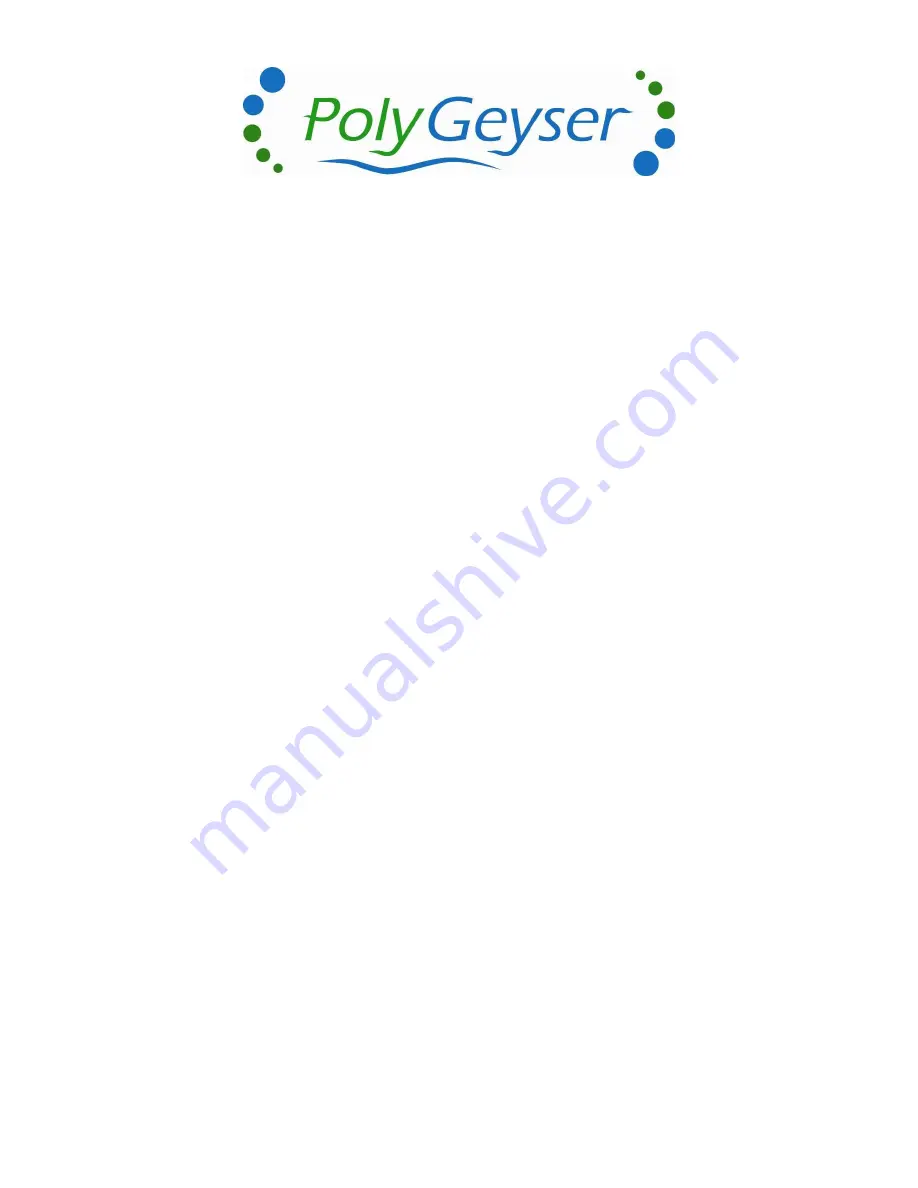
2
Introduc
�
on to the HPPG Series
The High Pressure
PolyGeyser
®
(HPPG) b
ead fi
lter series is the newest add
i�
on to Aquaculture Systems
Technologies’ line of bead
fi
lters. Patented ( U.S. Patent #9,227,863
Patent Pending , European
Patent #0977713B & Canadian Patent #2,287,191) fully exploits the bio
fi
lm protec
�
on provided by our
Enhanced Nitri
fi
ca
�
on (EN) Bead Media in a durable
fi
berglass hull. Designed as “bioclari
fier
s” capable
of performing both biological and mechanical
filtr
a
�
on,
PolyGeyser
®
Bead Filters are capable of handling
biological loads 50% to 100% higher than our Bubble Bead or Propeller Bead Filters equipped with
standard bead media. Addi
�
onally, the
PolyGeyser
®
Bead Filters are virtually immune to clogging and
caking, since they are backwashed pneum
a�cal
ly at a high frequency. These High Pressure
PolyGeyser
®
(HPPG) Bead Filters recycle their own backwash waters. The HPPG
fi
lters are the bioclari
fier
of choice
for commercial aquaculture and wastewater applica
�
ons dealing with high organic loads.
Opera
�on
The
PolyGeyser
®
Bead Filter stands apart from AST’s other Bead Filter technologies primarily through its
autom
a�c p
neuma
�c
backwash mechanism. Water is introduced below the bed of packed EN bead
media and travels upward through the
fi
ltra
�
on chamber where mechanical and biological
fi
ltra
�
on
takes place. Simultaneously, air is slowly introduced into the air charge chamber at a constant,
predetermined rate to achieve the desired backwash frequency. Once the charge chamber has reached
capacity, the pneuma
�
c trigger
fi
res, releasing the entrained air from the charge chamber below the
media bed. The sudden release of air from the charge chamber causes the beads to mix, roll and “drop”
as the air agitates the beads.
The circula
�
on pump/airli
�
operates con
�
nually, which ensures that the
filte
r chamber begins re
fi
lling
immediately a
�
er each backwash event. This causes the beads to
fl
oat upward and reform as a bed.
During the recharge cycle (a few hours), suspended solids in the trapped backwash waters se
�
le into the
sludge storage chamber for later disposal via the sludge drain valve (usually every 3 days- 1 week). At
the same
�
me, the clari
fi
ed backwash waters are passed slowly through the bead bed again elimin
a�
ng
any backwash water losses.
The elimina
�
on of water loss associated with backwashing is a key element in this new technology. In
most applica
�
ons, dozens of backwash sequences can be autom
a�cal
ly executed before sludge removal
is required. There is no water loss associated with the backwash process and the water loss associated
with sludge drainage is negligible. This strategy is pa
r�c
ularly advantageous for marine systems, where
the loss of saltwater must be minimized.