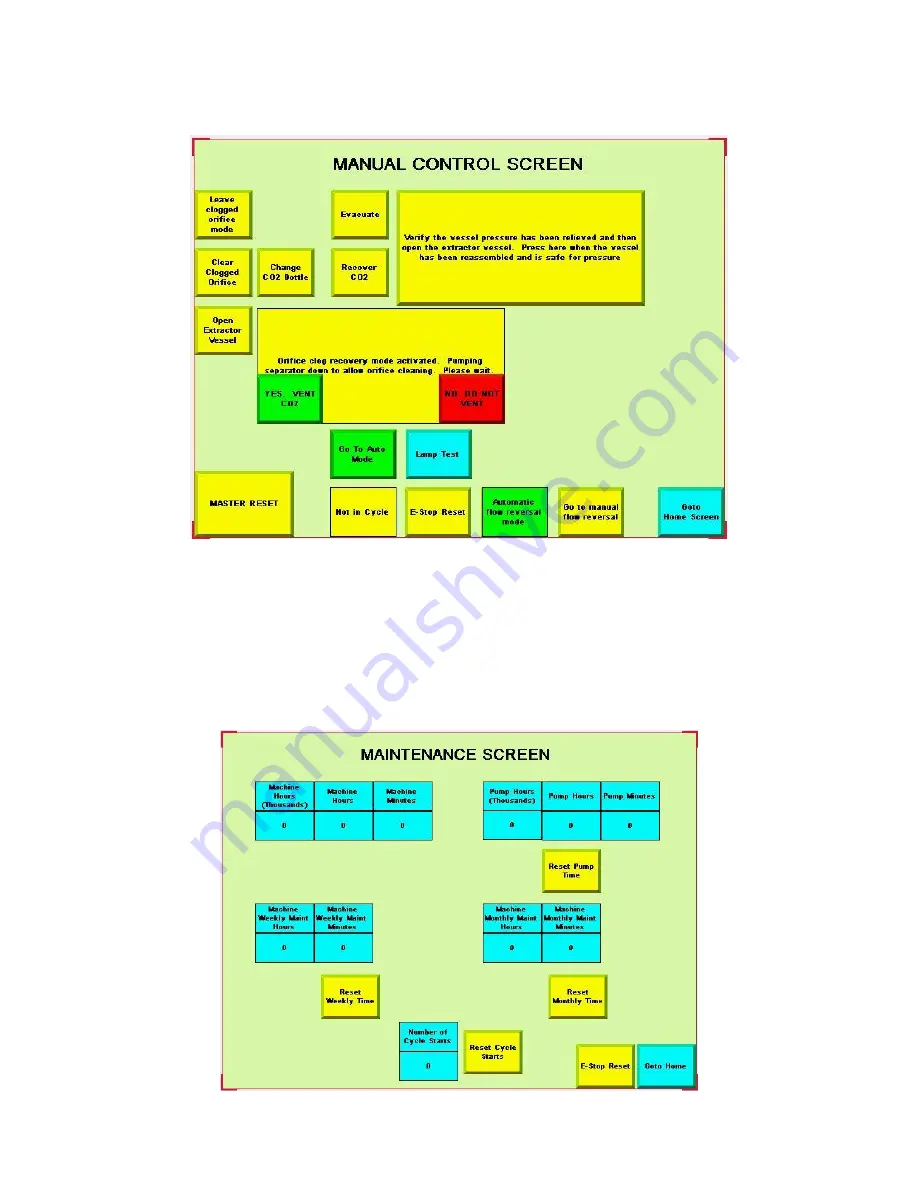
Updated 6/16/2016
Copyright Apeks LLC, 2014
44
5.1.33 On the manual screen, there's a button to switch between automatic flow reversal
and manual flow reversal. When in manual flow reversal mode, the operator can
press a button to switch the flow direction at any time during the run. (Figure
43a)
Figure 43b. Automatic Mode Selected
5.1.34 When in automatic flow reversal, the machine will only change flow direction
when a new extraction is started, meaning that forward flow at the beginning will
remain forward flow until the next run. The next run will be reverse flow and will
remain reverse flow for the entire run. (Figure 43b)
A.3. Maintenance Screen
The Maintenance Screen is rarely used. The Maintenance screen is where you will go to monitor run
times on your system and pump for scheduling and maintenance.
Figure 35. Maintenance Screen
Summary of Contents for 2000 PSI Series
Page 49: ...Updated 6 16 2016 Copyright Apeks LLC 2014 49 ...
Page 50: ...Updated 6 16 2016 Copyright Apeks LLC 2014 50 Appendix C CO2 Phase Diagram ...
Page 51: ...Updated 6 16 2016 Copyright Apeks LLC 2014 51 ...
Page 52: ...Updated 6 16 2016 Copyright Apeks LLC 2014 52 Appendix D Training Process ...