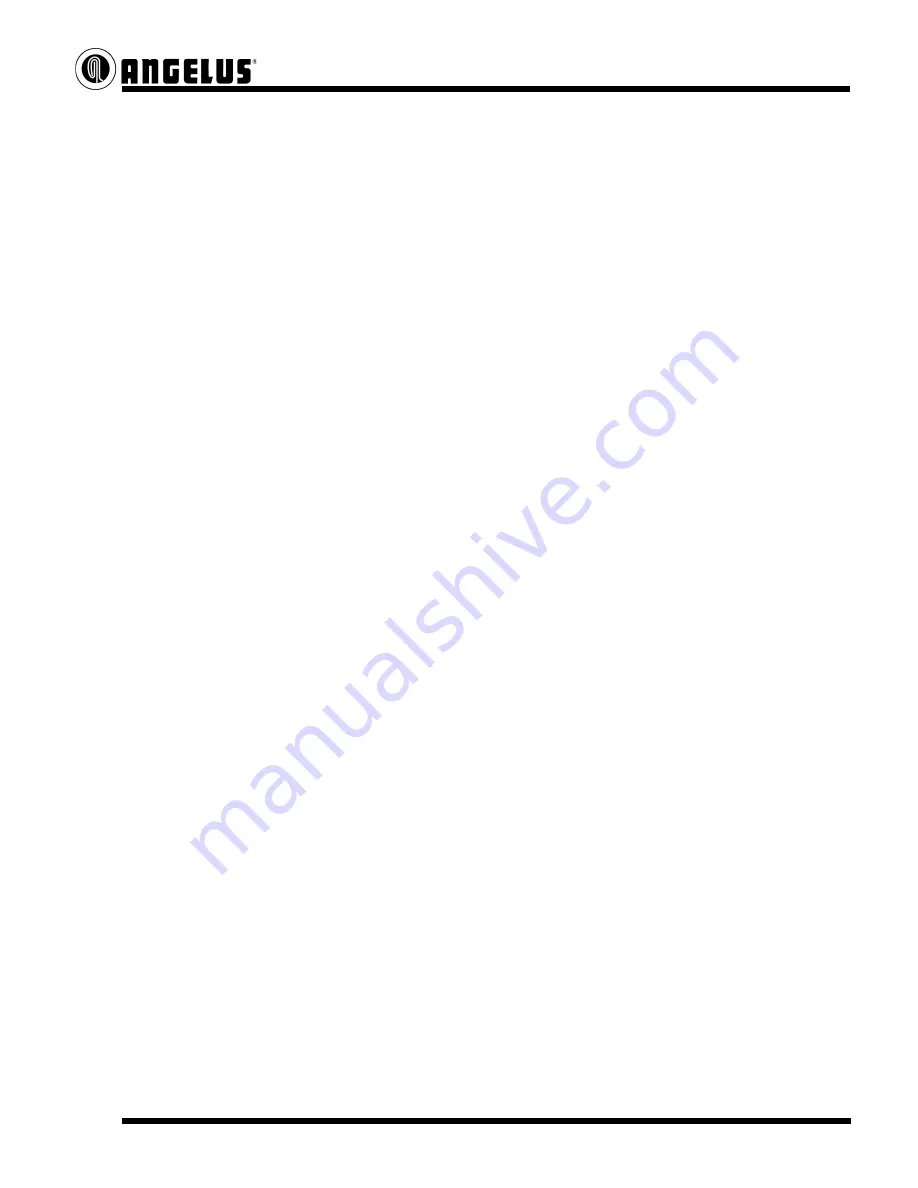
ANGELUS SANITARY CAN MACHINE COMPANY
SERVICE NOTICE
9/9/99-18033004
11 of 14
Rev. 1 - 9/9/99
FILLER DRIVE / SEAMER SAFETY CLUTCH SYSTEM OPERATION
STATIONARY FIELD TOOTH CLUTCH OPERATION
THE TORQUE RATING OF THIS 24VDC CLUTCH IS RATED AT 650 FT-LB. THE STANDBY POWER
SYSTEM POWERS THE ENGAGE VOLTAGE OF ABOUT 24VDC. ONCE FULLY ENGAGED THE
CLUTCH IS AUTOMATICALLY SWITCHED TO AN ADJUSTABLE HOLDING VOLTAGE.
