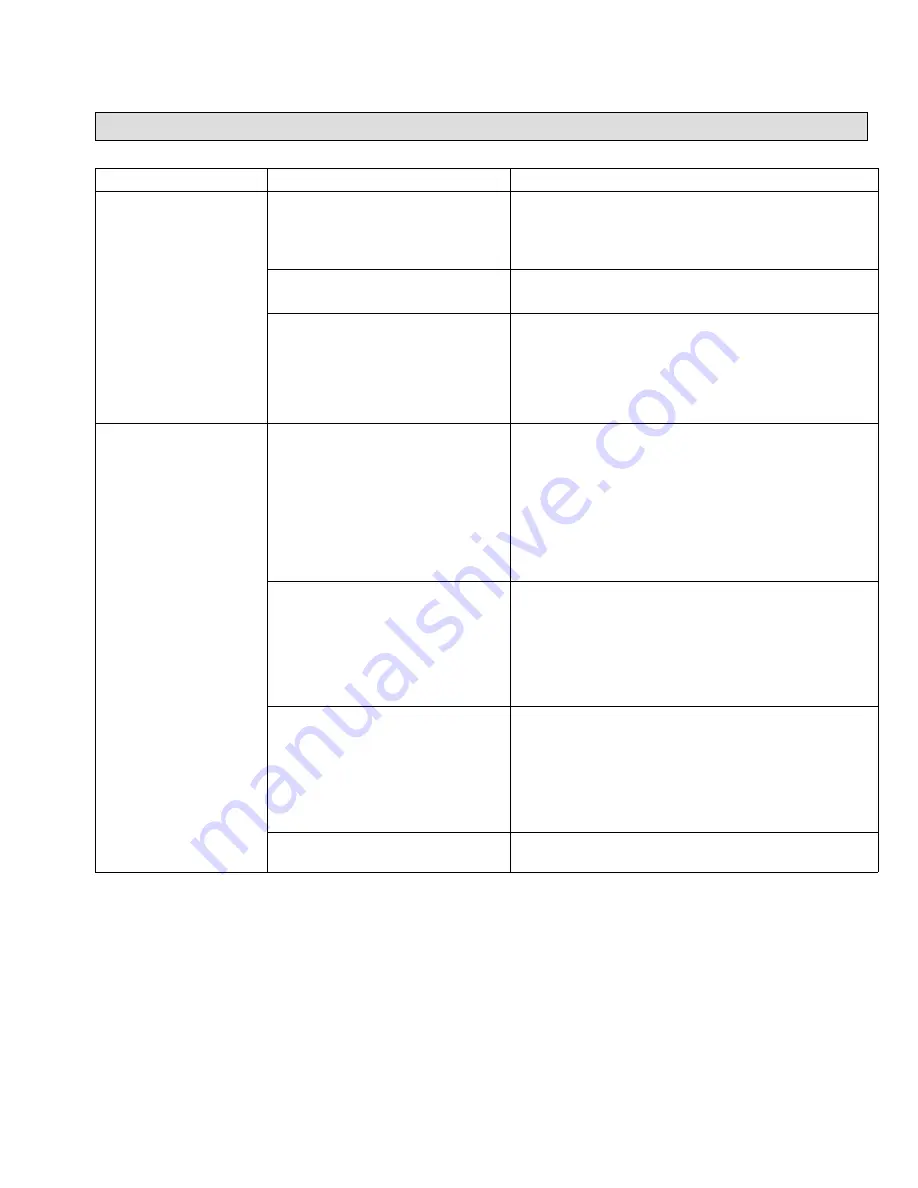
309884
25
Advanced Troubleshooting
General Problem: Motor Does Not Operate (continued)
SPECIFIC PROBLEM
CAUSE
SOLUTION
Basic Electrical Problems
(Continued)
Motor armature is shorting.
Check for shorts using armature tester (growler), or perform
spin test (see
Motor Diagnostics
on page 32). If shorts are
evident, replace motor using
Motor Kit
245063.
Control board fuse is blown.
Replace fuse 119276.
Control board is damaged.
CAUTION:
Do not perform control
board diagnostics until you have
determined that the armature is good.
A bad motor armature can burn out a
good control board.
See
Control Board Diagnostics
on page 32, and replace
control board if damaged using
Control Board Kit
243228.
Sprayer Wiring Problems
NOTE:
Remove right
enclosure mounting
screws, and pull right
enclosure away from drive
housing.
Take care to not
pull on the leads from
the electrical cord and
the Power switch (B).
Sprayer electrical cord is damaged.
Unplug sprayer electrical cord. Disconnect black electrical
cord wire at Power switch (B), and unplug in-line connection
of white electrical cord wire. Plug in electrical cord, and test
voltage between black and white electrical cord wires.
Meter must read 85 to130 Vac.
Replace electrical cord if no voltage.
Sprayer power switch (B) is damaged.
Unplug sprayer electrical cord. Disconnect black control
board wire at Power switch (B), and unplug in-line
connection of white electrical cord wire. Plug in electrical
cord, turn Power switch ON, and test voltage between open
terminal of Power switch and white electrical cord wire.
Meter must read 85 to130 Vac.
Replace Power switch (B) if no voltage.
Thermal overload cutoff switch is
damaged.
See
Startup Hazard After Thermal
Overload
in the WARNINGS section
on page 4.
Unplug sprayer electrical cord. Remove motor harness from
control card, and check for continuity between yellow leads
of motor harness. If thermal relief switch is open (no
continuity), allow motor to cool. If switch remains open after
motor cools, replace motor using
Motor Kit
245063.
If thermal relief switch closes after motor cools, find and
correct cause of overheating.
Terminals are damaged or loose.
Replace any damaged terminals, and make sure all
terminal connections are tight.