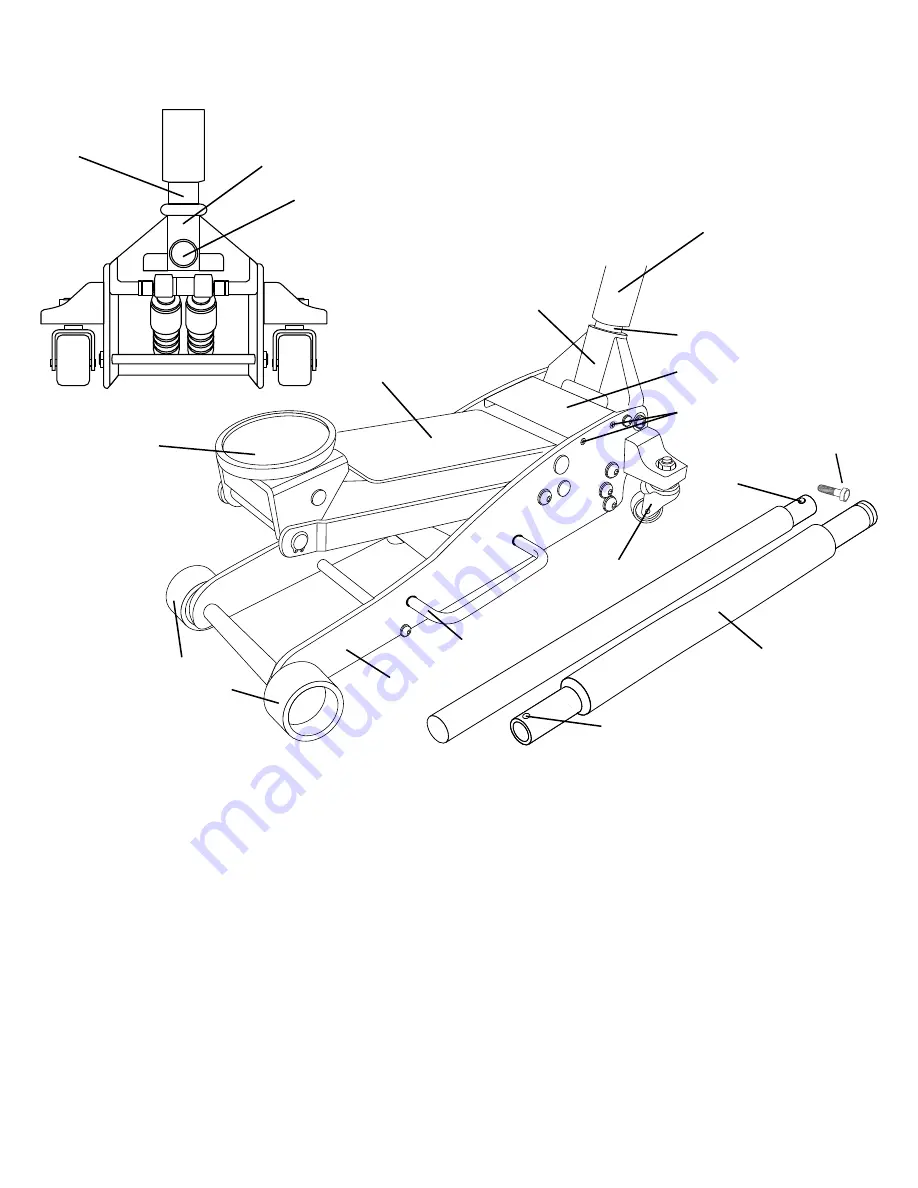
HJ1800AU User Manual
2
rev. 041814
INSPECTION
Visual inspection should be made before each use of the jack, checking for leaking hydraulic fluid and damaged, loose or missing parts. Any
jack which appears to be damaged in any way, is found to be badly worn, or operates abnormally MUST BE REMOVED FROM SERVICE
until necessary repairs are made.
SETUP
1
.
Remove 2-piece handle from box. Insert narrow portion of top handle into bottom handle, align top and bottom bolt holes, and secure with handle
bolt provided.
2. Grease the inside of the handle yoke so the handle will rotate freely inside the yoke. Remove the handle yoke screw. Insert the end of the lower handle
all the way in the handle yoke until it engages the release valve assembly. Secure the handle in the handle yoke by reinstalling the handle yoke screw
and tightening the screw. Rotate the handle to see if it is rotating the release valve assembly. Pull on the handle to make sure it is secured in the handle
yoke. If the release valve assembly is not rotating and/or the handle pulls out of the handle yoke, repeat step 2.
3. IMPORTANT: In most cases the jack should work normally right out of the box but it is not unusual for air to get trapped in the jack’s hydraulic system
during shipping and handling. There are several symptoms of an air trapped hydraulic system which include only partial incremental pump stroke,
jack will not lift load, jack will not sustain load or pumping feels spongy under load. The following procedure will purge air from the hydraulic system
and only needs to be done if experiencing the above mentioned conditions.
a) The saddle should be in its lowest position. Remove the four screws that secure the cover plate to the jack frame so the oil filler screw can be
removed from the hydraulic power unit reservoir tube.
b) Look inside the oil fill screw hole. You should be able to see the top of the power unit’s cylinder. The hydraulic fluid level should be no higher
than the top of the cylinder. Correct the fluid level if it is not at the proper height. CAUTION: In order to prevent seal damage and jack failure,
never use alcohol, hydraulic brake fluid, or transmission oil in the jack. Use hydraulic jack oil, a light turbine oil, Chevron Hydraulic Oil AW ISO
32 or Unocal Unax AW 150.
c) Close the release valve by turning the handle clockwise until it stops. Pump the jack against a load of at least 500 pounds (225 Kgs). After
the load is raised to maximum height, slightly turn the handle in a counterclockwise direction so the load is very slowly lowered, while
simultaneously and quickly pumping the handle 5 or 6 full incremental pump strokes. After pumping, lower the lift arm to its full rest position.
d) Install the oil fill screw. Rotate the handle in a clockwise direction until tight and pump the lift arm to maximum height without a load. Repeat steps
a) through d) until all the air has been purged from the system. Reinstall the cover plate.
IMPORTANT: Before attempting to raise any vehicle, check vehicle service manual for recommended lifting surfaces.
Saddle
Chassis
Side Handle
Lift Arm
Handle
Bumper
Handle Yoke Screw
Handle
Handle
Yoke
Handle
Yoke
Handle
Cover Plate
Screws
Rear
Casters
Upper
Handle
Hole
Lower
Handle
Bumper
Lower Handle Hole
Front
Wheels
Handle
Bolt