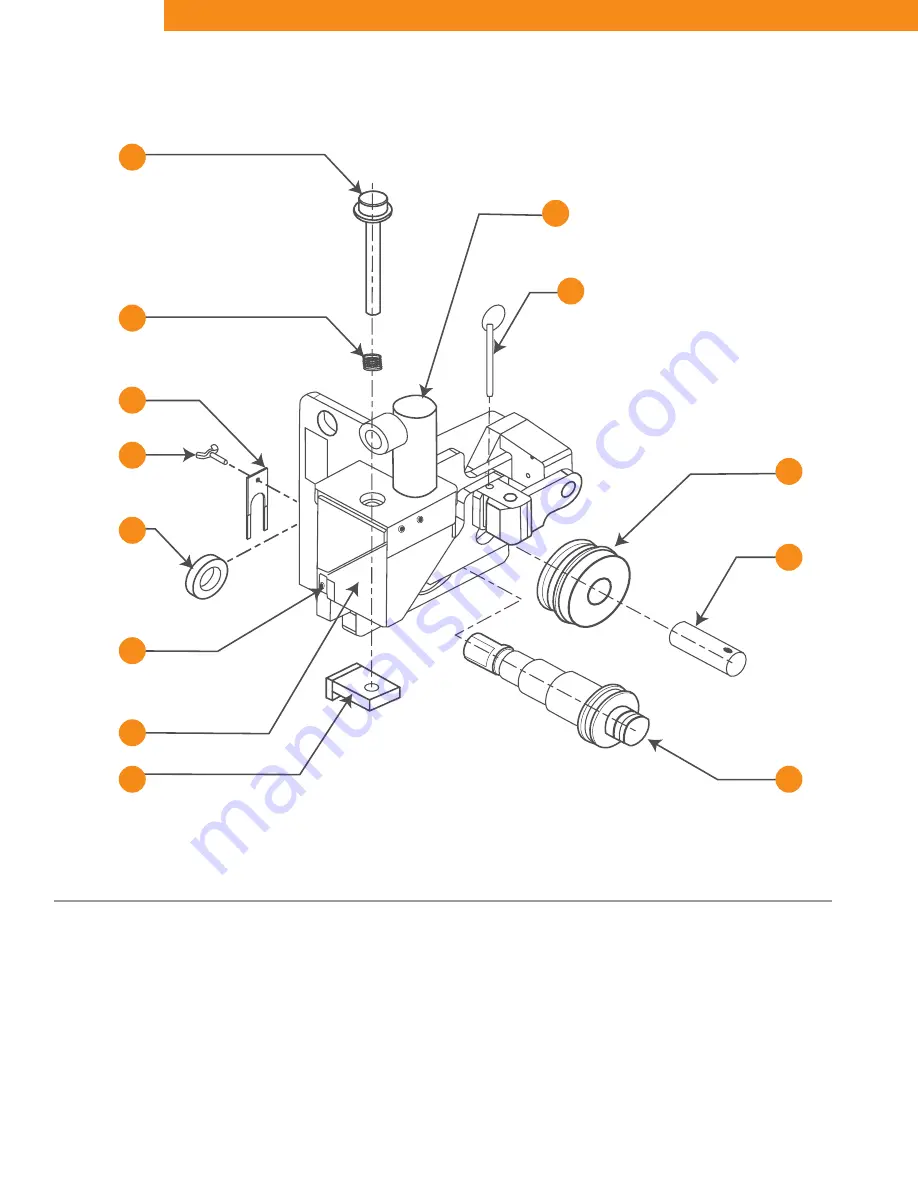
1007 & 3007 ROLL GROOVER
16
REPLACEMENT PARTS- 1007 & 3007 GROOVED HEAD
1
12
10
11
9
8
7
6
5
13
4
3
2
ID PART NAME
PART NO
1
Quick Release Pin
GL11775
2
Hydraulic Ram Assembly
GL11095
3 Knurled Stop Assembly
GL11035
4 Spring
GL11065
5 Thumb Screw
GL11056
6 Hinged Shaft Collar
GL11194
7 Cap Screw, 1⁄4"-20, L= 3/8"
GL11767
8 Safety Mesh
GL11313
9 Stop Plate Assembly
GL11467
ID PART NAME
PART NO.
10 Top Shaft
GL11039
11 Bottom Roller:
2"-6" Steel
GL11114
8"-12" Steel
GL11119
14"-16" Steel (OPT)
GL11337
2" -8" CTS Copper System (OPT) GL13801
12 Top Roller:
2"-6" Steel
GL11110
8"-12" Steel
GL11117
14"-16" Steel (OPT)
GL11335
2"- 8" CTS Copper System (OPT) GL13799
I
ID PART NAME
PART NO
13 Depth Gauge:
1"-3" Steel
GL11115
4"-6" Steel
GL11116
8"-12" Steel
GL11120
2"-4" CTS Copper System (OPT)
GL13850
5"-8" CTS Copper System (OPT)
GL13851
3 REQUIRED