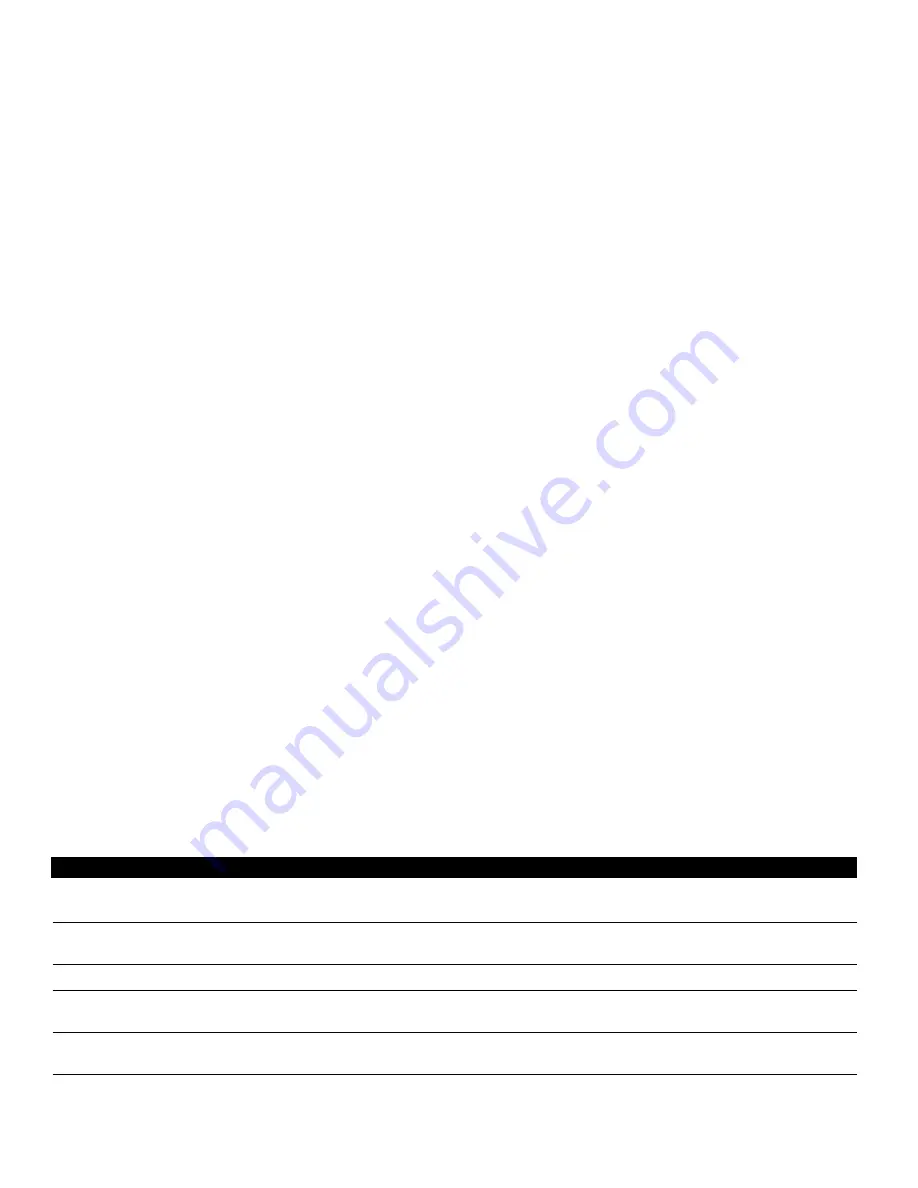
Page 3
Maintenance and Servicing Instructions
Cleaning and Lubrication
Exposed surfaces of the AA-75CF should be disinfected with a commercial dental disinfectant.
Abrasive cleaning agents have the potential to damage surface finishes and should be avoided. To
minimize the risk of corrosion do not use chlorinated solvents to clean either the inside or the
outside of the compressor valves, the air storage tank or the aftercooler assembly.
Lubrication of AA-75CF compressor components is unnecessary. The compressor uses sealed
bearings and Teflon cylinder technology to eliminate the need for lubrication. The cooling fans
similarly use sealed bearings.
Performance verification
To verify proper compressor function, make sure the tank gauge pressure is at zero, the tank drain
valve is closed and the pressure switch is in the OFF position. Plug the compressor into the power
source. Switch the pressure switch to the AUTO position. The compressor should charge the air
storage tank and the intake and aftercooler fans should run. Confirm that compressor shut off
occurs at approximately 105 psi. Open the tank drain valve. When gauge pressure in the tank drops
below 70 psi, the compressor should restart. Allow the tank to drain until all significant water is
removed. Once the air exiting the tank is dry to the touch, close the tank drain valve. When
compressor cuts off, verify that the fans continue to run for approximately two minutes and that the
tank pressure remains constant near 100 psi. A 5 psi drop can be expected after cut off. Listen for
leaks at pneumatic system connections. If leaks are indicated by pressure loss but are not audible,
check the seals with a soap test. A water-liquid detergent solution should be applied to the circum-
ference of the joint. A leak at a seal will cause the solution to bubble. Tighten the joint, if necessary
reapply Teflon tape, until bubbles no longer appear.
Inspection
The felt media of the air intake filters requires periodic inspection and replacement. Initial inspec-
tion is recommended after 500 hours. Afterwards a service duration should be determined based on
the operating conditions. Excessive felt contamination can reduce compressor output and may affect
service life.
Initial compressor inspection is recommended at 2,000 hours. The wear of the rider ring is an indica-
tion of the general condition of the compressor rings. To inspect the rider rings, remove the
compressor from the case as per Compressor Removal instructions, then disassemble the
compressor cylinder heads. If the rider ring measures 0.055 in. or less, an overhaul should be
performed by installing a Service Kit. See the Compressor Motor Service Kit Installation subsection
of the Disassembly, Repair, Replacement, Reassembly and Check Out Section of this manual for
detailed installation procedures.
Troubleshooting
Symptom
Problem
Action
System non-operational
Main breaker tripped
Reset main breaker
Pressure switch contacts corroded
Replace switch
Compressor motor not running
Main breaker tripped
Reset main breaker
Thermal overload tripped
Allow several minutes to cool and restart
No duplex outlet power
Circuit breaker tripped
Reset duplex breaker
Tank pressure exceeds 110 psi.
Pressure switch settings altered
Readjust according to Pressure Switch
Replacement section note
Compressor attempts to restart under load
Leaking or obstructed check valve
Disassembly and clean or replace.
Misaligned unloader valve
Tighten unloader valve screw and realign.
Extended compressor cycle time
Air demand has been altered
Readjust instruments
Clogged intake filters.
Clean or replace.
Air line leaks.
Tighten couplings, retape.
Water collected in air storage tank.
Blow off tank