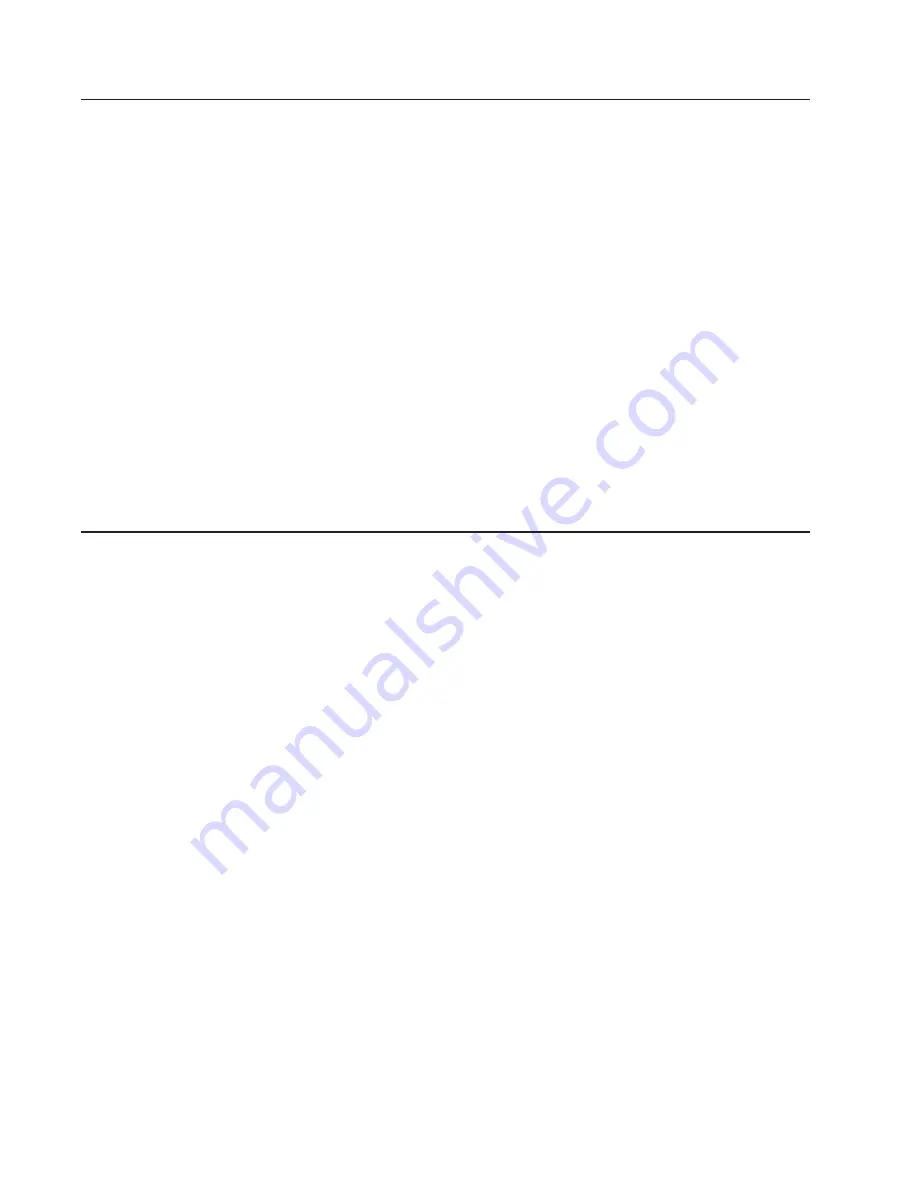
4
B. If automatic control is not used, the use of a hand
switch to control the fan motor has de
fi
nite ad-
vantages. The fan operates continuously during
the heating season. The motors are oil less in all
positions. Current consumption is low – 6 watts
for all AMEF models.
For FSA, VSA Models (See Figs. 3-4 & 3-5)
A. Beware of Voltage Drop. If the wire supplying
current to the humidi
fi
er is too small or too long,
there may be a voltage drop that will reduce the
life of your equipment. When the voltage is too
low, the solenoid valve will not open but current
will continue to
fl
ow and will burn up the coil.
