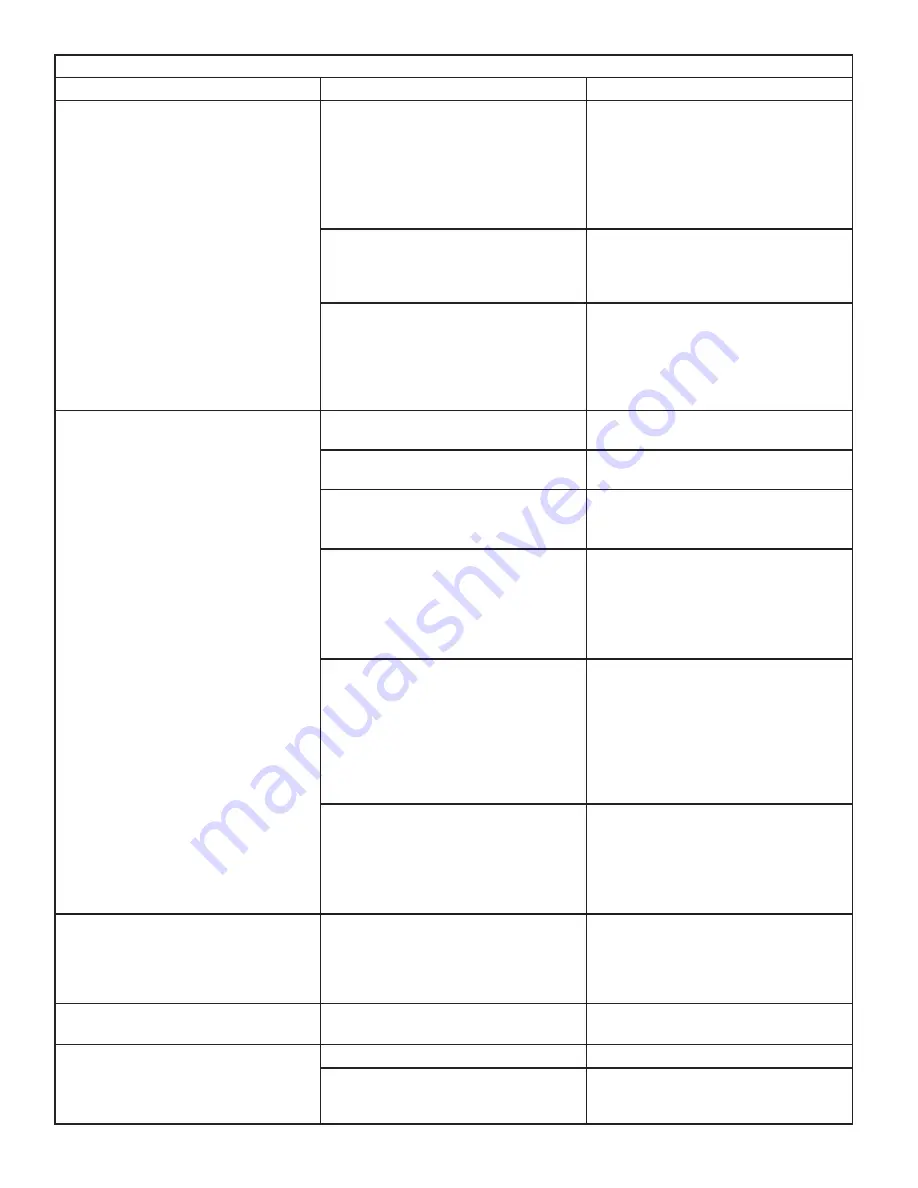
Troubleshooting Chart
Problem
Possible Causes
Possible Solution
Foaming oil.
Air in the hydraulic hose(s) or cylinder.
Fill reservoir with proper fluid. Refer
to “4.1 Monthly Inspection” on page
<?> for oil specifications and “4.3
Check Power Module Fluid Level” on
page <?> for oil level. Raise and lower
platform several times to remove any
trapped air.
Filter screen.
Filter screen in pump reservoir is
damaged or plugged with dirt. Replace
filter screen.
Replacement part — A‑150016.
Broken or loose fluid return tube.
Remove oil reservoir and make sure
return tube is below oil level. If tube
has turned or fallen out, reinstall it into
the pump housing. Use a center punch
to “stake” tube into position.
Replacement part — A‑150015
Motor runs, but liftgate will not open or
platform will not lower to the ground.
Structural damage. Check clearance
between platform and floor extension.
Fix damage. Replace worn parts. Refer
to the separate Parts Manual.
Latch pin.
Slide the latch pin to the open position.
Lowering valve solenoid (power down
models only).
Check the solenoid. “4.9 Checking Valve
Cartridge and Solenoid” on page <?>.
Replacement part — A‑176315.
Lowering valve cartridge (power down
models only).
With platform on ground, check, remove,
and clean valve cartridge using the
procedure in section “4.9 Checking Valve
Cartridge and Solenoid” on page <?>. If
plunger will not move freely, replace.
Replacement part — A‑130216.
Cylinder seals.
Cylinder piston seal are damaged
allowing fluid to leak past piston when
trying to raise platform. Replace the
cylinder, repair is not practical. Refer to
section “4.12 Checking Cylinder Piston
Seals” on page <?>.
Replacement part — A‑130113 Cylinder
3” or A‑130114 Cylinder 4”.
Flow control valve.
Remove flow control valve and hook
hydraulic hose directly to the cylinder.
If the cylinder operates properly, replace
the valve. “4.14 Checking Flow Control
Valve” on page <?>.
Replacement part — A‑130102.
Latch pin is broken or bent.
Operator has lowered platform without
releasing latch pin.
The latch pin is only used to prevent the
liftgate from opening due to a pressure
leak or pressure bleed‑off over an
extended period of time. Always release
latch before opening liftgate.
Platform raises truck when lowered to
the ground (power down models only).
Power down system pressure is set too
high.
See section “4.13 Checking System
Pressure” on page <?>.
Platform will not open.
Platform operating area is not clear.
Clear platform operating area.
Latch pin will not slide freely to release
liftgate.
Activate the “UP” switch and raise the
liftgate to the fully stored position.
The latch pin should slide freely.
Summary of Contents for AC-1600
Page 2: ......