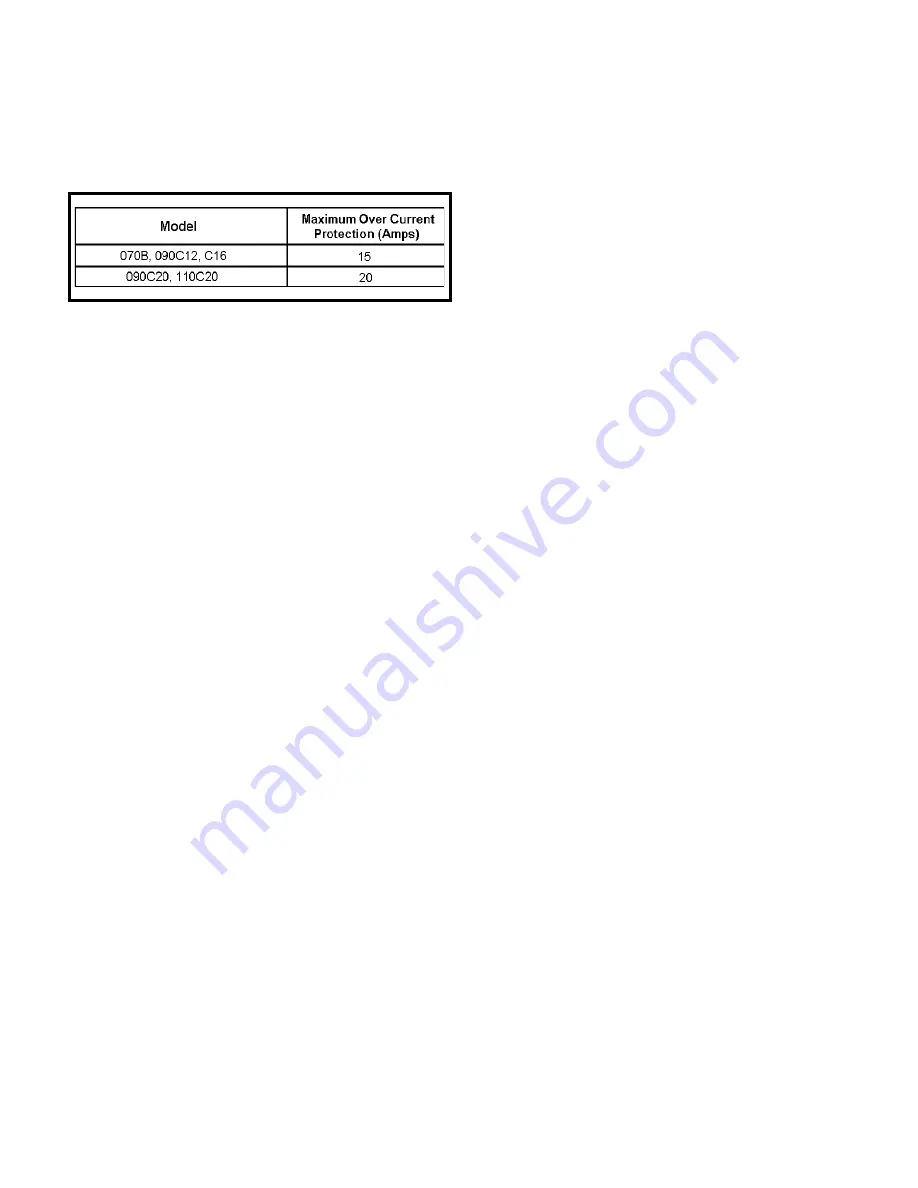
507029-03
Page 31 of 68
Issue 1622
NOTE:
Unit nameplate states maximum current draw. See
table for maximum over-current protection.
2. Holes are on both sides of the furnace cabinet to
facilitate wiring.
3. Install a separate (properly sized) disconnect switch
near the furnace so that power can be turned off for
servicing.
4. Before connecting the thermostat check to make sure
the wires will be long enough for servicing at a later date.
Make sure that the thermostat wire is long enough to
facilitate future removal of blower for service.
5. Complete the wiring connections to the equipment. Use
the provided unit wiring diagram and the field wiring
diagram shown in Figure 40 and Table 11. Use 18
gauge wire or larger that is suitable for Class II rating
for thermostat connections.
6. Electrically ground the unit according to local codes or,
in the absence of local codes, according to the current
National Electric Code (ANSI/HFPA No. 70) for the
USA and current Canadian Electric Code Part 1 (CSA
standard C22.1) for Canada. A green ground wire is
provided in the field make up box.
7. One line voltage “EAC” 1/4” spade terminal is provided
on the furnace integrated control. Any electronic air
cleaner or other 120V accessory rated up to
one amp
can be connected to this terminal with the neutral leg
of the circuit being connected to one of the provided
neutral terminals. See Figure 45 for location of terminal.
This terminal is energized when the indoor blower is
operating.
