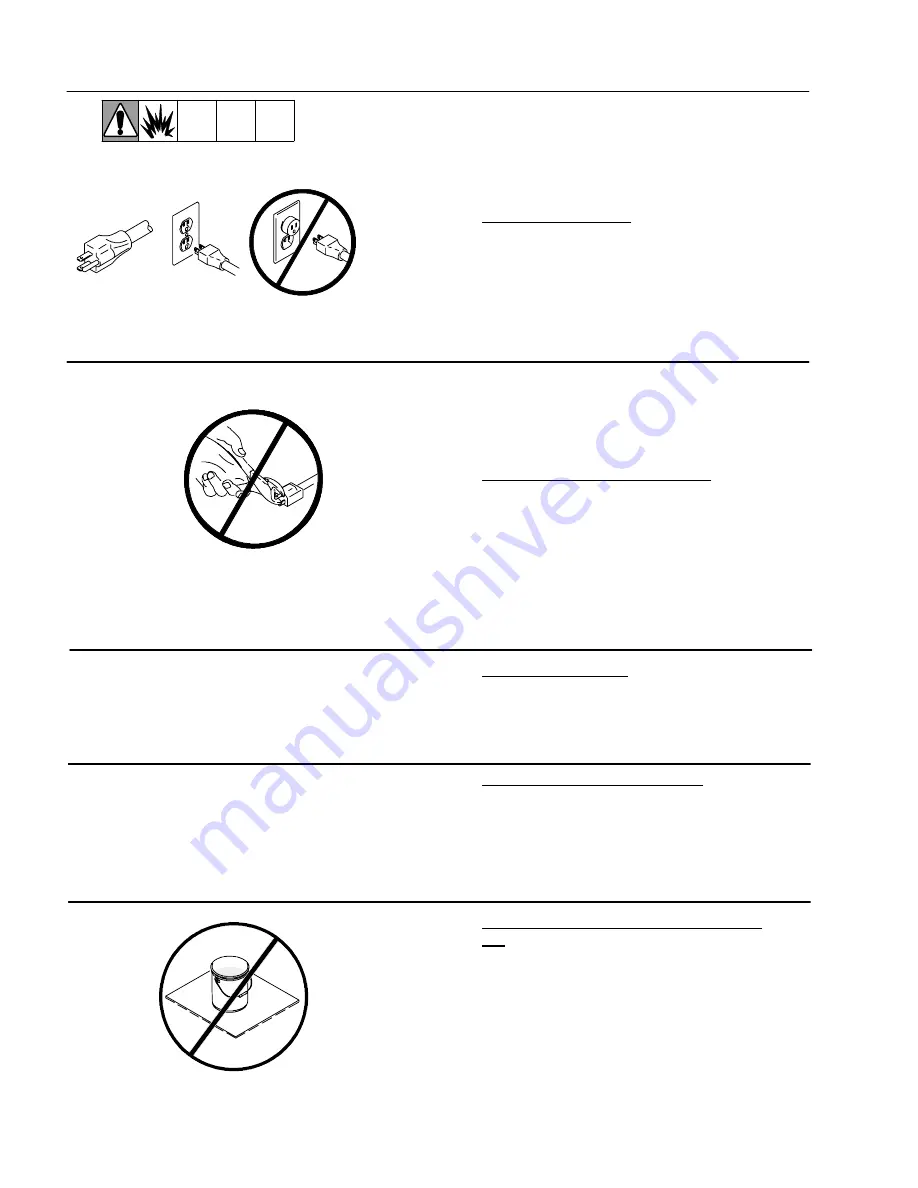
6
309902
D
The sprayer requires
a 120V AC, 60 Hz, 15A
circuit with grounding receptacle. Never use
an outlet that is not grounded or an adapter.
D
Do not use the sprayer if the electrical
cord has a damaged ground prong.
Only use an extension cord with an
undamaged, 3--prong plug.
D
Recommended extension cords
for
use with this sprayer:
D
25 ft (7.6 m) 18 AWG
D
50 ft (15.2 m) 16 AWG
D
100 ft (30.5 m) 14 AWG
D
150 ft (45.7 m) 12 AWG
Smaller gauge or longer extension cords
may reduce sprayer performance.
Grounding and Electric Requirements
D
Ground sprayer gun
through connection to
a properly grounded fluid hose and pump.
D
Ground fluid supply container.
Follow local code.
D
Ground solvent pails used when flush-
ing
. Follow local code. Use only conduc-
tive, metal pails, placed on a grounded
surface such as concrete. Do not place the
pail on a non--conductive surface such as
paper or cardboard, which interrupts the
grounding continuity.
ti5850a
ti5572a
The sprayer must be grounded. Grounding reduces the risk of static
and electric shock by providing and escape wire for the electrical
current due to static build up or in the event of a short circuit.
ti3001b