STANDBY POWER SUPPLY OPERATION
THE STANDBY POWER SUPPLY PROVIDES 24VDC TO THE CLUTCH TO ENGAGE AND PROVIDES
HOLDING VOLTAGE WHEN THE NORMAL PLANT POWER IS TRIPPED OFF. THE VOLTAGE IS
SUPPLIED BY THE GEL-CELL BATTERIES, AND IS ALWAYS KEPT IN A CHARGED STATE. A
FIXED
TIMER IS IN THE CIRCUIT TO DROP OUT THE BATTERIES AFTER 15 SECONDS, TO KEEP
THE
BATTERIES FROM COMPLETELY DISCHARGING.
CLUTCH PROXIMITY SENSOR OPERATION
THE CLUTCH SENSOR PROVIDES A SIGNAL THAT THE FILLER DRIVE CLUTCH IS FULLY ENGAGED.
THIS SIGNAL DROPS THE VOLTAGE TO AN HOLDING VALUE. IF TIES SIGNAL GOES LOW, THE
CLUTCH CIRCUIT WILL GO LOW AND DISENGAGE THE CLUTCH. THE ACCEPTABLE GAP FOR THE
SETTING OF DISTANCE FROM THE CLUTCH PLATE IS BETWEEN 0.012 TO 0.035 INCHES, WHEN
THE
CLUTCH IS FULLY ENGAGED.
FILLER DRIVE CLUTCH CONTROL LOGIC OPERATION
THE PLC LOGIC WILL ENABLE THE INCHING LOGIC AND WILL DISABLE THE MAIN DRIVE CIRCUIT,
WHEN THE CLUTCH IS TO BE MANUALLY ENGAGED. EITHER THE CLUTCH PRESET BUTTON ON
THE OPERATOR INTERFACE OR THE CLUTCH ON-OFF SELECTOR ON THE PENDANT WILL
ENABLE
THE INCH CIRCUIT. IN THE EVENT THAT THE CLUTCH IS DISENGAGED WHILE
RUNNING THE
SEAMER, THIS WILL ENABLE THE BRAKE CIRCUIT AND SHUT THE SEAMER
DOWN IN A BRAKE
STOP.
PLC LOGIC ALSO PROVIDES TIMERS, WHEN THE SEAMER GOES THRU A SPEED TRANSITION, OF
SLOW TO FAST OR FAST TO SLOW. THIS PROVIDES 24VDC TO THE CLUTCH TO ENSURE THAT
THE
CLUTCH WILL STAY ENGAGED. THIS ALSO IS PRESENT WHEN JOGGING OR ON AN
EMERGENCY
STOP.
NO CAN NO COVER SYSTEM
OPERATION AND CONTROL LOGIC FOR 180S SEAMERS
THE CONTROL COMPONENTS FOR THE OPERATION OF THE NO CAN NO COVER SYSTEM CONSIST
OF THE FOLLOWING; TURCK NO CAN PROXIMITY SENSOR, TURCK FLAG PROXIMITY SENSOR,
GORDOS DC SOLID STATE RELAY, AND COVER FEED SOLENOID POWER CIRCUIT COMPONENTS.
NO CAN NO COVER SYSTEM GENERAL INFORMATION
THE NO CAN NO COVER SYSTEM IS EMPLOYED AS A MEANS OF CONTROLLING THE MATCHING OF
FILLED CANS TO BE SEAMED WITH COVERS AT HIGH SPEEDS. THIS SYSTEM INCORPORATES TWO
(2) COVER FEED STACKS WITH TWO (2) SOLENOID SEPARATORS. EACH SEPARATOR HAS IT’S OWN
CAN AND FLAG PROXIMITY SENSORS. THE CRITICAL PORTION OF THIS SYSTEM IS IN THE TIMING
AND SETUP OF THE FLAG SENSORS IN RELATION TO THE SEPARATOR.
NO CAN NO COVER SYSTEM OPERATION
CAN PROXIMITY SENSOR OPERATION