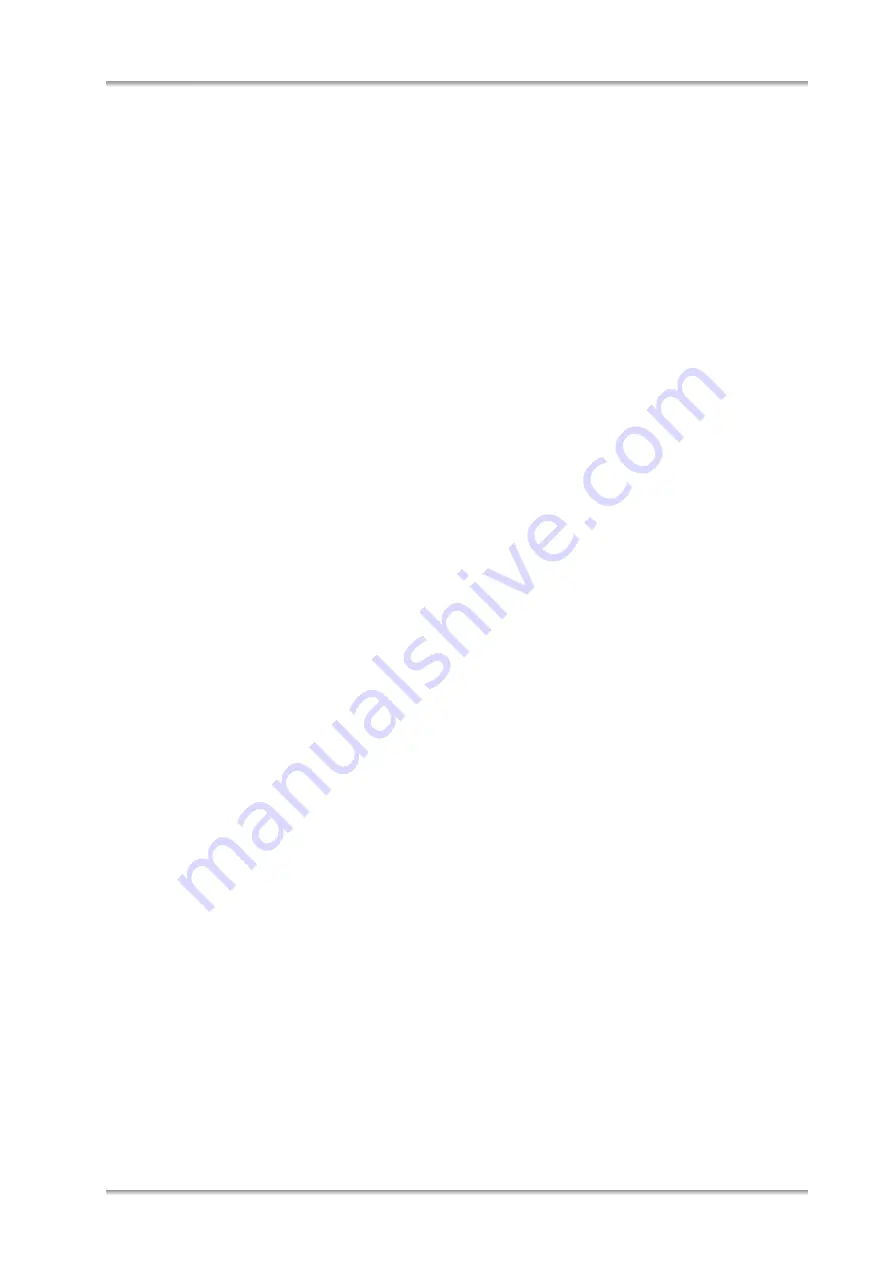
Contents
4
B40IB006EN-D
Contents
1.1 General safety instructions ............................................................................................................... 7
1.2 Radiation Safety................................................................................................................................ 8
1.3 Conventions for safety messages..................................................................................................... 8
1.4 Safety Signs on the Instrument......................................................................................................... 9
2.2.1 Housing with Safety Switch Box ............................................................................................. 10
2.2.2 Lid ........................................................................................................................................... 11
2.2.3 Sample Holder Flanges .......................................................................................................... 12
3 Checking the Supplied Parts ............................................................................................................... 15
4 Installation ............................................................................................................................................. 17
4.2 Mounting the Adapter on HTK 1200N............................................................................................. 17
4.3 Mounting HTK 1200N on the Goniometer....................................................................................... 18
4.4 Installing CCU 1000 ........................................................................................................................ 18
4.4.1 Power Supply for the Heater................................................................................................... 19
4.4.2 Thermocouple of Stationary Sample Holder and Sample Spinner ......................................... 19
4.4.3 Connection of Sample Spinner Motor..................................................................................... 20
4.4.4 Connection for Safety Circuit .................................................................................................. 20
4.5 Connecting CCU 1000 with a Computer......................................................................................... 20
4.6 Installing the Cooling Water Circuit................................................................................................. 21
4.7 Installing the Gas Supply ................................................................................................................ 21
4.8 Installing the Vacuum Equipment ................................................................................................... 21
5.1 Alignment of the Sample Holder ..................................................................................................... 23
5.2 Height adjustment with Rigid Adapter............................................................................................. 23
5.3 Height Adjustment with Motorized Alignment Stage ....................................................................... 24
5.4 Adjustment of Chamber Rotation.................................................................................................... 24
5.5 Alignment procedure....................................................................................................................... 24
5.6 Checking the Instrument Condition................................................................................................. 25
5.7 Turning on the Instrument............................................................................................................... 26
7.1.1 Exchanging the sample holder body....................................................................................... 32
7.1.2 Matching Sample Holder Height to Sample Thickness........................................................... 33