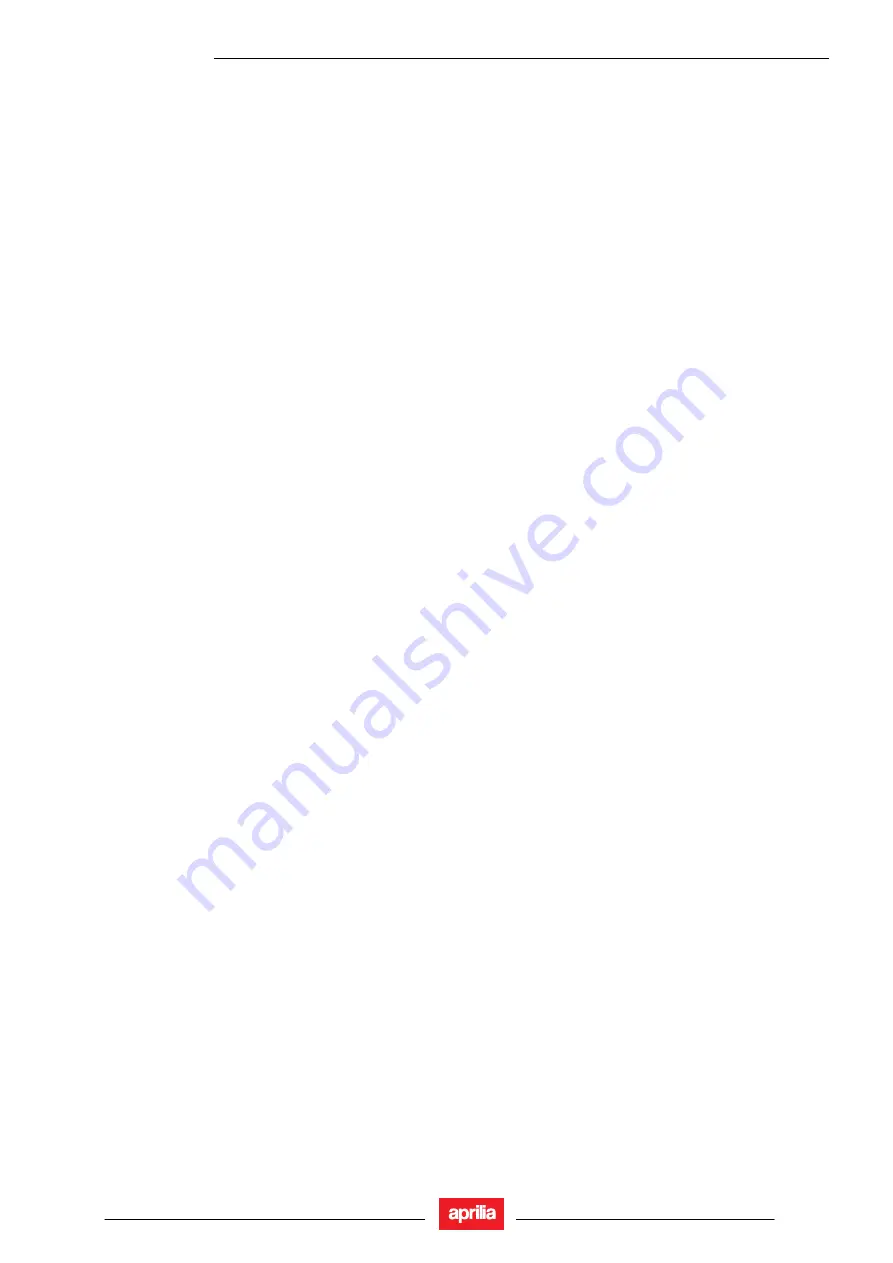
GENERAL TECHNICAL INFORMATION
2 - 37
PEGASO 650
Labelling
A label should be stuck at the back of every component; it
shall be indelible and water proof, indicating the following
details:
•
supplier code
•
Aprilia code
•
hardware board version
•
software version
•
production date
The Supplier shall add more labels for DOT certification or
immobilizer system homologation.
Summary of Contents for Pegaso 650 2005
Page 1: ...INTRODUCTION 0 1 PEGASO 650 INTRODUCTION 0 ProCarManuals com ...
Page 7: ...GENERAL INFORMATION 1 1 PEGASO 650 GENERAL INFORMATION 1 ProCarManuals com ...
Page 71: ...FUEL SYSTEM 3 1 PEGASO 650 FUEL SYSTEM 3 ProCarManuals com ...
Page 78: ...ENGINE 4 1 PEGASO 650 ENGINE 4 ProCarManuals com ...
Page 96: ...ENGINE 4 19 PEGASO 650 Bend the safety washer Refit the guide plate ProCarManuals com ...
Page 105: ...CYCLE PARTS 5 1 PEGASO 650 CYCLE PARTS 5 ProCarManuals com ...
Page 124: ...CYCLE PARTS 5 20 PEGASO 650 Remove the shim Remove the top sliding bush ProCarManuals com ...
Page 131: ...WIRING DIAGRAM 6 1 PEGASO 650 WIRING DIAGRAM 6 ProCarManuals com ...
Page 138: ...WIRING DIAGRAM 6 8 PEGASO 650 6 1 2 WIRING DIAGRAM ProCarManuals com ...