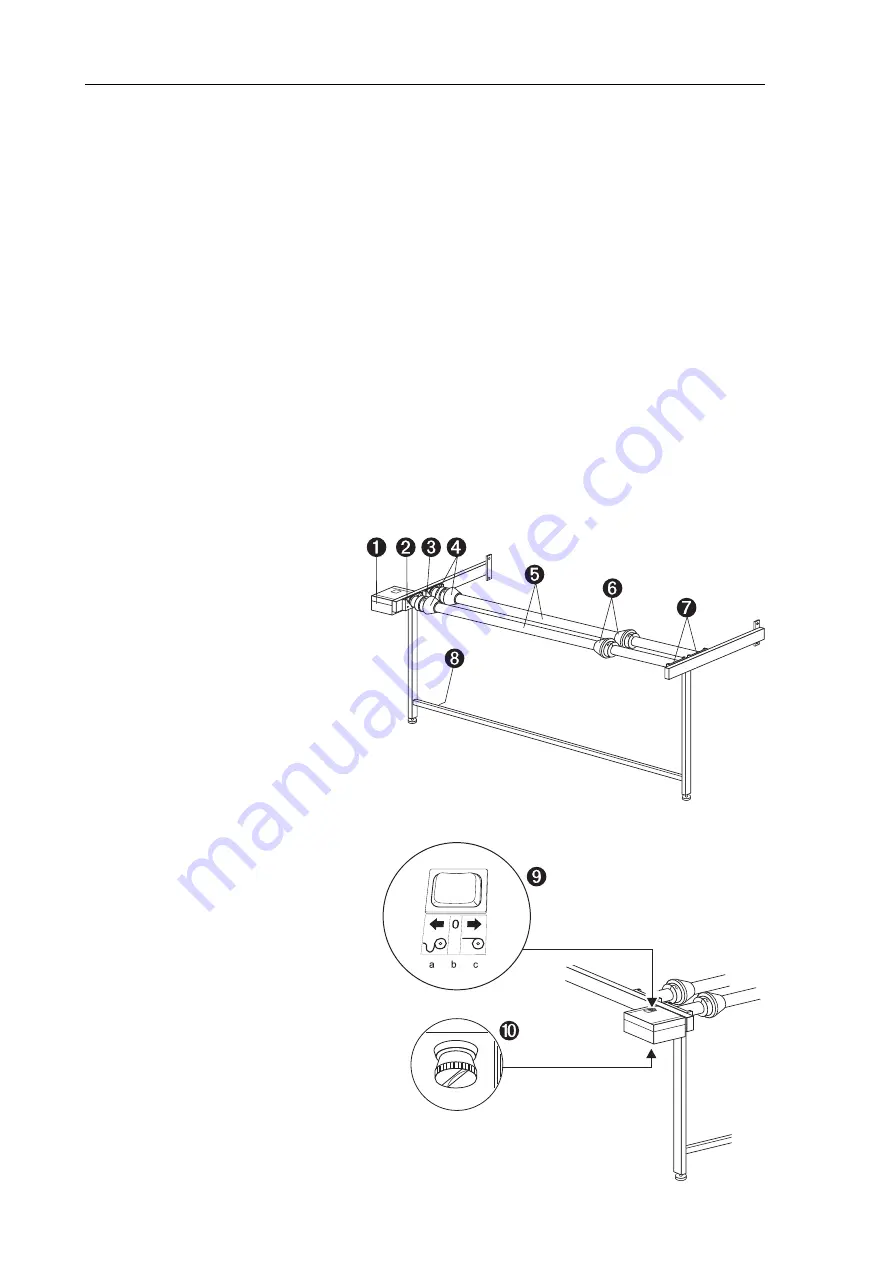
3-14
Material transport systems
Material winding systems
Motorized unroll device - MRA2 13xx, MRA2 16xx
Overview
Properties of suitable rolls:
- core diameters:
from 65 - 90 mm (2.55 to 3.5 in)
- outer roll diameter: max. 300 mm (11 3/4 in)
- max. roll width with: ARISTOMAT 13xx is 1400 mm (55 in)
ARISTOMAT 16xx is 1700 mm (67 in)
ARISTOMAT 13xx Conveyor is 1250 mm (49 in)
ARISTOMAT 16xx Conveyor is 1550 mm (61 in)
- max. roll weight:
70 kg (154 lbs)
1 electronic control
2 bearing bracket with drive slot
3 bearing bracket
4 support cone
5 unwind / wind shaft
6 support cone
7 bearing brackets
8 reflector for light barrier
9 mode select switch
switch settings:
a
= winding up (automatic)
b
= OFF/switched off
c
= unwind (manually by
holding the switch)
10 fuse 5x20 mm
(fine, 2A medium)
Summary of Contents for ARISTOMAT SL 1310
Page 1: ...Chapter 1 General ARISTOMAT SL 131O 1317 1617 1625 ...
Page 4: ...1 4 ARISTOMAT SL Series Contents ...
Page 12: ...1 12 ARISTOMAT SL Series Caution Areas ...
Page 14: ......
Page 16: ......
Page 17: ...Basic Elements of the ARISTOMAT SL 131O 1317 1617 1625 User s Manual Chapter 2 ...
Page 18: ... 2004 by ARISTO Graphic Systeme GmbH Co KG Issue Januar 2004 Article No 00001 8898 E ...
Page 22: ...2 6 Basic Elements of the ARISTOMAT SL Contents ...
Page 34: ...2 18 Basic Elements of the ARISTOMAT SL Menu Overview Main Menu ...
Page 35: ...Basic Elements of the ARISTOMAT SL 2 19 Menu Overview Menu Level 1 ...
Page 36: ...2 20 Basic Elements of the ARISTOMAT SL Menu Overview Menu Level 2 ...
Page 37: ...Basic Elements of the ARISTOMAT SL 2 21 Menu Overview Menu Level 3 ...
Page 59: ...Material transport systems for ARISTOMAT SL User s Manual Chapter 3 ...
Page 60: ... 2004 by ARISTO Graphic Systeme GmbH Co KG Issue Januar 2004 Article No 00001 8897 E ...
Page 86: ...3 28 Material transport systems Vacuum systems ARISTOMAT SL 131O ...
Page 87: ...Material transport systems 3 29 Vacuum systems ARISTOMAT SL 1317 ...
Page 88: ...3 30 Material transport systems Vacuum systems ARISTOMAT SL 1617 ...
Page 91: ...Material transport systems 3 33 Vacuum systems ARISTOMAT SL 1317 ...
Page 110: ...3 52 Material transport systems Malfunctions ...
Page 111: ...Chapter 12 ARISTOMAT SL Safety Devices User s Manual ...
Page 112: ... 2005 by ARISTO Graphic Systeme GmbH Co KG Issue August 2005 Article number 0000 18857 E ...
Page 122: ...12 12 Safety Devices for ARISTOMAT SL Maintenance ...