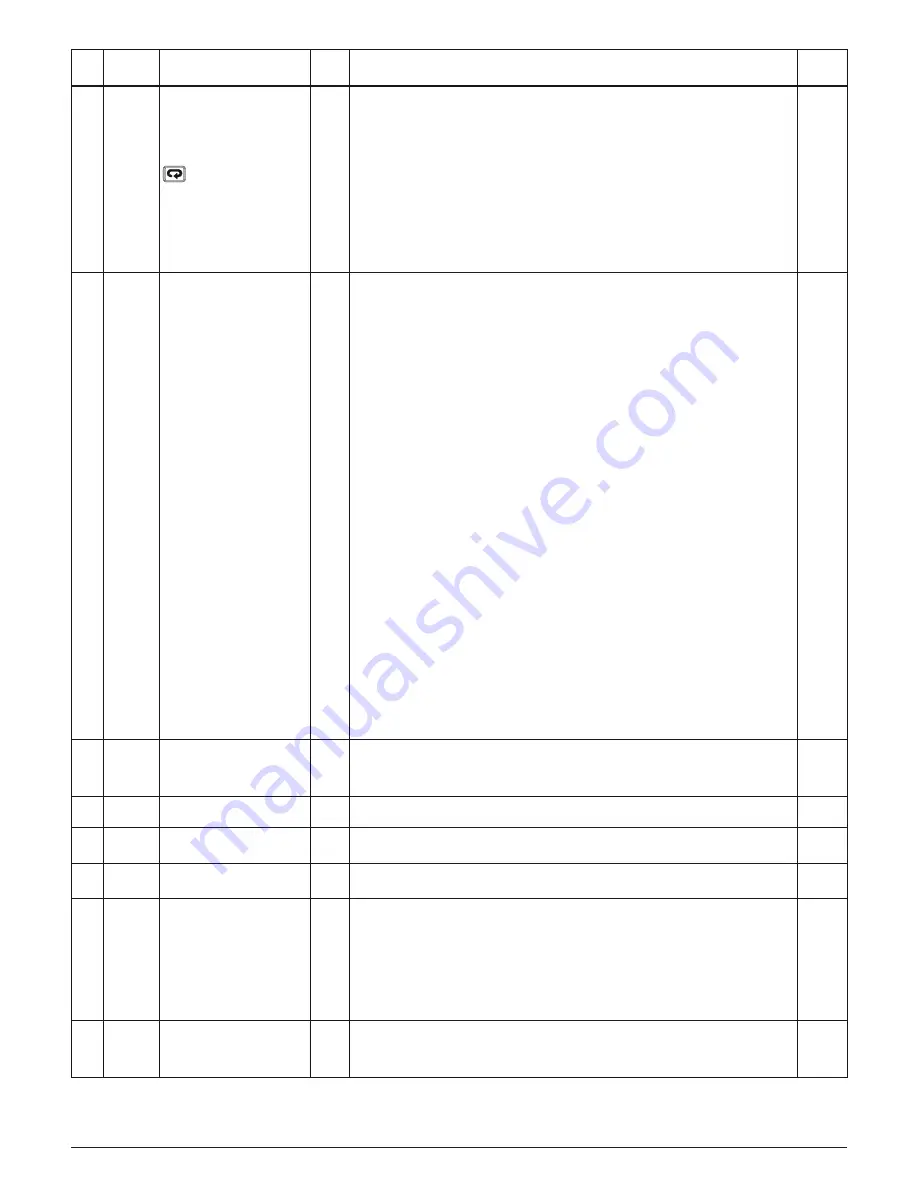
Ascon Tecnologic - KX Line - ENGINEERING MANUAL -Vr.4.0
PAG. 38
no. Param.
Description
Dec.
Point
Values
Default
120 uSrb
button function dur-
ing RUN TIME
nonE = No function
tunE = Auto-tune/self-tune enabling. A single press (longer than 1 second)
starts the auto-tune
oPLo = Manual mode. The first pressure puts the instrument in manual mode
(OPLO) while a second one puts the instrument in Auto mode
AAc = Alarm reset
ASi =
Alarm acknowledge
chSP = Sequential set point selection
St.by = Stand by mode. The first press puts the instrument in stand by mode
while a second one puts the instrument in Auto mode.
Str.t =
Timer run/hold/reset
P.run = Program run
P.rES = Program reset
P.r.H.r = Program run/hold/reset
tunE
121 diSP
Display management
nonE = Standard display
Pou =
Power output
SPF = Final set point
Spo =
Operative set point
AL1 =
Alarm 1 threshold
AL2 =
Alarm 2 threshold
AL3 =
Alarm 3 threshold
Pr.tu = - During a soak, the instrument shows the soak elapsed time;
- During a ramp the display shows the operative set point. At the end
of the program execution, the instrument will show “P.End” messages
alternately with the measured value.
- When no program is running, the instrument shows the standard
display
Pr.td = - During a soak, the instrument shows the soak remaining time
(count down).
- During a ramp the display shows the operative set point. At the end
of the program execution, the instrument shows “
P.End
” messages
alternately with the measured value.
- When no program is running, the instrument shows the standard
display.
P.t.tu = When the programmer is running, the display shows the total elapsed
time. At the end of the program execution, the instrument shows
“
t.End
” messages alternately with the measured value.
P.t.td = When the programmer is running, the display shows the total remaining
time (count down). At the end of the program execution, the instrument
shows “
P.End
” messages alternately with the measured value.
ti.uP = When the timer is running, the display shows the timer counting up.
At the end of the counting, the instrument shows “
t.End
” messages
alternately with the measured value.
ti.du = When the timer is running, the display shows the timer counting
down. At the end of the counting, the instrument shows “
t.End
”
messages alternately with the measured value.
PErc = Percent of the power output used during soft start (when the soft
start time is equal to infinite, the limit is ever active and it can be
used also when ON/OFF control is selected)
0
122 di.cL
Display colour
0 = The display colour is used to show the actual deviation (PV - SP)
1 = Display red (fix)
2 = Display green (fix)
3 = Display orange (fix)
0
123 AdE
Deviation for display
colour management
1... 999 (E.U.)
5
124 di.St
Display Timeout
2
- oFF (display always ON)
- 0.1... 99.59 (mm.ss)
oFF
125 fiLd
Filter on the displayed
value
1
- oFF (filter disabled)
- From 0.0 (oFF) to 20.0 (E.U.)
oFF
126 bG.F
Bar graph Function
0
nonE = Bargraph not lit
Pou =
PID Output power (single action: 0... 100%, double action: -100... +100%)
Po.h = Energy Used (kWh)
Pr.tu = Elapsed time of the program in execution
Pr.td = Time to end of the program in execution
Pr.tS = Time to end of the program segment in execution
ti.uP = Elapsed time of timer (T1 and T2)
ti.du = Time to end of timer (T1 and T2)
r.iSP = Time to preventive maintenance
127 dSPu
Instrument status at
power ON
AS.Pr = Starts in the same way it was prior to the power down
Auto = Starts in Auto mode
oP.0 = Starts in manual mode with a power output equal to zero
St.bY = Starts in stand-by mode
AS.Pr