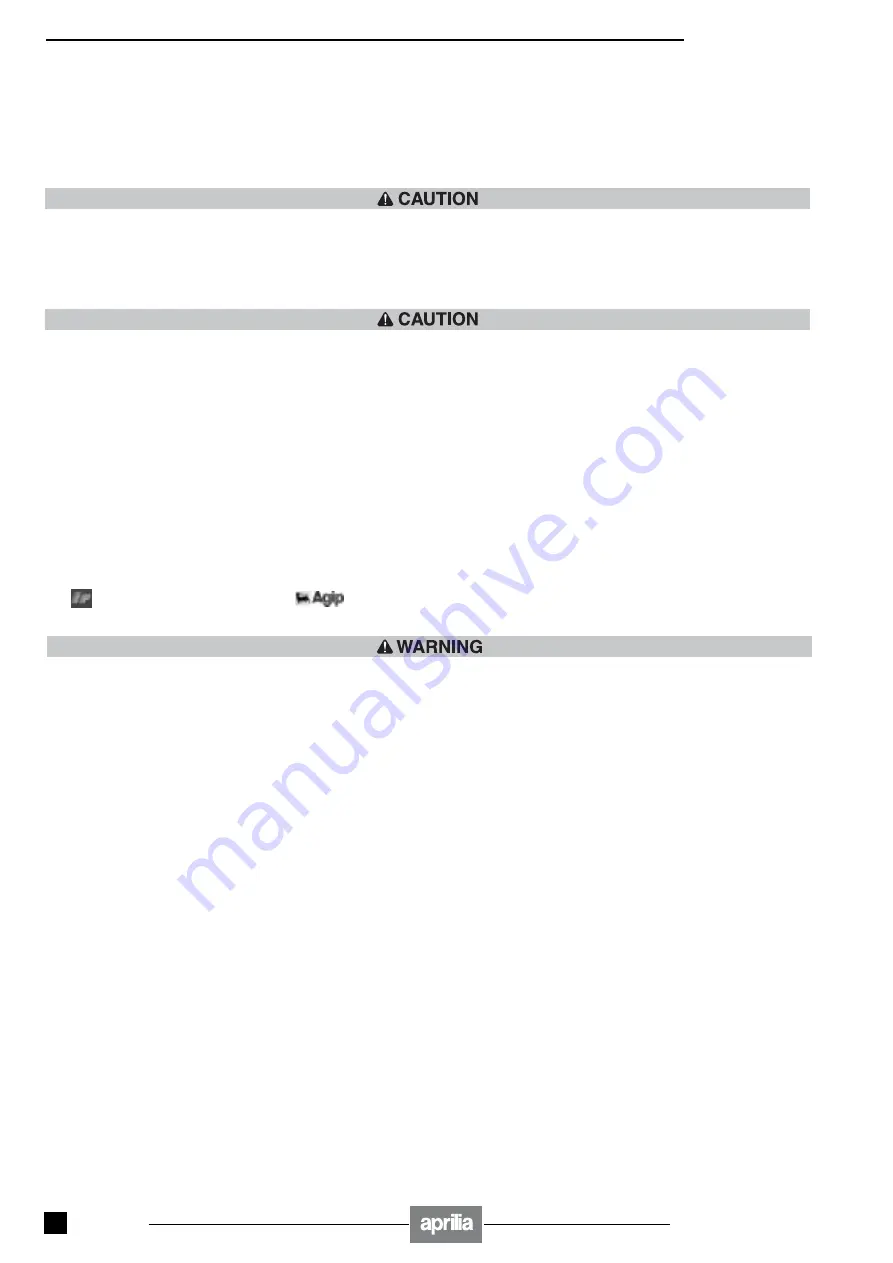
GENERAL INFORMATION
QUASAR 125-180
1
- 4 -
00
Release 00/2003 - 09
1.3
GENERAL SAFETY RULES
1.3.1
CARBON OXIDE
When an operation must be performed with the engine running, position the motorcycle out of doors or in a well-ventilated area.
