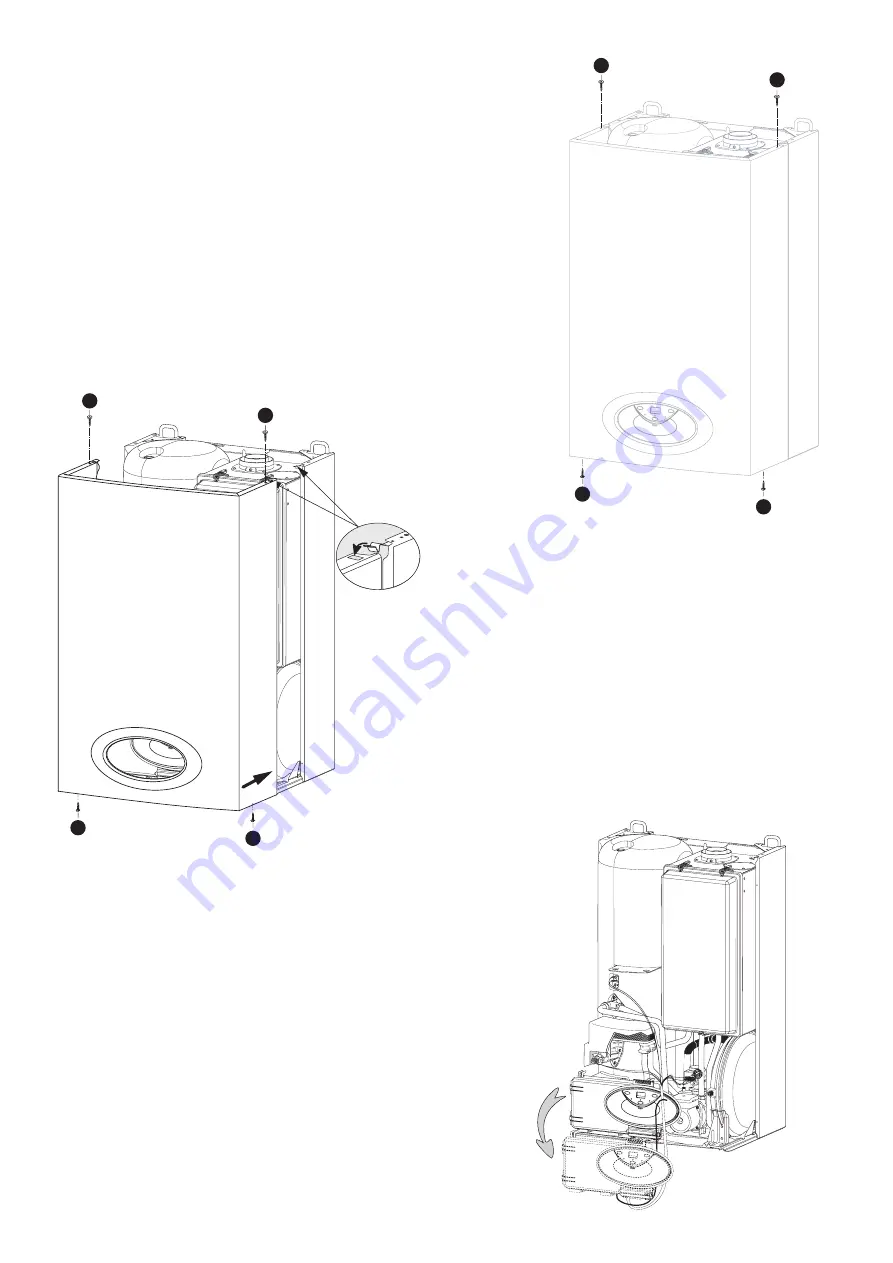
36
15.3
Removal and fitting of the case Servicing
Removal of the case
- undo the 4 case retaining screws (Fig. 15.2)
- disengage the clips
- remove the case
Fitting the case
Remove the protective film from the front and
rear of the case
- position the case (Fig. 15.3)
- engage both clips in the case (see detail)
- fasten the 4 retaining screws
A
on the front
Servicing
To maintain the unit, it is possible to move the electrical
box without having to disconnect it. The electrical box
is clipped onto the heating outlet pipe or onto the
bottom of the chassis. (Fig. 15.4)
A
A
A
A
A
A
A
A
detail
F
IG
. 15.2
F
IG
. 15.3
F
IG
. 15.4