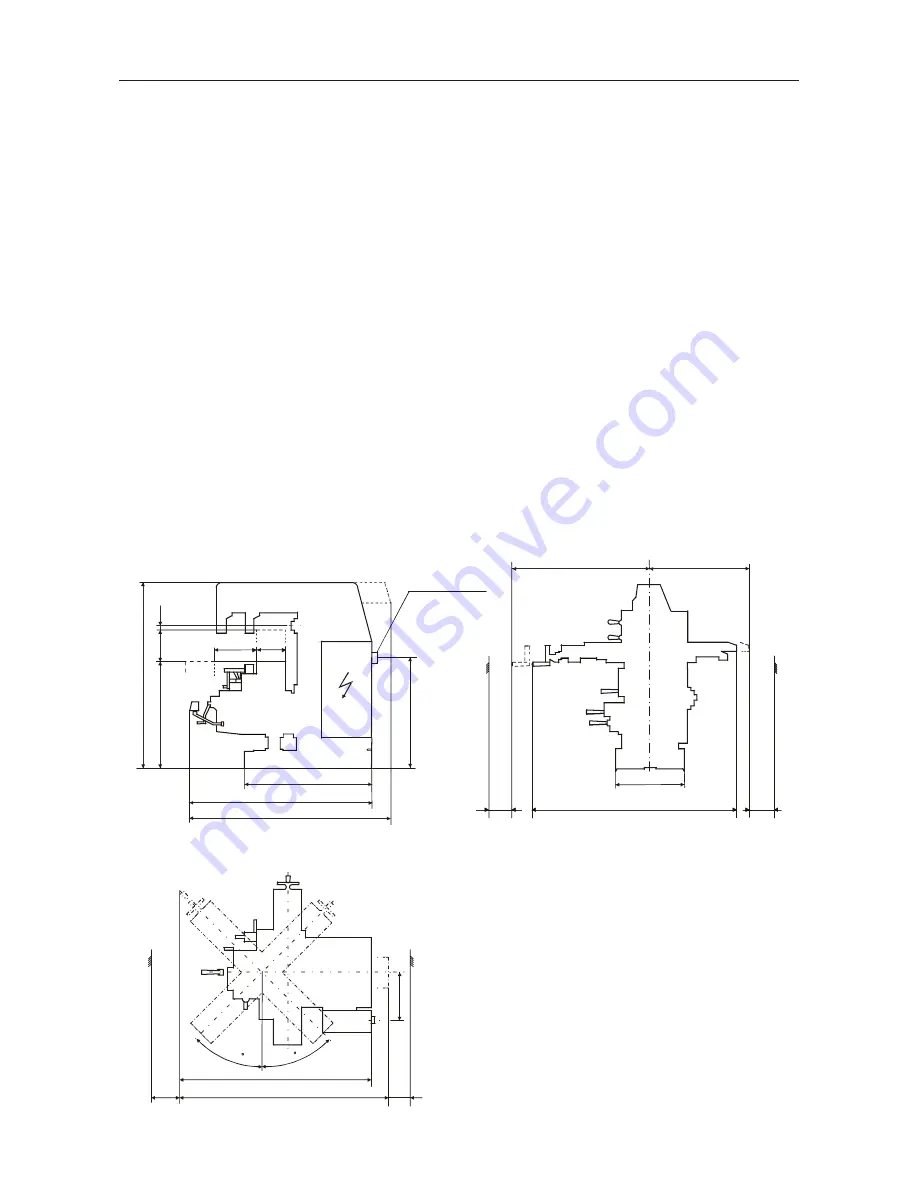
OPERATING AND MAINTENANCE MANUAL FU 321M
9
Install the machine on stable and flat concrete floor and if necessary use addi-
tional pads including vibroinsulating pads, or place concrete. If the floor is un-
stable, install the machine on a concrete foundation / Fig.2 /. Machine base has
holes for the foundation bolts, by which machine can be fixed at special situa-
tions. The dimension H depends on the bearing capacity of the soil, but it should
be minimum 350 mm.
After final curing of the concrete, tight the nuts of foundation bolts (if used), as
continuously observe and keep not to disturb the horizontal leveling of the ma-
chine. Then fill the space between the machine and the foundation with a mixture
of sand and cement.
Fondation bolts, nuts and the leveling plates are not delivered by the producer.
NOTE:
The use of vibration insulating supports is allowed if the soil is hard
enough. Foundation bolts, nuts and wedges are not supplied by the manufacturer.
MACHINE DIMENSIONS
3150
2450
1300
360
320
500
720
2090
500
1635
1455
500
500
2665
3310
45
45
30
40
6
940
10
78
1080
30
6
Е
l. conection point
Summary of Contents for FU 321M
Page 32: ...OPERATING AND MAINTENANCE MANUAL FU 321M 29 ELECTRIC EQUIPMENT DETAILS...
Page 33: ...OPERATING AND MAINTENANCE MANUAL FU 321M 30 ELECTRIC ARRANGEMENT...
Page 34: ...OPERATING AND MAINTENANCE MANUAL FU 321M 31 BUTTON ARRANGEMENT FRONT PANEL 10...
Page 35: ...OPERATING AND MAINTENANCE MANUAL FU 321M 32 BUTTON ARRANGEMENT SIDE PANEL WARNING...
Page 39: ...OPERATING AND MAINTENANCE MANUAL FU 321M 36 Fig 3a 45 41 46 51 48 43 52 44 42 53 49 50 47...
Page 40: ...OPERATING AND MAINTENANCE MANUAL FU 321M 37 SEMI AUTOMATIC CYCLE...
Page 43: ...OPERATING AND MAINTENANCE MANUAL FU 321M 40 Fig 6 1 2...
Page 46: ...OPERATING AND MAINTENANCE MANUAL FU 321M 43 Fig 10 4 3 2 1...
Page 52: ...OPERATING AND MAINTENANCE MANUAL FU 321M 49 Fig 16 3 ELECTRIC CIRCUIT DIAGRAM...
Page 57: ...OPERATING AND MAINTENANCE MANUAL FU 321M 54 Fig 18 3 4 1 2 1 1 1 1 1 1 7 5 6 1 1...
Page 60: ...OPERATING AND MAINTENANCE MANUAL FU 321M 57 Fig 21 OPERATOR S WORKING POSITION ON THE MACHINE...
Page 62: ...OPERATING AND MAINTENANCE MANUAL FU 321M 59 Fig 23 MARKING ON THE PACKING 2170 2370...
Page 63: ...OPERATING AND MAINTENANCE MANUAL FU 321M 60 Fig 24 DIGITAL READOUT SYSTEM...