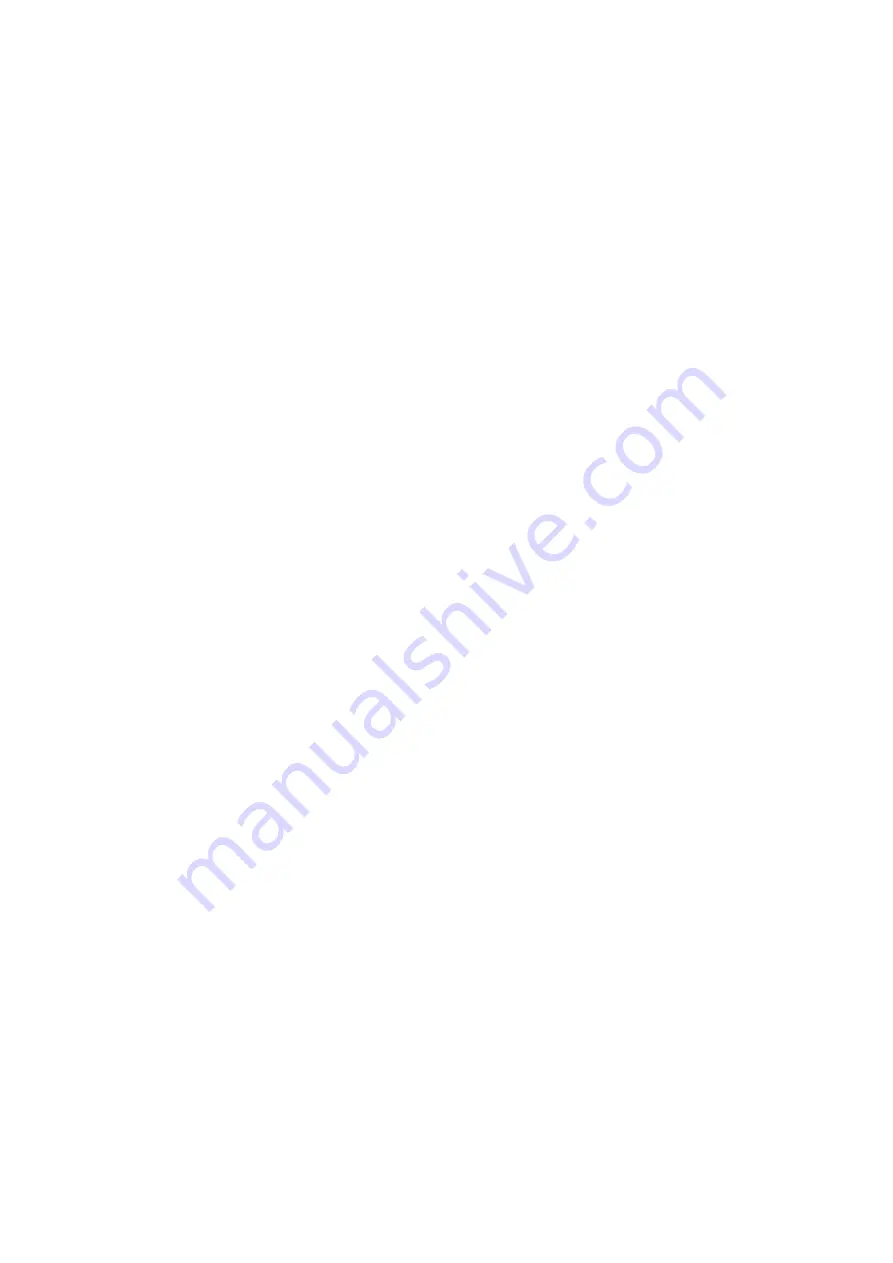
3
Table of Contents
1
User Advisory
/ Application Requirements
………………………………………………
.
4
2
For your safety
………………………………………………………………………………
5
3
Functions Head
/ Connectors
…
.
…………………………………………………………
..
7
4 Remote
Head Setup
/ Top Down, Home Position,Tilt Lock
……
..
………………
.
………
9
5
Camera Setup /
Mounting the Camera / Balancing the Camera
……
..
…
..
……
..
……
..
10
6
Power Supply
/ Recommended Batteries / Wiring
………………
..
……………………
.
12
7
Remote Control
Setup
/ Connecting / Emergency Shut Off / Mounting Position
……
.
13
8
Remote Control GUI
………………………………………………………………………
..
14
9
PID
Setup
/ Quick Setup / PID Fine Trim / Drop
…………………………………………
.
15
10
Controls Setup
/ Changing profiles / Auto Assignment / Manual Assignment /
Available Controllers / Changing Directions / Speed / Ramp / Default Position /
True Horizon / Endstops / Follow
…………………………………………………………
18
11
Additional Controls Setup
/ Deadband / Sensitivity / Ramp Mode / Filter / Ratio
…
20
12
Remote Head Setup /
Pan Motor On/Off / Motor Mode / Endstops / Follow / True
Horizon / High Dynamic Mode / Mounting Position
………………………………………
.
22
13
Wireless
Setup
/
Channels / Regions / Range ..
…………………………………………
.
25
14
FIZ Setup
Assigning / Assignable Controllers / Calibration / Torque / Mode / Speed /
Fine Trim
………………………………………………………………………………………
28
15
Info & Service
Factory Defaults / Joystick Calibration / Sensor Calibration
…………
..
31
16
Profile Management
……..…………………………………………………………………
42
17
Power Disconnection
………………………………………………………………………
43
18
Dimensions
…………………………………………………………………………………
..
43
19
Pinout
…………………………………………………………………………………………
.
44
20
Assignable Controllers & Functions
..
…………………………………………………
..
45
21
Declaration of Conformity
…………………………………………………………………
46
Table of Contents