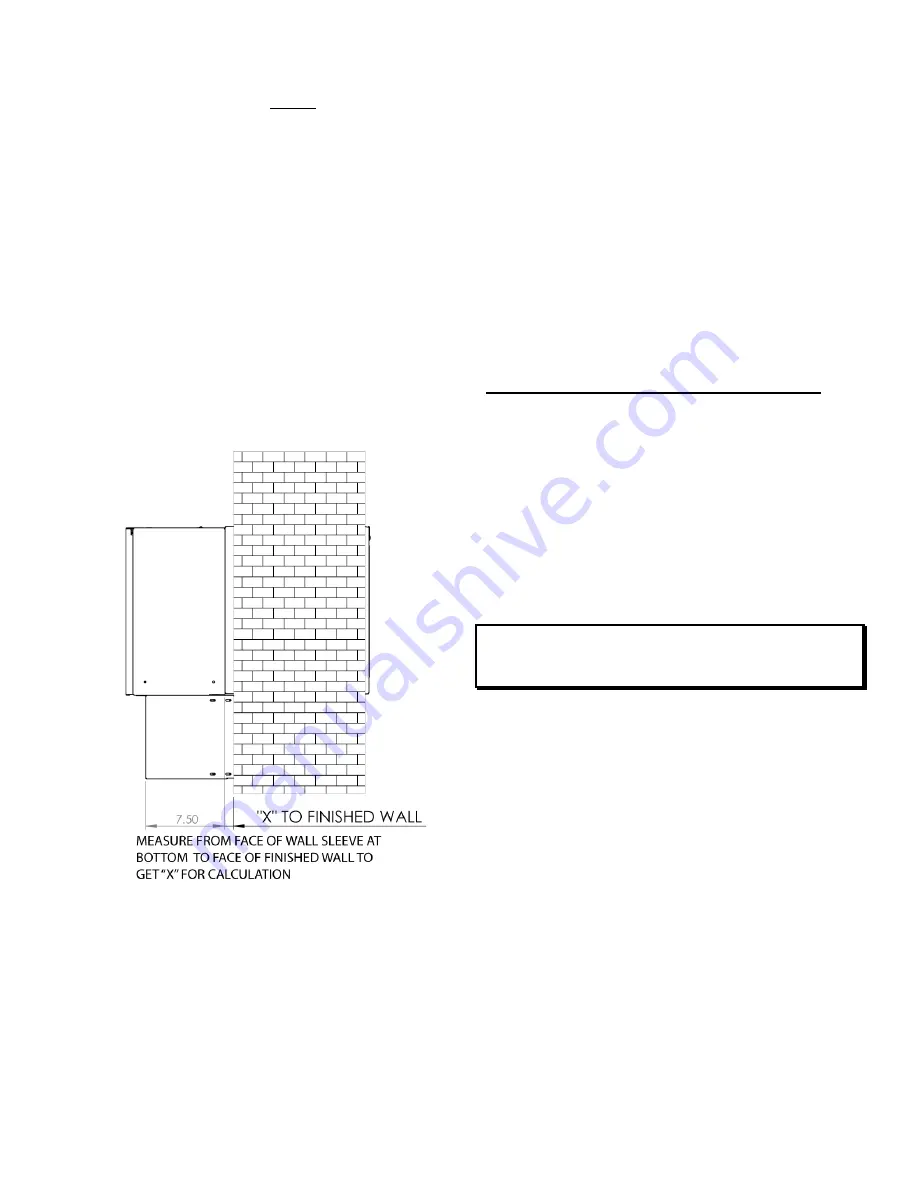
4
803809 Rev. 01
Adjust the side flanges as follows:
Measure the penetration of the bottom of the wall
sleeve into the room relative to the finished wall
surface, and record as “x”. Remove the grille cover
from the heating subbase by rotating the two ¼ turn
finger and thumb fasteners until the grille cover
releases. The total side length of the heating subbase
(cover removed) plus side channel closure is calculated
as 7.5 + “x”. Insert the side channels and secure with
the screws provided, set at the total side length
calculated. Center the subbase under the wall sleeve
opening and adjust the levelling feet to the anticipated
correct height. Final height adjustment can be made
after the wall sleeve is permanently installed. At that
point, the flanges of the side channels can be screwed
to the finished wall from inside the subbase if desired,
to anchor the entire heating subbase assembly in place.
The bottom of the wall sleeve will end up overlapping
the subbase by about 0.875 inches.
Plumbing Connections:
The heating coil is supplied with 5/8” O.D. (actual
diameter) copper tubing connections. Hot water heating
typically requires a Normally Open (NO) water valve, and
steam usually requires a Normally Closed (NC) steam
valve. The NFWC unit 24 VAC control output to the
valve is factory set for NC but can be field-converted to
NO duty as described in Section
Heating/Cooling Chassis
Installation.
Remove the cover plate on the right hand side of the
heating coil to provide better access to the copper
connection tubes. Always pipe the valve to the supply
connection. If the heating medium is hot water, connect
the valve “outlet” (Supply) to the lower connection and
the Return water to the upper connection. If the heating
medium is steam, connect the valve “outlet” (Supply) to
the upper connection and the Return to the lower
connection. Route the steam or water source to the valve’s
“inlet” connection.
Install the piping, valve, and accessories (as specified by
the design engineer) in the space available under the
heating coil.
ELECTRICAL WIRING AND RECEPTACLE
Wire Sizing
A single outlet branch circuit from the main electrical
panel to the receptacle in the subbase should be used.
Wire sizing shall be in accordance with the minimum
circuit ampacity as declared on the unit Rating Plate for
the specific chassis. Wire sizing must also take into
account any distance from fuse box or breaker panel to
receptacle to prevent excessive voltage drop in
undersized wires.
IMPORTANT:
Low voltage to the unit will cause
compressor starting problems and decrease the
performance and reliability of the compressor.
Branch Circuit Protection
The Current Rating of branch circuit protection using a
Time Delay Fuse or HACR circuit breaker should also
be as declared on the unit Rating Plate for the specific
chassis being installed.
Plug and Receptacle
All 230-208 Volt units are normally furnished with a
NEMA 6-20P, 20 Amp non-locking plug, and hence
will require a NEMA 6-20R receptacle to be installed
in the heating subbase.
All 115 Volt units are furnished with a NEMA 5-15P,
or 5-20P non-locking plug as applicable. The
respective plug will require a NEMA 5-15R or
combination 5-20R receptacle to be installed in the
heating subbase.