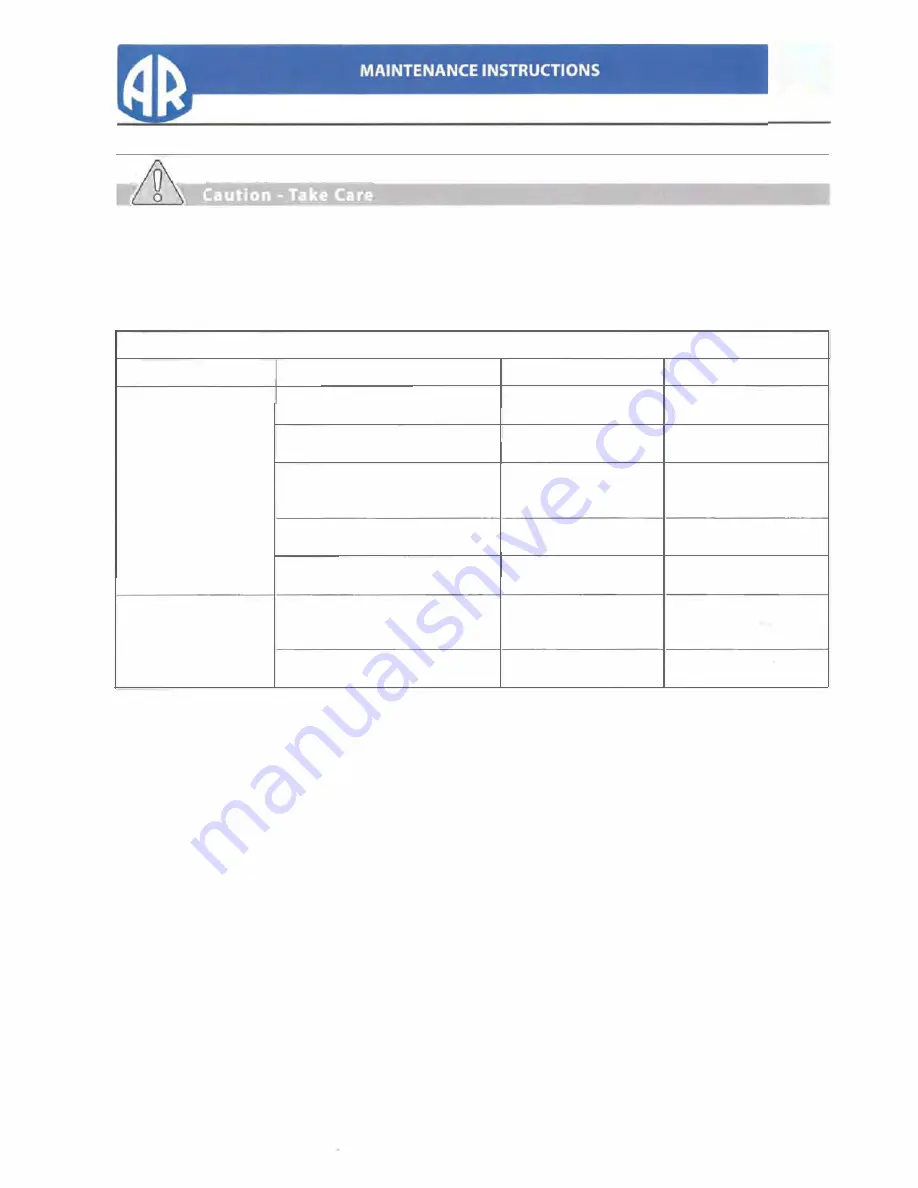
Safety recommendations for maintenance
Before doing any maintenance work, depressurise the water system and isolate the pump from all en-
ergy sources.
I
When the jobs are done, before restarting the pump, check that no tools, rags or other materials have
been left close to moving parts or in hazardous zones.
Replace any excessively worn components with original parts and use the lubricants recommended by
the manufacturer.
Scheduled maintenance table
Frequency
Component
Procedure
Reference
Filter
Inspect filter cartridge See "Inspecting the
filter"
Pump
Checking the oil level
See "Checking the oil
level"
Connection of pump to power
Inspection
-
Every working day
source (pulley, belt, coupling)
Pump
Inspect mounting
See "Inspecting the
pump mounting"
Pipes and connections
Inspection
See "Inspecting the
connections and pipes"
Pressure accumulator (if in-
Check inflation pres-
See "Checking the
Every 100 working
stalled)
sure
inflation pressure"
hours
Reduction gear (if installed)
Check oil
See "Checking the oil
level"
Dispose of the worn-out components and lubricants in accordance with the relevant statutory require
ments.
Carry out the routine maintenance procedures specified by the manufacturer to keep the pump safe
and performing well.