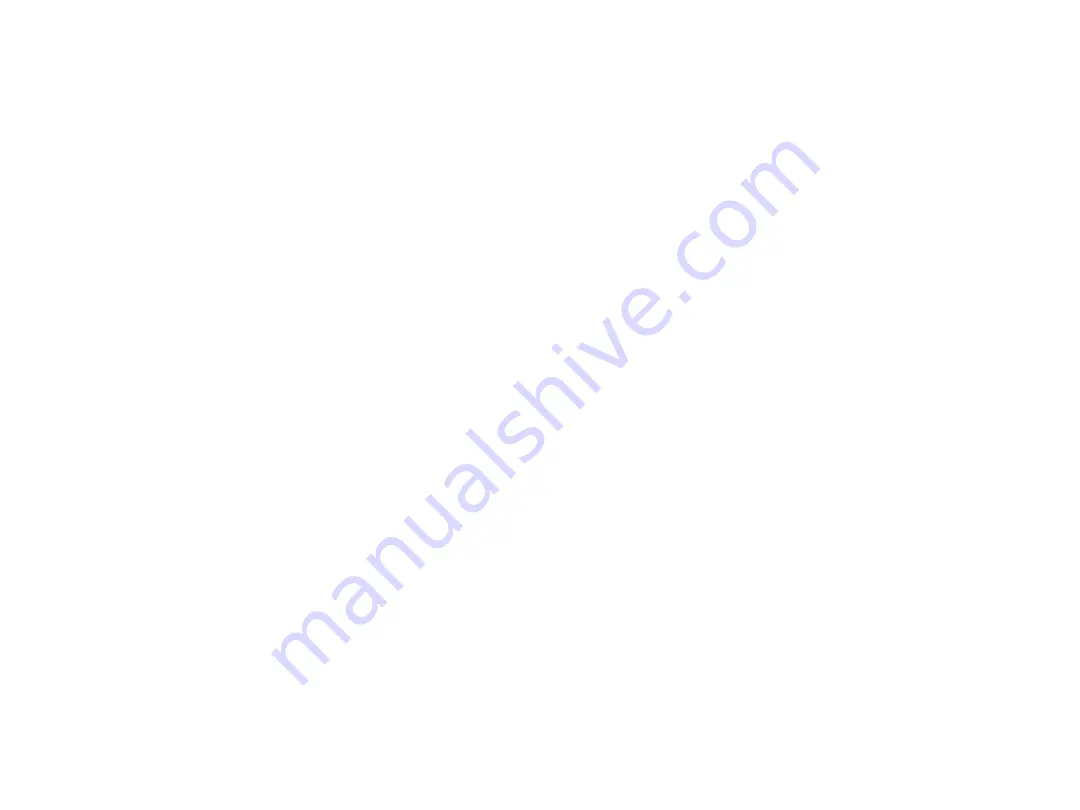
page6of36
2 Installation Instructions
●Please make sure the packing is intact before receiving the goods.
●After unpacking, please check carefully whether the parts list is consistent with the physical
parts.
●If you have any problems, please contact your supplier in time.
●Pictures in this manual are for your reference ,please take the object as the standard .