8. One line voltage “hum” 1/4” spade terminal is provided
on the furnace integrated control. Any humidifier rated
up to one amp can be connected to this terminal with the
neutral leg of the circuit being connected to one of the
provided neutral terminals. See Figure 46 for location
of terminal. This terminal is energized in the heating
mode when the indoor blower is operating.
9. One 24V “H” terminal is provided on the furnace
integrated control terminal block. Any humidifier rated
up to 0.5 amp can be connected to this terminal with
th ground leg of the circuit being connected to either
ground or the “C” terminal. See Figure 46 for location
of terminal.
1. The power supply wiring must meet Class I restrictions.
Protected by either a fuse or circuit breaker, select circuit
protection and wire size according to unit nameplate.
10.
Install the room thermostat according to the instructions
provided with the thermostat
.
See Table 11 for
thermostat connections
.
If the furnace is being matched
with a heat pump
,
refer to the instruction packaged with
the dual fuel thermostat
.
Thermostat Selection
The unit is designed to operate in a variable rate capacity
mode using a two stage thermostat. This unit will
automatically adjust firing rate based upon thermostat cycle
times.
A Comfort Sync™ thermostat must be used in communicating
applications. Refer to the instructions provided with the
thermostat for installation, set up and operation.
For optimal performance in non-communicating applications,
a thermostat with adjustable settings for 1
st
stage /2
nd
stage on/off differentials and adjustable stage timer is
recommended.
The Following two stage thermostat set-up is recommennded
for optimal variable rate capacity mode:
First heat stage differential set to
1/2
to 1 degree F; second
heat stage differential set to
1/2
or 1 degree F; second heat
stage upstage timer disabled, or set to maximum (1 hr
minimum).
Indoor Blower Speeds
NOTE:
When this unit is used with a Comfort Sync™
thermostat, proper indoor blower speed selections are made
by the communicating thermostat
.
1. When the thermostat is set to “FAN ON”, the indoor
blower will run continuously at 38% percent of the
second stage cooling speed when there is no cooling
or heating demand.
2. When the unit is running in the heating mode, the
integrated control will automatically adjust the blower
speed to match the furnace firing rate. This speed can
be adjusted up or down by 7.5% or 15% using DIP
switches 14 through 16 for the low heat speed and 17
through 19 for the high heat speed.
3. When there is a cooling demand, the indoor blower will
run on the cooling speed designated by the positions of
DIP switches 8 through 11.
NOTE:
The discharge air temperature sensor is intended
to be mounted downstream of the heat exchanger and a
i
r
conditioning coil
.
I
t must be placed in free airflow
,
where
other accessories (humidifiers
,
UV lights etc.) will not
interfere with its accuracy
.
Wiring distance between the
furnace and discharge air sensor should not exceed 10 ft
.
when wired with 18 gauge thermostat wi
r
e
.
Table 10
Summary of Contents for A97DSMV
Page 3: ...507029 03 Page 3 of 68 Issue 1622 A97DSMV Exploded View Figure 1...
Page 13: ...507029 03 Page 13 of 68 Issue 1622 OUTDOOR TERMINATION KITS USAGE Table 3...
Page 24: ...507029 03 Page 24 of 68 Issue 1622 Figure 29...
Page 27: ...507029 03 Page 27 of 68 Issue 1622 Figure 36 Trap Drain Assembly Using 1 2 PVC or 3 4 PVC...
Page 33: ...507029 03 Page 33 of 68 Issue 1622 Figure 43 Typical A97DSMV Wiring Diagram...
Page 34: ...507029 03 Page 34 of 68 Issue 1622 Figure 45...
Page 35: ...507029 03 Page 35 of 68 Issue 1622 Figure 46...
Page 36: ...507029 03 Page 36 of 68 Issue 1622 Figure 47 Integrated Control...
Page 40: ...507029 03 Page 40 of 68 Issue 1622 Low Voltage Field Wiring Table 14 Single Stage 2 Stage...
Page 44: ...507029 03 Page 44 of 68 Issue 1622 BLOWER DATA...
Page 57: ...507029 03 Page 57 of 68 Issue 1622...
Page 58: ...507029 03 Page 58 of 68 Issue 1622...
Page 59: ...507029 03 Page 59 of 68 Issue 1622...
Page 60: ...507029 03 Page 60 of 68 Issue 1622 Configuring Unit Size Codes...
Page 61: ...507029 03 Page 61 of 68 Issue 1622 Troubleshooting Heating Sequence of Operation...
Page 62: ...507029 03 Page 62 of 68 Issue 1622 Troubleshooting Heating Sequence of Operation continued...
Page 63: ...507029 03 Page 63 of 68 Issue 1622 Troubleshooting Heating Sequence of Operation continued...
Page 64: ...507029 03 Page 64 of 68 Issue 1622 Troubleshooting Heating Sequence of Operation continued...
Page 65: ...507029 03 Page 65 of 68 Issue 1622 Troubleshooting Cooling Sequence of Operation...
Page 66: ...507029 03 Page 66 of 68 Issue 1622 Troubleshooting Continuous Fan Sequence of Operation...