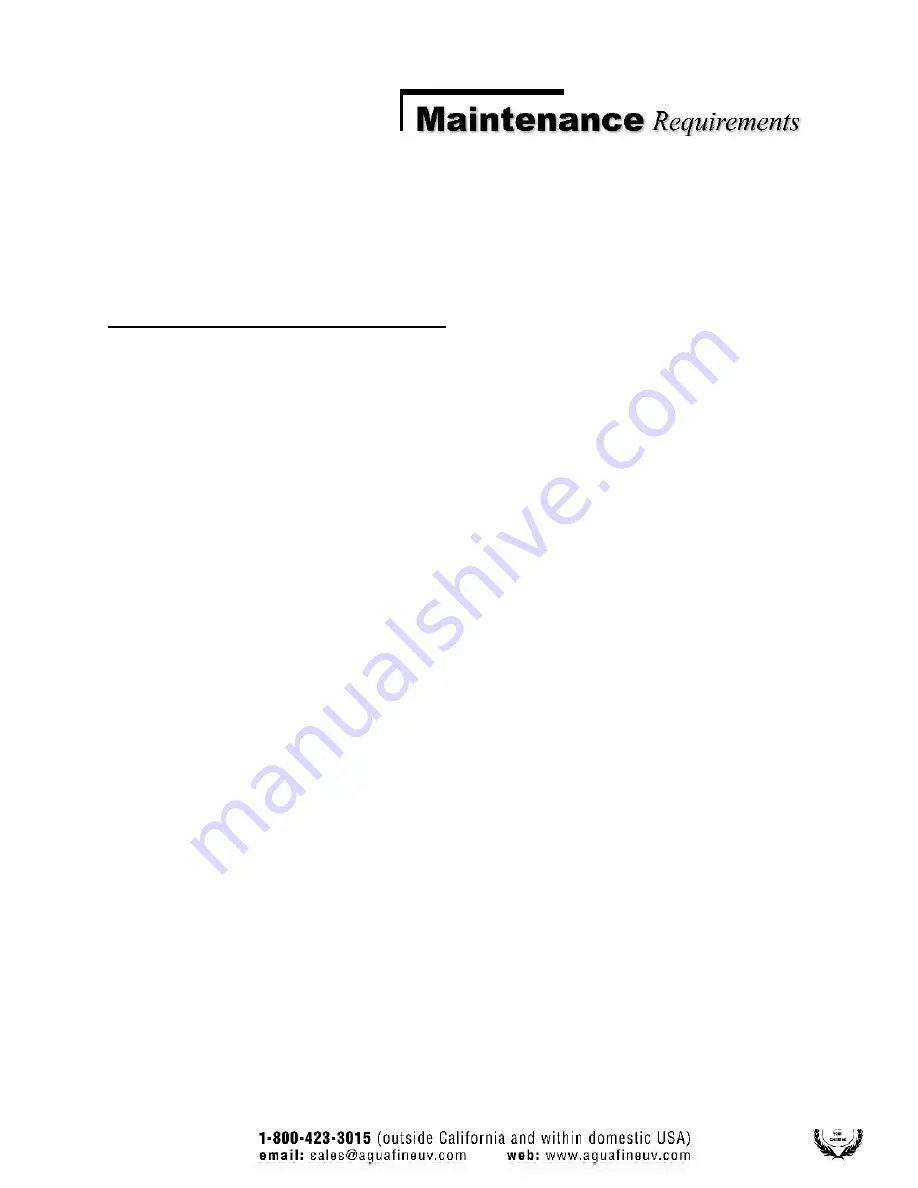
17
We have provided
1
/
4
” NPT threaded fittings on both
the intake and discharge UV chamber flange risers. We
recommend you use these fittings to collect “before and
after UV” water samples to eliminate the possibility of
contamination by nearby piping, fittings, etc.
We recommend you select a valve with a discharge
orifice no larger than
1
/
4
” (6 mm).
sampling procedures
The following procedure is recommended for collecting
samples for bacteriological analysis when sample valves
are installed:
1. Prior to taking the water sample, have on hand an
adequate supply of sterile bottles. These should be
obtained from a source laboratory and should have
been autoclaved and contained within a plastic outer
wrapping.
2. The inside diameter of a sample valve must not exceed
1
/
4
” (6 mm) to ensure proper velocity. Prior to taking
the sample, it is imperative that the test sample valve
be fully opened under full pressure for a full three and
one half minutes. Temporary tubing or some other
material may be used to direct the water to a container
or drain to avoid unnecessary spillage.
3. After the valve has been left fully open for three and
one half minutes, reduce the flow to a reasonable
stream of water (not less than 50% of full flow).
Continue flowing to drain three additional minutes.
4. Remove any temporary tubing used for flow diver-
sion.
5. Open the sterile bottle. Holding the cap in a down
position, the operator should then hold his breath
while taking the sample so as to avoid atmospheric
contamination of the sample. The operator must also
not allow his finger to touch the inside of the cap or
the neck of the bottle.
6. After the water sample has been taken, the cap should
be immediately secured on the sample container.
7. The sample container should be labeled and placed in
a plastic wrapping and must be taken to the laboratory
for plating as soon as possible. Processing should
begin within three hours of sample collection and
should comply with accepted standard methods.
The above procedure was developed by a leading national
pharmaceutical firm after an 18-month study. It has been
more
found that virtually all removable debris which may
accumulate within a sample valve can be mechanically
flushed during the procedures detailed above.
We recommend duplicate samples be taken at each test
station, during each specific test, to avoid laboratory
error and to ensure reasonable repeatability and validity
through comparison.
Summary of Contents for MP-2-SL
Page 2: ......