B. 24 Volt Wiring. (VSA Only)
Where codes permit
24 volt wiring without conduit, the use of a 120-24
volt transformer relay, as shown in Fig. 3-5 will
lower the installation cost.
Step 7: Install Pneumatic Piping. (AM)
A. Air
Supply.
Air supply for Armstrong Humidi
fi
ers
should be 15 to 20 psi. This air must be clean and
dry instrument air. Make air connections to fan of
AMAF models.
B. Compressed
Air
Piping.
Plastic tubing or equiva-
lent is used for all air connections.
Step 8: Install Humidity Controller.
Location.
The humidistat should be installed anywhere
from 20 ft. to 30 ft. from the humidi
fi
er – at one side of
the air stream from the humidi
fi
er. The hygrostat should
be able to “see” the unit controlled. It must not be hidden
behind piles of goods or in channels of columns where air
movements cannot reach it. It may be necessary to experi-
ment with the location in order to get the best control.
Setting and Adjusting
should be done in accordance with
the manufacturer’s instructions furnished with the humidi-
stat.
Recommended Option.
A pneumatic or an electric temperature switch is recom-
mended in any system where the steam supply to the
manifold jacket and humidi
fi
er body may be interrupted or
turned off.
Air and Electrical Connections
Sizing and Selection
A survey of your requirements should be taken to deter-
mine the amount of steam needed for humidi
fi
cation, the
number, size and type of units required, and the location of
both humidi
fi
er and humidity controllers.
Sizing and location with natural ventilation.
These are the average industrial humidi
fi
cation applications
with:
Room temperatures – 65° to 80°.
Relative humidities – 35% to 80%.
Natural ventilation – i.e., in
fi
ltration around windows and
doors.
Selection Data Required.
■
Minimum Outdoor Temperature: for most jobs,
fi
gure
10°F above the lowest recorded temperature for your
locality. The lowest temperatures are seldom
encountered for more than a few hours.
■
Indoor Temperature
■
RH Desired
■
Pressure of Steam Available for Humidi
fi
cation
■
Number of Cubic Feet in Room
■
Air Changes Per Hour: air changes taking place under
average conditions exclusive of air provided for
ventilation or regain of hygroscopic materials.
Rooms, 1 side exposed ................... 1
Rooms, 2 sides exposed ................. 1 ½
Room, 3 or 4 sides exposed ............ 2
Rooms with no windows or
outside doors ............................ ½ - ¾
Typical Problem:
Design outdoor temperature ............ 0°F
Indoor temperature .......................... 70°F
RH required ..................................... 40%
Air changes per hour ....................... 2
Steam pressure available ................ 5 psi
Room size 400’ x 160’ with 10’ ceiling.
Natural ventilation
Heated by:
Unit heaters – fan on-off control.
Step 1:
Steam required for humidi
fi
cation. Our room con-
tains (400’ x 160’ x 10’) or 640,000 cu. Ft.
From the 70°F Table 5-1, read across from 0°F outside
temperature to the 40% RH column where you
fi
nd the
fi
gure .409 lbs. of steam per hour per 1000 cu. ft. of space
for each air change. Then, 640 x .409 x 2 equals 524 lbs. of
steam per hour installed humidi
fi
cation capacity required.
Step 2:
Electric or air controlled units. The large
fl
oor area
calls for multiple humidi
fi
ers. No explosion hazard has
been speci
fi
ed so use of air controlled units is not required.
Electric units are recommended.
Step 3:
Number of humidi
fi
ers for job. Divide steam
required by capacity of humidi
fi
ers at steam pressure avail-
able.
Step 4:
What size humidi
fi
er to use. For this example, a
large number of smaller capacity units is recommended.
Larger capacity units could cause condensation on the low
ceiling. Also, because of the large
fl
oor area, the humidi-
stats for fewer units would be widely spaced, which could
result in less accurate control than desirable.