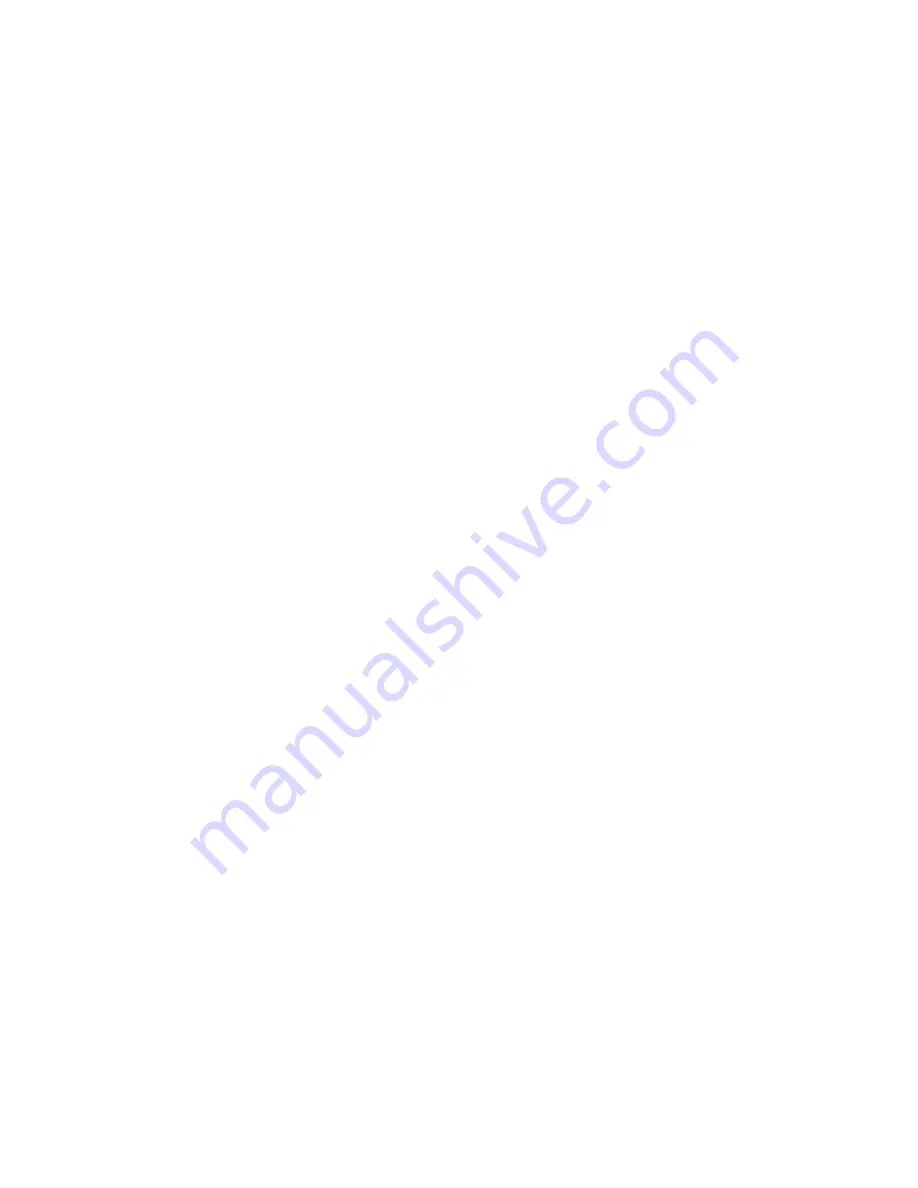
# 44876D006
Page 9
SYSTEM CHECK
Pre-start Check
•
Is unit properly located, level, secure, and service-
able?
•
Has an auxiliary pan been provided under the unit
with separate drain for units installed above a finished
ceiling?
•
Have all webs been carefully removed from the drain
connections that are being used?
•
Has the condensate line been properly sized, run,
trapped, pitched, and tested?
•
Is the ductwork correctly sized, run, taped, and
insulated?
•
Have all cabinet openings and wiring been sealed?
•
Is the indoor coil metering orifice size correct?
•
Is the filter clean, in place, and of adequate size?
•
Has the indoor/outdoor unit application been reviewed
for proper motor dip switch settings?
•
Is the wiring tight, correct, and to the wiring diagram?
•
Is the unit properly grounded and protected (fused)?
•
Is the thermostat correctly wired, level, and in a good
location?
•
Is the unit circuit breaker(s) rotated properly – ON up/
OFF down?
•
Are all access panels in place and secure?
Refer to outdoor unit installation instructions for system
start-up instructions and refrigerant charging instructions.
Airflow
For proper system operation, the airflow through the
indoor coil should be between 350 – 450 CFM per ton of
cooling capacity. Each electric furnace is shipped config-
ured to provide the correct airflow for the maximum
tonnage outdoor unit. If the electric furnace is to be used
with smaller tonnage outdoor equipment, the variable
speed motor must be configured for that application by
field changing the motor control board (refer to the
Appli-
cation Table
on page 7).
Electric Heater
To check the electric heater operation:
1.
Set thermostat to call for auxiliary heat (approximately
5° F above ambient temperature). The indoor blower
and auxiliary heat should come on together. Allow a
minimum of 3 minutes for all sequencers to cycle on.
2.
Set the thermostat so it does not call for heat. Allow
up to 5 minutes for all sequencers to cycle off.