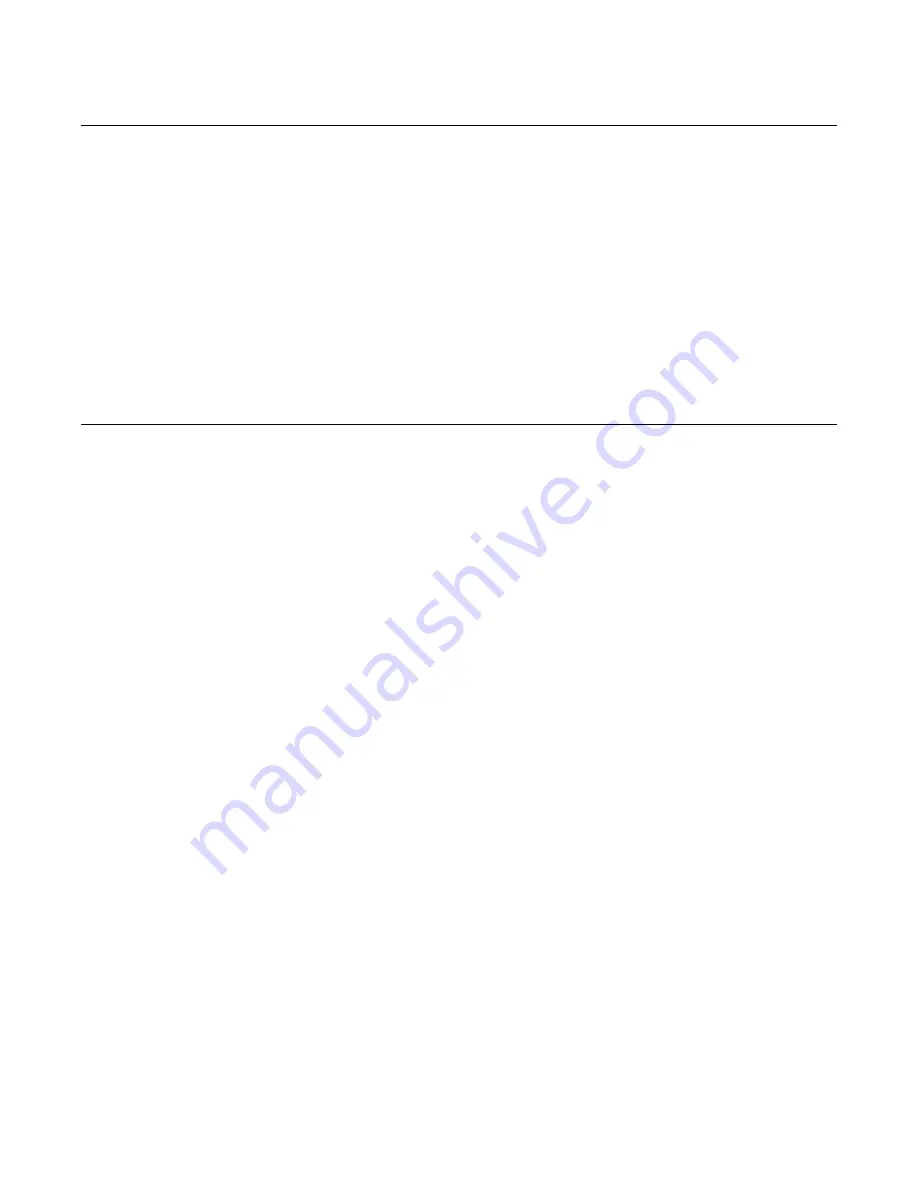
Removing the Tank, HC-6100/6300 Only
1. Operate menu to "MANUAL DRAIN" and allow unit to complete a deep drain.
(
Caution:
Tank will still be quite warm).
2. Turn off circuit breaker.
3. Unlock and open front and side doors. Remove left side panel.
4. Disconnect 3 hoses from front of tank; rubber hose cuff at steam outlet; heating element leads at
contactor, fuses, or power module; and thermocouple wires.
5. Loosen and remove 2 mounting bolts at the bottom of tank. Slide tank out left side of cabinet
(be sure tank had time to cool after operation).
Troubleshooting
Notice:
This troubleshooting guide is offered to aid in servicing the HC-6000 humidifiers. It is intended
for use by electricians and technical service personnel familiar with electrical and electronic equip-
ment. Many steps in the troubleshooting procedures require measurements of high voltages and
involve working near exposed live parts.
KNOW WHERE THE HIGH VOLTAGE PARTS ARE, AND
KEEP HANDS AND METAL TOOLS AWAY FROM THEM.
All resistance checks should be made with
main power OFF and the component disconnected from wiring. All continuity checks should be made
with main power OFF. If unsure concerning any of the following procedures, PLEASE consult the
Armstrong Humidification Group at Phone: (269) 273-1415.
Humidifier will not fill with water when power is applied.
1. Make sure the status in menu is "Steam Gen.".
2. Make sure "STATE" LED is red. If so, refer to MAINTENANCE or DIAGNOSTICS section of
this manual.
3. Make sure "POWER" LED is lit. If not, check voltage at secondary side of the main power
transformer. Voltage should be 24-28 VAC. No or low voltage is an indication of a problem with the
supply voltage or transformer. Verify supply voltage and make sure it is the same as voltage rating
on humidifier nameplate. Check secondary power fuses.
4. Check the voltage to the fill valve. Voltage should be 24-28VAC (voltage should be taken with
wires connected). If voltage is present, fill valve solenoid coil is probably defective. Coil resistance
should be 18
Ω
(8.3
Ω
for HC-6500/6700) with wires disconnected.
5. Check for water in cabinet bottom or in fill cup overflow line. If present, see "Water in bottom of
cabinet" on page 24.
6. If no voltage is present to fill valve, check water level. If it is above 2/3 full in electrode level
canister (float canister for DI units), the drain valve has to open to drain water below high water
level before the fill valve is energized.
7. Check for 24-28 Vac power to drain valve (voltage should be taken with wires connected). If power
to drain valve is OK, check drain valve coil resistance with wires disconnected. It should be
approximately 10
Ω
(8.3
Ω
HC-6500/6700).
22
Summary of Contents for HumidiClean HC-6100 Series
Page 28: ...HC6100 Wye Wiring layout 28...
Page 29: ...HC6100 Delta Wiring layout 29...
Page 30: ...30 HC6100 PAR Single Phase Wiring Layout...
Page 31: ...HC6300 Wye Wiring layout 31...
Page 32: ...HC6300 Delta Wiring layout 32...
Page 33: ...HC6500 Wye Wiring layout 33...
Page 34: ...HC6500 Delta Wiring layout 34...
Page 35: ...35 HC6500 WYE 2 contactors Wiring Layout...
Page 36: ...36 HC6500 Delta 2 contactors Wiring Layout...
Page 37: ...HC6700 Wye Wiring layout 37...