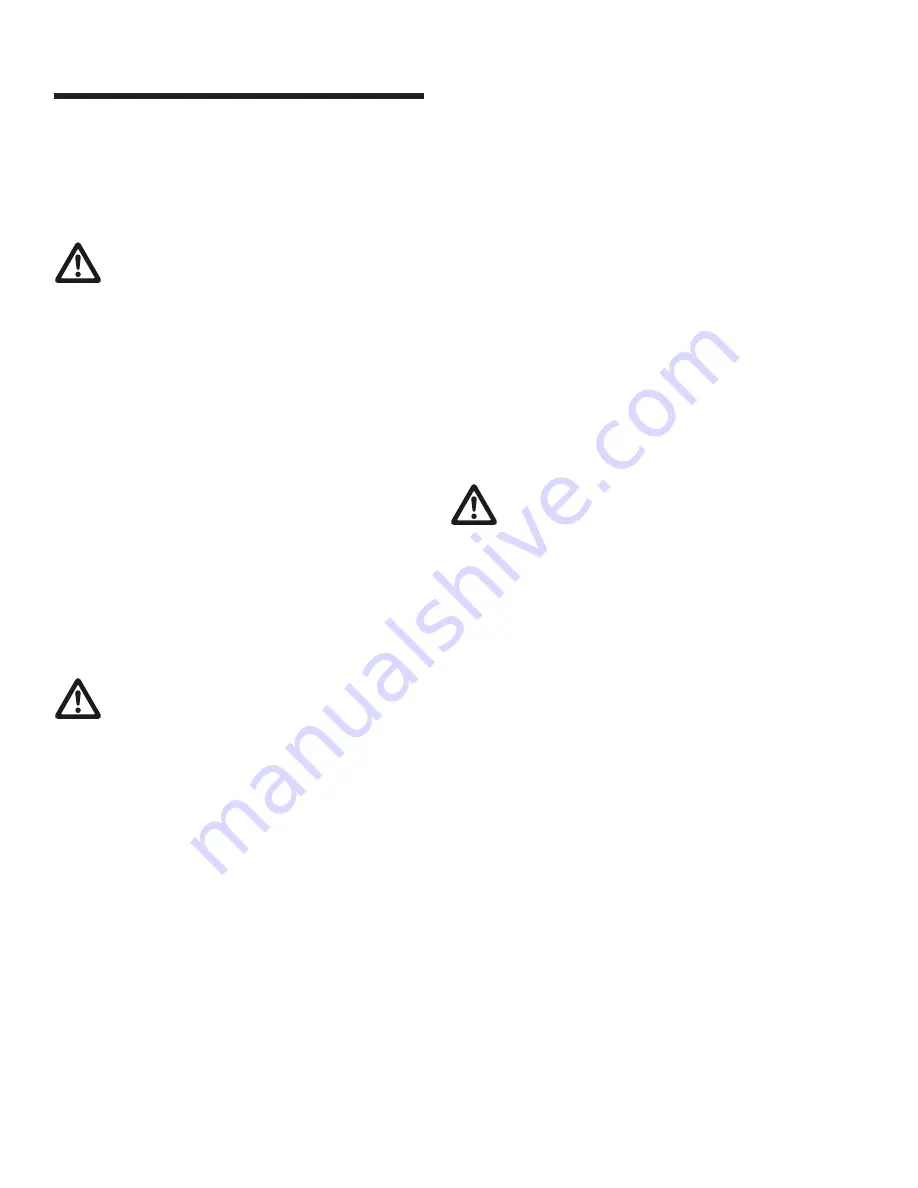
installation &
operating instructions
Design Envelope
4300
&
4380
Vertical In-line Pumping Unit
18
4.0 operation
4.1 start-up checklist
Particular care must be taken to check the following
before the pump is put into operation:
a
Pump primed?
b
Rotation
ok
?
c
Lubrication
ok
?
d
Pipe work properly supported?
e
Voltage supply
ok
?
f
Overload protection
ok
?
g
Is the system clean?
h
Is the area around the pump clean?
Warranty
Does not cover any damages to the equipment resulting from
failure to observe the above precautions. Refer to Armstrong
General Terms and Warranty sheet. Contact your local Arm-
strong representative for full information.
4.2 starting pump
Ensure that the pump turns freely by hand, or with
some gentle mechanical help such as a strap or Allen
key in coupling bolt.
Ensure that all protective guarding is securely fixed in position.
The pump must be fully primed on start up. Fill the pump
casing with liquid and rotate the shaft by hand to remove any
air trapped in the impeller. On split-coupled Design Envelope
units any air trapped in the casing as the system is filled must
be removed by the manual air vent in the seal flush line.
Ensure
entrained air is removed from Design Envelope pumps, prior
to starting, through the air vent on the seal flush line. Open
vent until clear of air.
Design Envelope close-coupled units are fitted with seal flush/
vent lines piped to the pump suction area. When these units
operate, residual air is drawn out of the pump towards the suc-
tion piping. energize the motor momentarily and check that the
rotation corresponds with the directional arrow on the pump
casing (clockwise when viewed from non-drive end of motor).
Start the pump with the discharge valve closed and the suc-
tion valve open, then gradually open the discharge valve when
the motor is at operating speed. The discharge valve may be
cracked
or open slightly at start up to help eliminate trapped air.
When stopping the pump:
Close the discharge valve and
de-energize the motor.
Do not
run the pump against a closed discharge valve at full
speed for an extended period of time (a few minutes maxi-
mum.)
Should the pump be noisy or vibrate on start-up a common
reason is overstated system head. Check this by calculating the
pump operating head by deducting the suction pressure gauge
value from the discharge gauge reading. Convert the result into
the units of the pump head as stated on the pump nameplate
and compare the values. The system designer or operator
should be made aware of this soon as some adjustment may be
required to the drive settings to make the pump suitable for the
system as installed.
Check rotation arrow prior to operating the unit. The
rotation of all Armstrong
4300
&
4380
Vertical
In-Line units is clockwise when viewed from behind
the motor (
nde
).
Summary of Contents for Design Envelope 4300
Page 2: ......