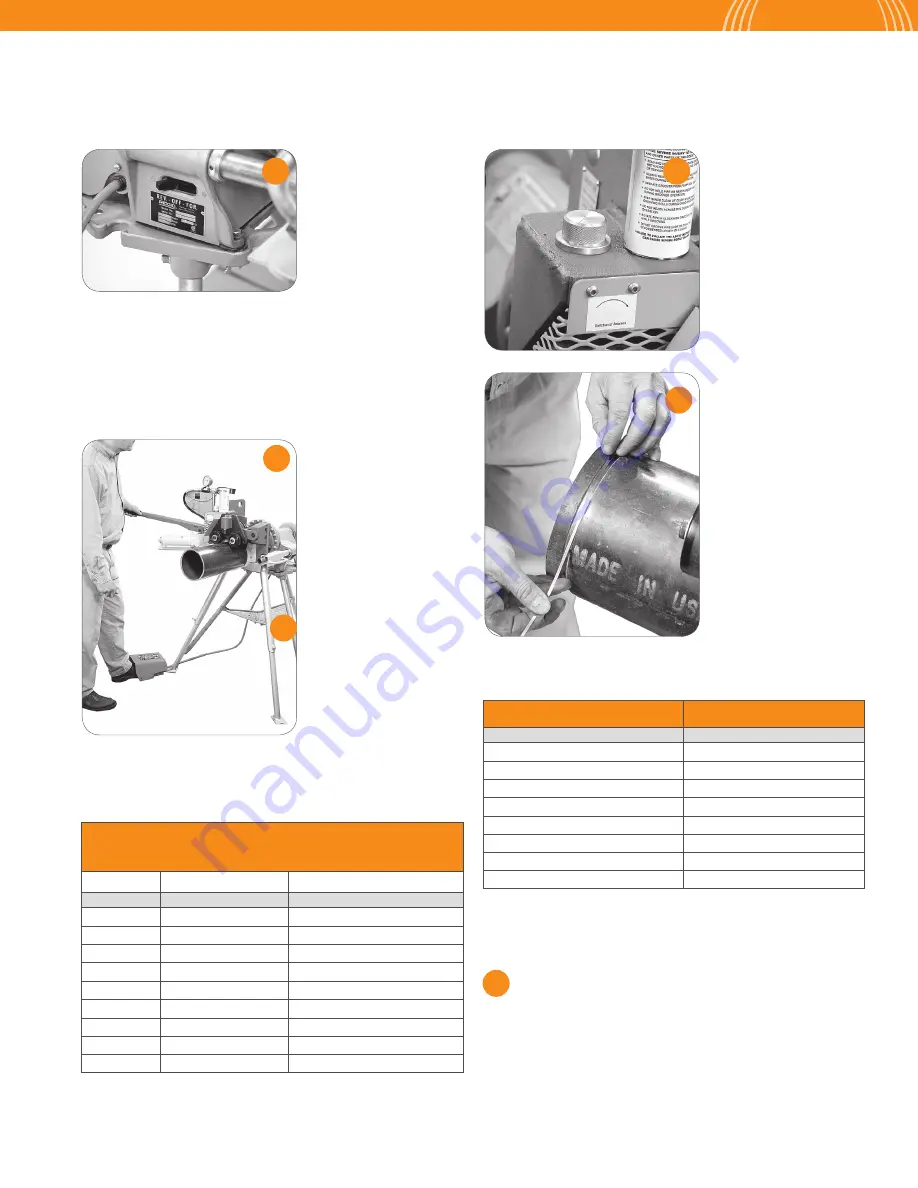
BUILDING CONNECTIONS THAT LAST
11
GROOVING THE PIPE OR TUBE - STEEL PIPE
Recheck for correct pipe
set-up and position on the
bottom roll and adjust as
required. Close the relief
valve on the hydraulic hand
pump and increase pump
pressure to 400 psi.
(200 psi for Sch. 10)
Maintain grooving force
until the Knurled Stop (groove
diameter stop) comes into
full, firm contact with the top
of the groover base head.
Allow the pipe to rotate 1 to
2 revolutions assuring
completion of the groove.
Release the foot switch to allow
the pipe to stop rotation.
Start the drive motor by
depressing the foot switch to
rotate the pipe. Assure that
the pipe is tracking firmly
against the back of the
bottom roll.
Open the hydraulic hand
pump release valve by turning
counterclockwise. Remove the
pipe from the Groover.
Check the groove diameter.
If required, adjust the groove
diameter stop to assure
grooves to be within Gruvlok
groove specification limits.
(Grooving Specifications are
shown on page 20 of these
instructions.)
With the pipe rotating,
increase grooving force
by slowly pumping the
hydraulic pump handle
to raise pump pressure.
Do not pump too fast.
1
4
2
5
5
3
KNURLED STOP
**
ADJUSTMENT
GROOVE DIAMETER CHANGE
Turns
Inches
1/8
.008"
1/4
.016"
3/8
.024"
1/2
.032"
3/4
.047"
1
.062"
11/2
.094"
2
.125"
STEEL PIPE
RECOMMENDED GROOVING PRESSURE
Pipe Size
Wall
Grooving Pressure
Inches
Schedule
PSIG
2" - 6"
10
800 - 1,000
8" - 12"
10
3,000 - 3,400
14" - 16"
10
3,400 - 3,800
2"
40
1,600 - 2,000
2
1
/
2
" - 4"
40
2,600 - 3,000
5" - 6"
40
3,400 - 3,800
8" - 10"
40
4,400 - 4,800
12"
STD.
4,600 - 5,000
14" - 16"
STD.
4,600 - 5,000
Note:
Adjustment of the Knurled Stop (groove diameter stop) will produce
the below listed groove diameter changes.
**Knurled Stop Rotation:
Clockwise rotation – Increase groove diameter
Counterclockwise rotation – Decrease groove diameter
After adjustment of the Knurled Stop, if the groove diameter is
large (i.e. shallow groove depth), place the pipe end back into the
Groover and complete the same groove to the new diameter stop
setting. If the groove diameter is small (i.e. deep groove depth), put
an unfinished end into the Groover and complete the groove.
Recheck the groove diameter for conformance to grooving
specifications.
MODEL 3007 ONLY – Extremely Important
Check to see that the Ridgid* 300 drive directional switch is set to
"reverse"
position (clockwise rotation of the pipe looking at the front
of Groover.) Pipe must be square on ends.
Burrs or torch slag must be removed. Any pipe manufacturing seam, on
inside or outside of pipe, must be removed.
Using the pressure gauge mounted on the hydraulic ram maintain
approximately the listed grooving pressures for size and wall thickness
of pipe to efficiently form the groove.
*
“RIDGID” is a registered trade mark of Emerson Electric Company.