Never operate the engine indoor.
Use an exhaust emission extraction plant when working indoor.
Exhaust emissions contain carbon oxide, which is a poisonous gas and may lead to loss of conscience or even death.
Operate the engine out of doors or, if working indoors, use an exhaust emission extraction plant.
1.3.2
FUEL
The fuel used to operate engines is highly flammable and becomes explosive under particular conditions.
Refuelling and engine service should take place in a well-ventilated area with the engine stopped.
Do not smoke when refuelling or in the proximity of sources of fuel vapours. Avoid contact with bare flames, sources of
sparks or any other source which may ignite the fuel or lead to explosion.
DO NOT RELEASE FUEL INTO THE ENVIRONMENT.
KEEP AWAY FROM CHILDREN.
1.3.3
HOT COMPONENT PARTS
The engine and exhaust component parts become hot when the engine is running and will stay hot for some time after the engine
has been stopped.
Wear heat gloves before handling these components or allow for the engine and exhaust system to cool down before proceeding.
1.3.4
TRANSMISSION OIL
Use
PONTIAX HDI SAE 85W - 140 or
POTRAIMP 85W-140. As an alternative to recommended fluids it is possible to
use high-quality fluids having equal or higher ratings with respect to A.P.I. GL-4 specifications.
Insufficient lubrication or the use of unsuitable lubricants may result in irreparable damage due to increased wear and
tear of the moving parts.
Do not overtighten the drain plug as this could damage the crankcase.
Used oil contains substances that are harmful to the environment, even small quantities must be disposed of in compli-
ance with the regulations in force.
To avoid serious skin damage due to prolonged contact with oil, accurately wash your hands after handling the lubri-
cant.
KEEP AWAY FROM CHILDREN.
Summary of Contents for QUASAR 125 2003
Page 9: ...FOREWORD QUASAR 125 180 0 8 00 Release 00 2003 06 NOTE ProCarManuals com ...
Page 25: ...GENERAL INFORMATION QUASAR 125 180 1 16 00 Release 00 2003 09 NOTE ProCarManuals com ...
Page 49: ...PERIODIC MAINTENANCE QUASAR 125 180 2 24 00 Release 00 2003 09 NOTE ProCarManuals com ...
Page 50: ...QUASAR 125 180 ENGINE 3 1 00 Release 00 2003 09 3 ENGINE ProCarManuals com ...
Page 97: ...ENGINE QUASAR 125 180 3 48 00 Release 00 2003 09 NOTES ProCarManuals com ...
Page 98: ...QUASAR 125 180 FUEL SYSTEM 4 1 00 Release 00 2003 09 4 FUEL SYSTEM ProCarManuals com ...
Page 103: ...FUEL SYSTEM QUASAR 125 180 4 6 00 Release 00 2003 09 NOTES ProCarManuals com ...
Page 104: ...QUASAR 125 180 ELECTRIC SYSTEM 5 1 00 Release 00 2003 09 5 ELECTRIC SYSTEM ProCarManuals com ...
Page 129: ...ELECTRIC SYSTEM QUASAR 125 180 5 26 00 Release 00 2003 09 NOTES ProCarManuals com ...
Page 130: ...QUASAR 125 180 CYCLE PARTS 6 1 00 Release 00 2003 09 6 CYCLE PARTS ProCarManuals com ...
Page 157: ...CYCLE PARTS QUASAR 125 180 6 28 00 Release 00 2003 09 NOTES ProCarManuals com ...
Page 158: ...QUASAR 125 180 TROUBLESHOOTING 7 1 00 Release 00 2003 09 7 TROUBLESHOOTING ProCarManuals com ...
Page 166: ...TROUBLESHOOTING QUASAR 125 180 7 9 00 Release 00 2003 09 NOTE ProCarManuals com ...
Page 167: ...TROUBLESHOOTING QUASAR 125 180 7 10 00 Release 00 2003 09 NOTE ProCarManuals com ...