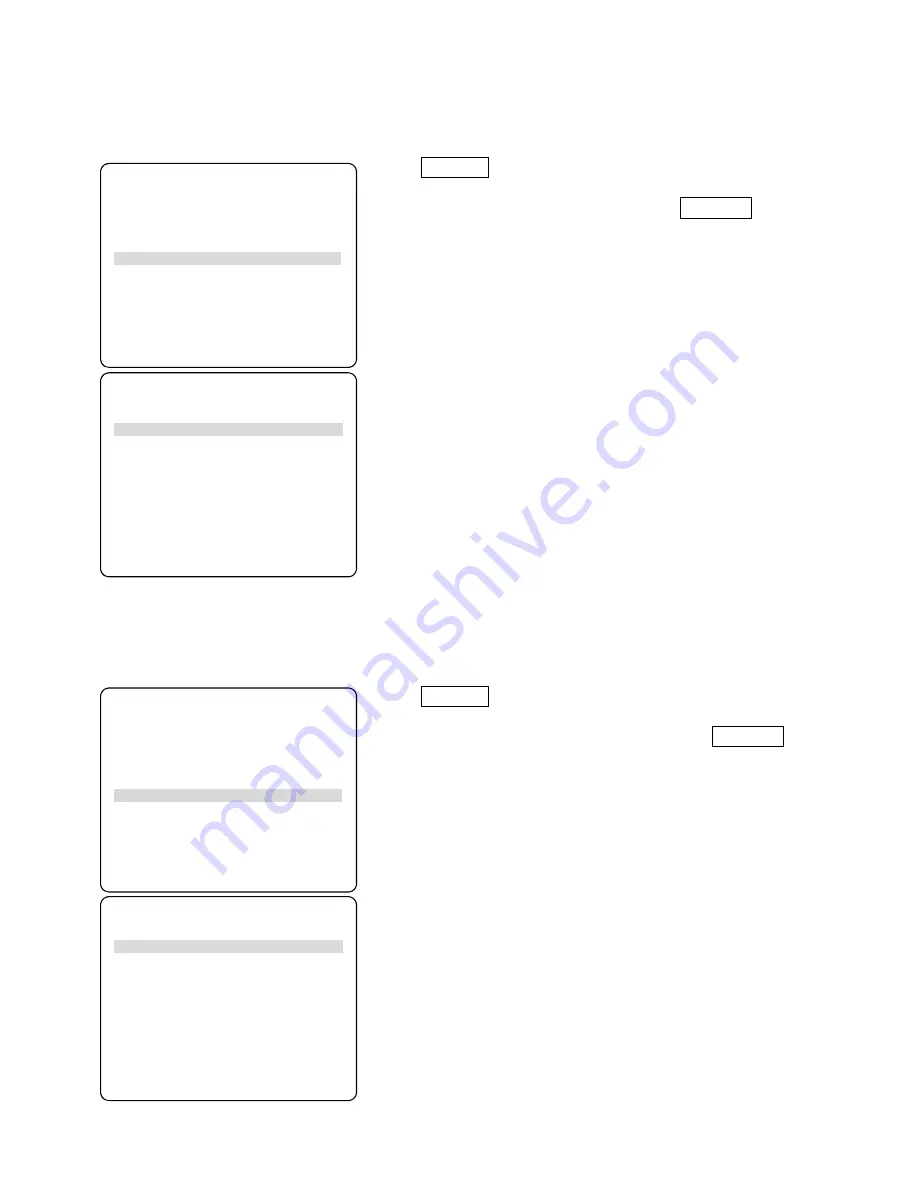
Page 46 of 60
19.4 Type of Restart
Restart setting can be selected in case of Solder shortage, Solder clogged, Heater error. There are
three types of restart setting, Same Point Restart, Next Point Restart, Program End. *Initial value:
“Program End”
Press MENU key at teaching mode, and select “Soldering
System Settings”.
Then, select “Type of Restart” and press ENTER .
Select restarting way.
Same Point Restart:
Restarting from the point that error occurs.
Next Point Restart:
Restarting from the next point that error occurs.
Program End:
Back to the home position and program ends.
19.5 Type of Error Reset
Error resetting that is by Start button on the robot or by inputting signal (I/O SYS) of external device
can be selected in case of Solder shortage, Solder clogged or Heater error occurs.
*Initial value : “START BUTTON”
Press MENU key at texching mode, and select “Soldering
System Settings”.
Then, select “Type of Error Reset” and press ENTER .
Select “START BUTTON” or “I/O SYS”.
START BUTTON:
Resetting by pressing the start button on the robot.
*Set “Switch Run Mode”.
I/O SYS:
Resetting by the external device.
*Set “External Run Mode”.
*It also outputs I/O SYS 9 at the error ouputting.
(Refer to 20. Function Assignment List)
Reset by the selected way, when error occurs.
Soldering System Settings
IO Function Assignment
Iron Shot Counter Disable
Cycle Count Disable
One Touch Feed Length 0mm
APN05 Alarm Display Disable
Type of Restart Program End
Type of Error Reset START BUTTON
Feeder Calibration 100%
Manual Feed Speed 50mm/s
Type of Restart
Same Point Restart
Next Point Restart
Program End
Soldering System Settings
IO Function Assignment
Iron Shot Counter Disable
Cycle Count Disable
One Touch Feed Length 0mm
APN05 Alarm Display Disable
Type of Restart Program End
Type of Error Reset START BUTTON
Feeder Calibration 100%
Manual Feed Speed 50mm/s
Type of Error Reset
START BUTTON
I/O SYS