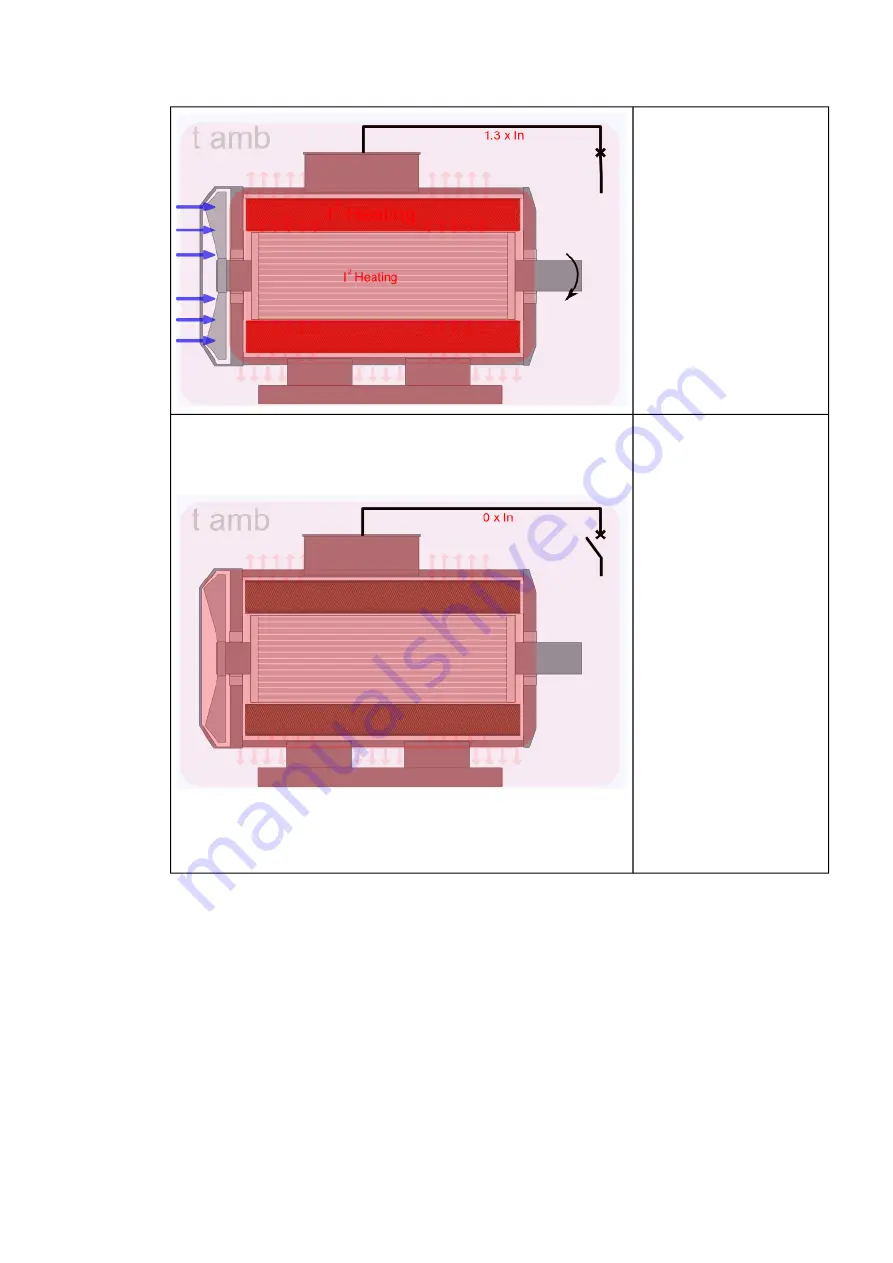
If the motor is overloaded, the
stator winding starts to heat up
according to its heating time
constant. If the overload is not
released in time, it can lead to the
melting of the stator's winding
insulations which in turn leads to a
short-circuit; the motor is said to
"burn". This situation does not differ
much from the rotor's nominal
conditions. When the load
increases, the slip increases slightly
as well and causes a small increase
to the induced voltage and current.
However, when rotating the heating
does not differ significantly from the
nominal load.
When a hot motor is de-energized
the temperatures inside the motor
start to stabilize. The hottest part
of the motor is the rotor: its heat is
transferred to the motor body
through the stator windings and
from the body to the surrounding
air. This is why it seems that the
motor body's temperature keeps
rising even after a surface-cooled
motor is stopped. The stopped
motor cooling follows the same
equation than heating, with one
exception: when the surrounding
air is not moving (as the fan has
stopped) and the air temperature
is increasing, the cooling is faster in
the beginning and slows over time
as the temperature difference
decreases (since heat is transferred
slower than in the beginning of the
cooling). When the motor is run
with a cyclic load, the start and
stop applications for the cooling of
the motor have to be modeled
accurately in the thermal replica in
order to avoid a situation where the
calculated used thermal capacity
"runs" from the actual used thermal
capacity causing the protection to
overshoot significantly.
The previous figures presented the thermal behavior of a motor on a theoretical level. In reality, the
temperature of a rotor inside the motor windings can also be measured with RTD elements. The rotor
temperature is highest on the drive end becuase the cooling is the weakest there (as can be seen in
the image below).
A
AQ
Q-M215
-M215
Instruction manual
Version: 2.04
264