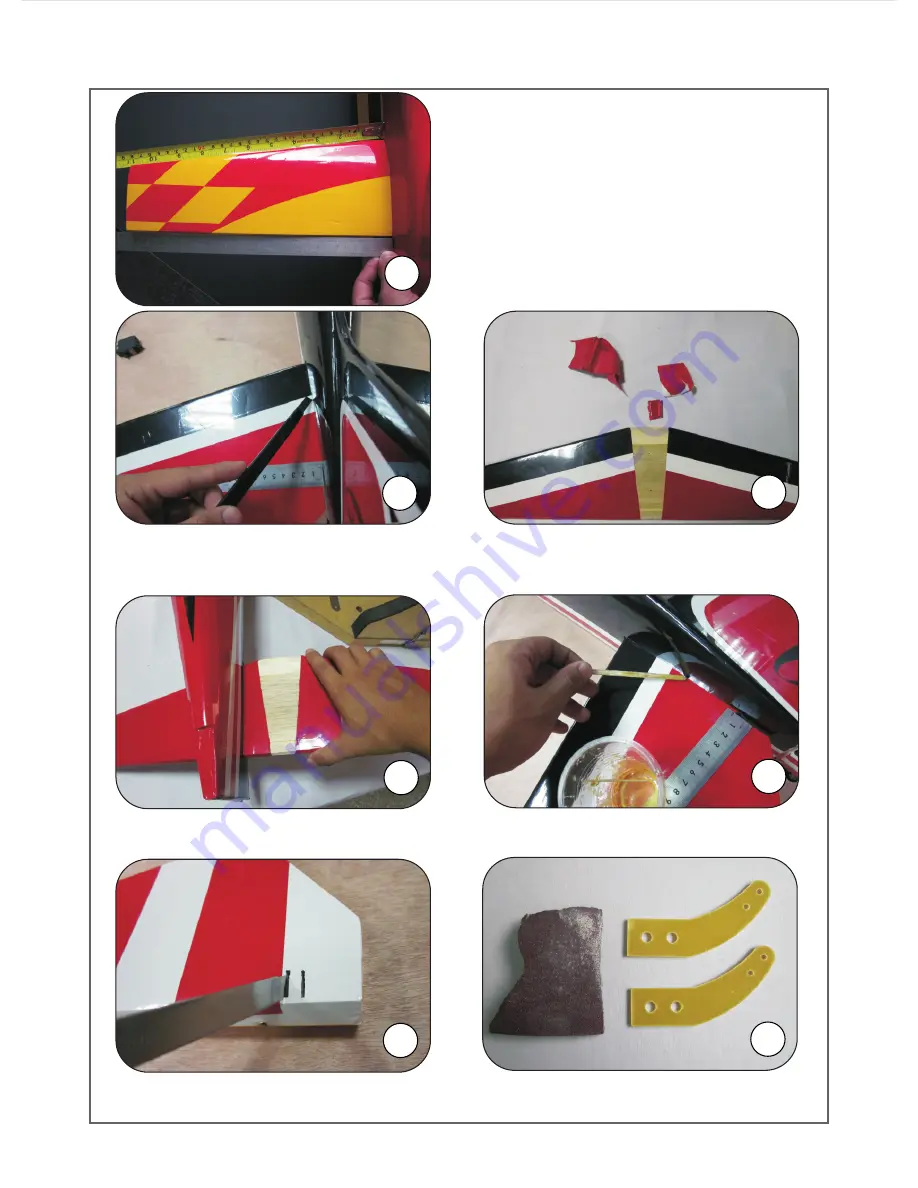
4.Remove the covering below to expose the pre-cut slots with a knife. Scuff
the
horns
with
sand
paper
to
ensure
a
good
glue
bond
.
1.
Insert
the
stab
into
the
fuselage
tail
.
Measure
the
stab
to
find
the
middle
.
3
.
Coat the horns with epoxy
.
Insert them into the fuselage
again
.
Make
sure
the
stab
is
symmerical
.
09
2 1
1
2 1
.
4 2
.
2 1
.
4 1
.
2
.
Mark
the
stab
with
a
pen
when
the
stab
is
symmerical
.
Trace around
the fuselage with a knife and remove the covering below to expose the
board
.
Take
care
not
to
scratch
the
board
.
2 1
.
3 1
.
2 1
.
2 1
.
2 1
.
2 2
.
2 1
.
3 2
.
Stab
and
Elevator
Installtion