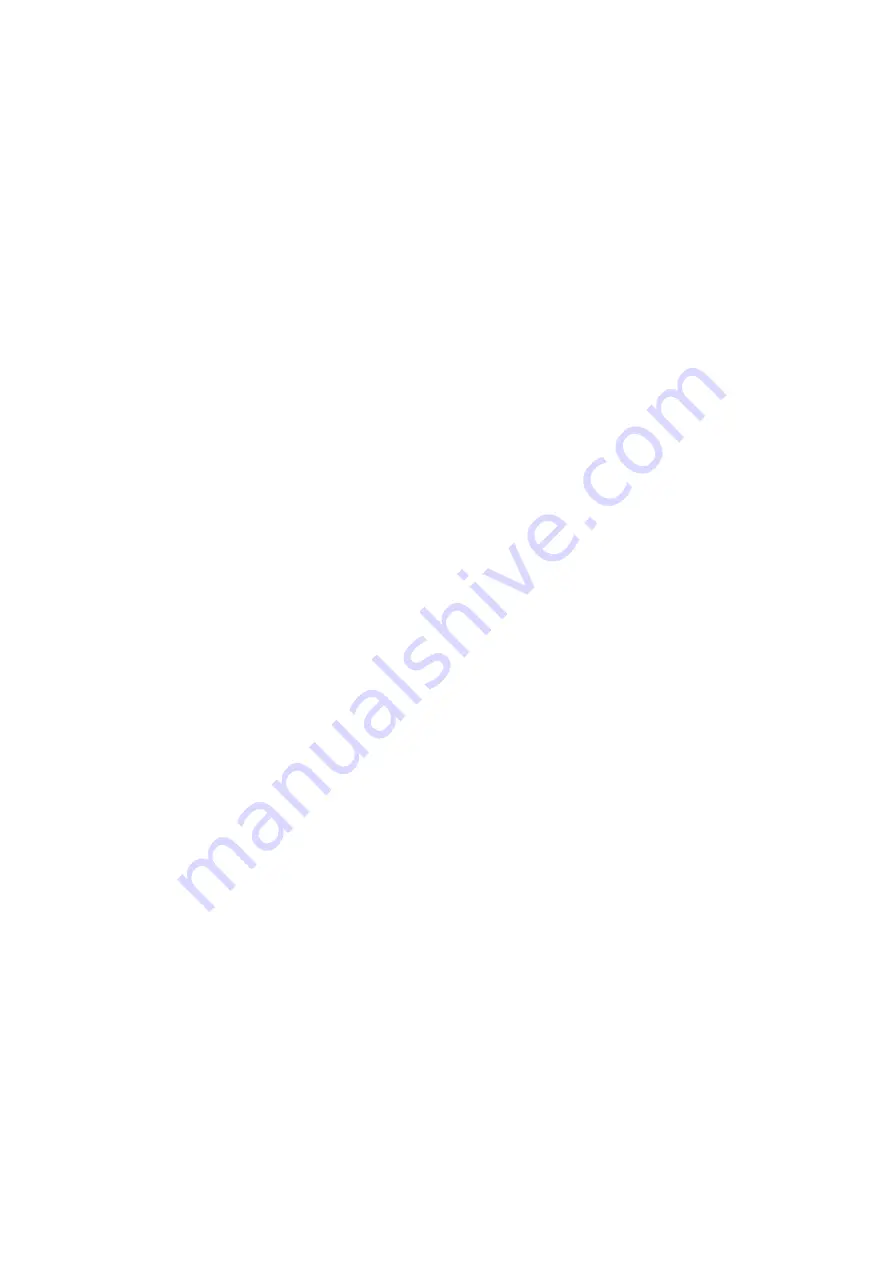
42
Disinfection product recommendations for the EvaPack™ Evaporative Pad
Important : this recommendation is based on our experience. It is of the user’s responsibility to use an
appropriate disinfection method and/or product. In case of doubt, please contact Armstrong to confirm if
the proposed disinfection product/ method is usable on EvaPack™ Evaporative Pad.
For disinfection & anti-mold treatment of the pad, the media must be completely soaked (immerge completely
the cassette) in a chlorine based sterilizer such as sodium hypochlorite (bleach) or sodium percarbonate, by
ensuring that the disinfection time is respected. If the cassette is too big, dismantle it carefully by removing
the rivets, then immerge the EvaPack
™
pad sheets in the disinfection solution and disinfect the cassette frame
separately.
In case of contamination by biofilms of pseudomonas or legionella we recommend to replace pad cassettes
with new ones.
Rinse properly after disinfection.
Please pay attention to toxic chlorine gas if the chlorine based sterilizer is used with an acid solution sterilizer.
For bleach, and other forms of hypochlorite, the water pH must be maintained between 7.6 and 7.2, for maximal
desinfection efficiency and action against algae.
Recommended free water chlorine dosage:
Continous treatment:
0.1
-
4.0
mg/l
(ppm)
(In US EPA, MRDL (Maximum Residual Disinfectant Level) for drinking water is 4.0 PPM or mg/l)
Shock treatment:
2.0
-
5.0
mg/l
(ppm)
(WHO (World Health Organization) stated free chlorine concentration in the city water should be below 5 PPM or mg/l)
.
It is of the user’s responsibility to respect limit chlorine air concentration, established to avoid the risk of
irritating effects. This limit is given by the Environment / Health State Agencies of user’s Country.
To calculate the air concentration of free chlorine (PPM
v
):
PPM
v
= mg/m
air
³ * (0.082057338 * (dbt
air
ºC + 273)) / 70.9
(with dbt
air
ºC : oulet dry bulb air temperature in ºC)
.
To calculate mg/m
air
³ of chlorine from inlet water chlorine concentration (
[Chlorine]
water
):
mg/m
air
³
= [Chlorine]
water
(mg/l) * evaporated waterflow rate (l/h) / airflow rate (m
3
/h).
Example: at 25ºC, Chlorine air concentration of 1 PPM
v
= 2.9 mg/m
air
³
Standard EvaPack™ metal frames are in stainless steel.
However, Please pay attention to metal frame, basin corrosion risk.
Chlorides (mg/l):
[Chloride]
water
≤
250 mg/l
Sulphates ( mg/l)
[Sulphate]
water
≤
250 mg/l
Rinse properly after disinfection
.
All EvaPack™ parts can be dismantled for easy cleaning.
Summary of Contents for EvaPack Series
Page 46: ...46 Notes...
Page 47: ...47 Notes...